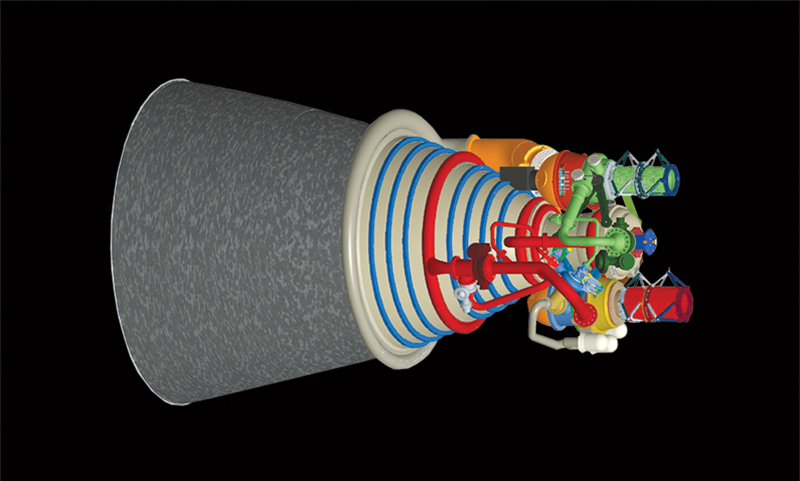
Engineering Models Ease and Speed Prototyping
Originating Technology/NASA Contribution
NASA astronauts plan to return to the Moon as early as 2015 and establish a lunar base, from which 6-month flights to Mars would be launched by 2030. Essential to this plan is the Ares launch vehicle, NASA’s next-generation spacecraft that will, in various iterations, be responsible for transporting all equipment and personnel to the Moon, Mars, and beyond for the foreseeable future.
The Ares launch vehicle is powered by the J-2X propulsion system, with what will be the world’s largest rocket nozzles. One of the conditions that engineers carefully consider in designing rocket nozzles—particularly large ones—is called separation phenomenon, which occurs when outside ambient air is sucked into the nozzle rim by the relatively low pressures of rapidly expanding exhaust gasses. This separation of exhaust gasses from the side-wall imparts large asymmetric transverse loads on the nozzle, deforming the shape and thus perturbing exhaust flow to cause even greater separation. The resulting interaction can potentially crack the nozzle or break actuator arms that control thrust direction.
Side-wall loads are extremely difficult to measure directly, and, until now, techniques were not available for accurately predicting the magnitude and frequency of the loads. NASA researchers studied separation phenomenon in scale-model rocket nozzles, seeking to use measured vibration on these nozzle replicas to calculate the unknown force causing the vibrations. Key to this approach was the creation of a computer model accurately representing the nozzle as well as the test cell.
Partnership
System-response models developed by LMS International NV were used to calculate side-wall loads on the J-2X nozzles. LMS is a Belgium-based company founded in 1980 with over 30 offices around the world, which acts as an engineering innovation partner for companies in automotive, aerospace, and other advanced manufacturing industries. LMS works with customers to improve process efficiency and product quality by offering a unique combination of virtual simulation software, testing systems, and engineering services.
LMS Virtual.Lab, an integrated suite of simulation software, developed the system-response models based on modal data on nozzle replicas from LMS Test.Lab, a software solution for test-based engineering combining high-speed multichannel data acquisition with a suite of integrated testing, analysis, and report-generation tools. Tests were conducted by the Marshall Space Flight Center Structural Dynamics Test Branch, which uses LMS Test.Lab in modal testing for a wide range of projects.
The close integration between LMS Test.Lab and LMS Virtual.Lab means data is readily available without file conversions, which often fail to fully represent critical data, such as frequency response functions (FRFs). Utilizing test data in combination with modeling and predictive tools in this type of hybrid approach will enable engineers to more accurately determine transverse separation forces and design nozzles to better withstand operational loads. Marshall also uses LMS Test.Lab for ground vibration testing (GVT) of the new vehicles.
Preparations are underway for GVT of the complete Ares I craft to be conducted in 2011 using the dynamic test stand at Marshall. Tests will be performed on the “full stack,” or the complete vehicle, including the first and second stage motors, fuel tanks, and crew capsule. Structural vibrations will be induced using up to six hydraulic or electrodynamic shakers delivering random and sine excitations. LMS Test.Lab can provide engineers with critical test data including FRFs, natural frequencies, damping values, and mode shapes to evaluate how the structure will likely vibrate during liftoff, stage separation, and subsequent phases of the flight.
The LMS SCADAS 260-channel front-end is also one of NASA’s large modal data-acquisition systems. The high channel count enables the modal test measurements in fewer test runs. Measuring multiple functions simultaneously allows them to obtain FRFs as well as associated cross spectrums, auto powers, and time data in parallel instead of having to run separate tests. The modal test team plans to complete the Ares GVT in only three test sets versus up to eight runs needed for comparable tests on the Saturn and shuttle vehicles using a system with far fewer channels.
The team also makes extensive use of LMS PolyMAX software, which automatically highlights resonances and provides consistent results that could otherwise vary due to subjective interpretation. In addition, animated operational deflection shape features show how the structure may bend and twist at various frequencies so engineers have deeper insight into dynamic structural behavior.
LMS is focused on the mission critical performance attributes in key manufacturing industries, including structural integrity, system dynamics, handling, safety, reliability, comfort, and sound quality. From this work, LMS engineers gained knowledge that will help develop tomorrow’s rocket propulsion systems and can also be used for engineering applications in a wide range of other industries. By providing onsite support for tests, the LMS technical support and development staff seize opportunities like the work with NASA to expand their knowledge of tests and dynamics in real-world applications.
Product Outcome
As the pool of companies and agencies testing rockets is limited, knowledge related to the execution and optimization of design resulting from such tests is likewise small. Exposure to this data will lead to better modeling and simulation, resulting in better and safer products for the public. This approach of creating system models based on modal test data is useful in research and development studies of similar structures that are difficult to model and whose dynamic behavior is of primary interest. By working with NASA, LMS engineers gained access to uncommon test data to enhance and refine their product to help companies test future processes and designs.
In one recent example of the benefit of amalgamating experiences into an integrated platform, the Spanish division of the European Aeronautic Defence and Space Company, Construcciones Aeronáuticas S.A. (EADS-CASA), also Spain’s leading aeronautical company, implemented LMS Test.Lab and PolyMAX tools to accelerate its ground vibration testing. This aircraft testing process included a series of tests to detect the aircraft resonances as a verification of the aircraft safety and reliability before the first actual test flights. Overall, the LMS Test.Lab GVT solution and the successful deployment and technology transfer project allowed EADS-CASA to realize considerable savings in time and resources on the Airbus A330 Multi-Role Tanker Transport project.
LMS computer simulation and modeling expertise has also been applied to motorcycle safety and stability. Engineers at BMW Motorrad employed LMS DADS mechanical system simulation software to create virtual prototypes of vehicles and mechanical systems. While LMS DADS included a tire model, motorcycle tires can roll up to 50 degrees, creating forces not captured in the conventional model. BMW engineers used the program’s open architecture to write in two subroutines to measure wobble, weave, and kickback. The first subroutine modeled throttle, brake, and handlebar inputs by a virtual rider. The second modeled tires and their interaction with the pavement, including variables for the frame; lower and upper forks; Telelever, a front suspension design unique to BMW motorcycles; front and rear wheels; rear swing arm; and other components. This model proved remarkably accurate in evaluating motorcycle design—engineers consider the simulation results at least as accurate as measurements taken on the test track, but with less invested time and expense. BMW is now able to specify structural design requirements, such as stiffness and mass distribution, which will ensure greater stability and safety of the end product.
Test.Lab®, Virtual.Lab®, SCADAS®, and PolyMAX® are registered trademarks of LMS International NV.
Telelever™ is a trademark of BMW AG Motorrad.
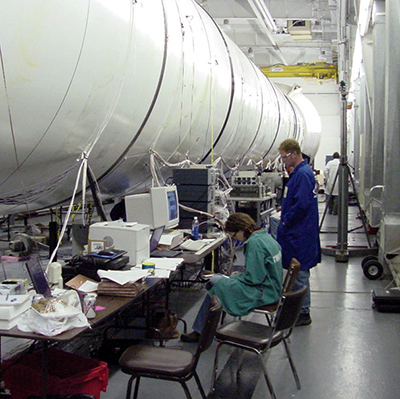
LMS software and data-acquisition hardware help test, analyze, and optimize a vehicle’s ability to withstand the vibration loads experienced during missions.
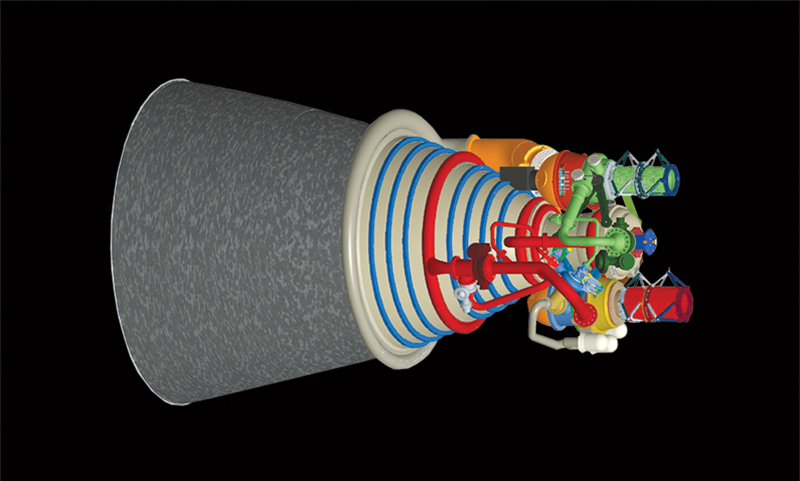
LMS system-response models were used to calculate side-wall loads for the J-2X rocket nozzles, easing NASA’s development and offering LMS engineers a unique opportunity to gather data.