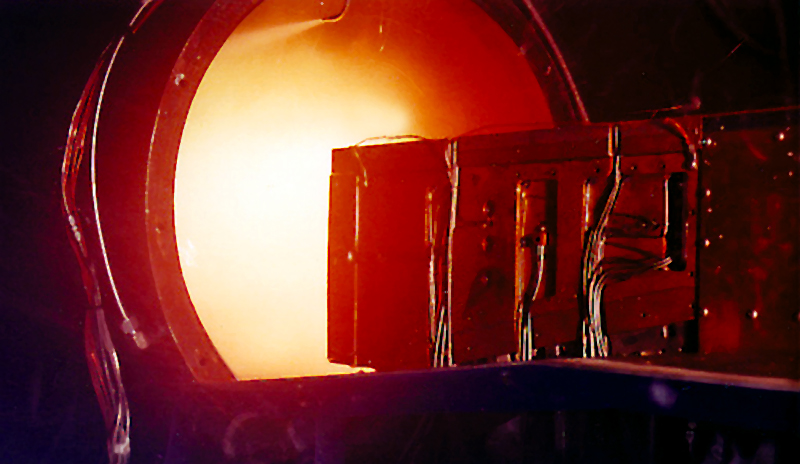
Polyimide Boosts High-Temperature Performance
Originating Technology/NASA Contribution
Polyimides are a class of polymers notable for chemical, wear, radiation, and temperature resistance, characteristics that have led to applications as diverse as aerospace engine housings and electronics packaging. Other applications include electronics, ranging from insulation for flexible cables to use as a high-temperature adhesive in the semiconductor industry. High-temperature polyimide carbon fiber composites are also used in non-loading structural components in aircrafts, weapon systems, and space vehicles. The appeal of polyimides is attributable to their unique combination of high-thermal stability, good chemical and solvent resistance, as well as excellent retention of mechanical properties at high temperature.
The polymerization of monomeric reactants (PMR) addition polyimide technology was developed in the mid-1970s at NASA’s Lewis Research Center (renamed Glenn Research Center in 1999). This technology used an alcohol solution of polyimide monomers to make “prepreg,” graphite or glass fiber bundles impregnated with polyimide resins, which could be thermally cured into composites with low voids, eliminating the difficulty of removing high-boiling solvents often used for condensation (step-polymerization) polyimides.
The initial PMR resin, known as PMR-15, is still commercially available and is used worldwide by the aerospace industry as the state-of-the-art resin for high-temperature polyimide composite applications; including engine bypass ducts, nozzle flaps, bushings, and bearings. PMR-15 can also be formualted into adhesives and coatings, and offers easy composite processing, excellent mechanical property retention for long-term use at temperatures up to 288 °C (550 °F), and is relatively inexpensive. As such, PMR-15 is widely regarded as a leading high-temperature polymer matrix composite for aircraft engine components.
However, PMR-15 is made from methylene dianiline (MDA), a known carcinogen and a liver toxin, and the Occupational Safety and Health Administration (OSHA) imposes strict regulations on the handling of MDA during the fabrication of PMR-15 composites. Recent concerns about the safety of workers involved in the manufacture and repair of PMR-15 components have led to the implementation of costly protective measures to limit worker exposure and ensure workplace safety.
Glenn researchers have continued to work on improving the properties and applicability of polyimides, with the ultimate goal of offering the aerospace, chemical, and automotive industries a lower toxicity alternative to PMR-15 that maintains similar processability, stability, and mechanical properties. The new polyimide developed by Dr. Kathy Chuang and Raymond Vannucci under NASA’s Advanced Subsonic Technology (AST) program, named DMBZ-15, replaces MDA with a noncoplanar diamine, 2,2´-dimethylbenzidine (DMBZ).
The DMBZ-15 composition has a glass transition temperature of 414 °C (777 °F). This constitutes an increase in use temperature of 55 °C (100 °F) over the state-of-the-art PMR-15 composites and enables the development of fiber-reinforced polymer matrix composites with use temperatures as high as 343 °C (650 °F). DMBZ-15 graphite fiber reinforced composites exhibit an operational temperature range up to 335 °C (635 °F) and good thermo-oxidative stability in aircraft engine or missile environments.
Partnership
In 2002, Maverick Corporation, of Blue Ash, Ohio, licensed the DMBZ-15 technology.
In 2003, Chuang and Vannucci along with Maverick’s Dr. Robert Gray and Eric Collins received R&D Magazine’s 2003 “R&D 100” award recognizing DMBZ-15 among the best 100 new inventions of the year. In 2004, the DMBZ-15 technology received a NASA Space Act Award.
Product Outcome
DMBZ-15 bushings exhibit better wear resistance than state-of-the-art PMR-15. This ultrahigh-temperature material has a wide range of potential applications from aerospace (e.g., aircraft engine and airframe components, space transportation airframe and propulsion systems, and missiles) to bushings and bearings for non-aerospace applications (e.g., oil drilling, rolling mill). DMBZ-15 lightweight composites provide substantial weight savings and reduced machining costs compared to the same component made with more traditional metallic materials. Using solvent-assisted resin transfer molding, complex parts such as engine center vent tubes can be produced with braided reinforcement.
The DMBZ-15 polyimide has proven useful as a resin matrix with glass, quartz, and carbon fibers for lightweight, high-temperature composite applications similar to PMR-15 in aircraft engine components. Due to its higher temperature capability, it is especially suitable for use in missile applications, including fins, radon, and body components. Of particular interest to NASA, DMBZ-15 is well-suited to use as face sheets with honeycombs or thermal protection systems for reusable launch vehicles, which encounter elevated temperatures during launch and reentry. Other applications include use with chopped fibers to make bushings and bearings for engine or oil drilling components, and in high-temperature coating and ink applications. The light weight of DMBZ-15 polyimide composites invites use in secondary, non-load bearing aircraft engine components such as vent tubes, nozzle flaps and bushings, as well as for oil drilling components. Lightweight polymer composites also offer significant weight savings and subsequent improvements in fuel efficiency in aerospace propulsion and automotive applications.
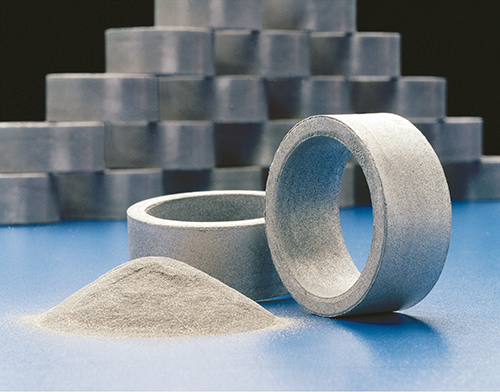
The “R&D 100” award-winning DMBZ-15 high-temperature polyimide
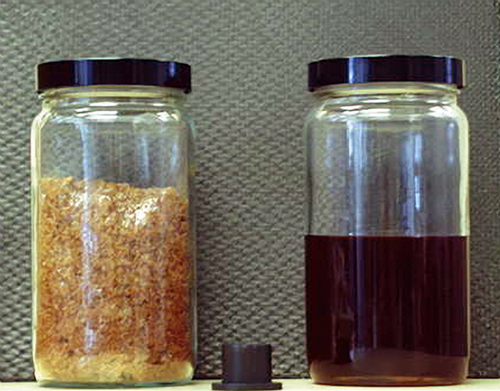
The DMBZ-15 resin can be made into lightweight bushings and polyimide/carbon fiber composite components for high-temperature applications.
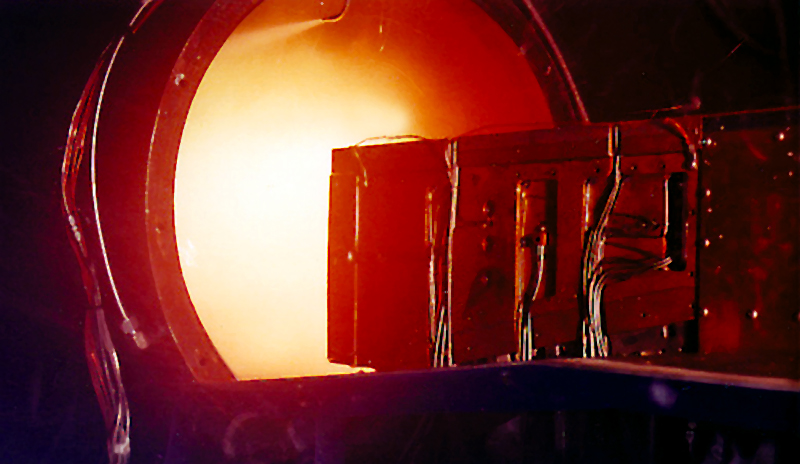
Polyimide composites are introduced to the harsh environmental loads familiar to space launch propulsion systems in the combustion chamber of a rocket-based combined-cycle demonstrator.