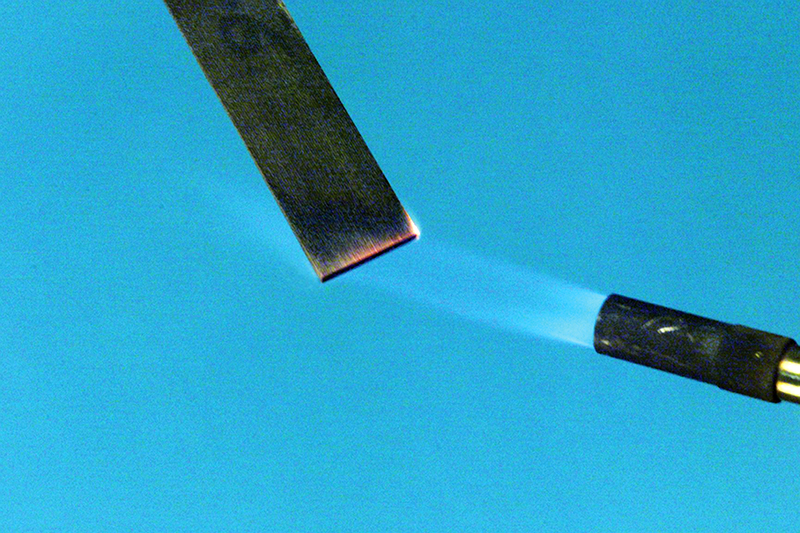
Polyimide Resins Resist Extreme Temperatures
Originating Technology/NASA Contribution
Spacecraft and aerospace engines share a common threat: high temperature. The temperatures experienced during atmospheric reentry can reach over 2,000 °F, and the temperatures in rocket engines can reach well over 5,000 °F.
To combat the high temperatures in aerospace applications, Dr. Ruth Pater of Langley Research Center developed RP-46, a polyimide resin capable of withstanding the most brutal temperatures. The composite material can push the service temperature to the limits of organic materials.
Designed as an environmentally friendly alternative to other high-temperature resins, the RP-46 polyimide resin system was awarded a 1992 “R&D 100” award, named a “2001 NASA Technology of the Year,” and later, due to its success as a spinoff technology, “2004 NASA Commercial Invention of the Year.” The technology’s commercial success also led to its winning the Langley’s “Paul F. Holloway Technology Transfer Award” as well as “Richard T. Whitcom Aerospace Technology Transfer Award” both for 2004. RP-46 is relatively inexpensive and it can be readily processed for use as an adhesive, composite, resin molding, coating, foam, or film. Its composite materials can be used in temperatures ranging from minus 150 °F to 2,300 °F. No other organic materials are known to be capable of such wide range and extreme high-temperature applications.
In addition to answering the call for environmentally conscious high-temperature materials, RP-46 provides a slew of additional advantages: It is extremely lightweight (less than half the weight of aluminum), chemical and moisture resistant, strong, and flexible.
Pater also developed a similar technology, RP-50, using many of the same methods she used with RP-46, and very similar in composition to RP-46 in terms of its thermal capacity and chemical construction, but it has different applications, as this material is a coating as opposed to a buildable composite.
A NASA license for use of this material outside of the Space Agency as well as additional government-funded testing proved that RP-46 is even more exceptional than originally thought.
Partnership
Unitech LLC, of Hampton, Virginia, is an advanced materials solutions provider specializing in advanced materials technology, engineering, manufacturing, research and development, and prototyping services. In 2001, Unitech received a nonexclusive license from NASA for commercialization of the cost-effective, weight- and space-saving high-temperature material RP-46 and the RP-50 coating.
Using the NASA-developed technology, Unitech applied for a Small Business Innovation Research (SBIR) contract with the U.S. Navy to develop insulation for an all-electric ship that was under consideration. One of the considerations the Navy had was the need for an extremely fire-resistant material. While initial NASA testing had proven that RP-46 could withstand temperatures in the range of 700 °F, the Navy was looking for a material that could withstand anywhere from 8,000 to 250,000 volts of electricity. Under this Navy SBIR, independent testing showed that RP-46 could withstand temperatures up to 2,300 °F. This discovery made it ideal for use in the original Navy application, but also opened up the possibility that the material could be used in future applications, like in high-voltage insulation for high-rise buildings, where great amounts of power run long distances.
Product Outcome
Unitech now commercially manufactures RP-46, the high-temperature polyimide resin matrix system, and RP-50, the high-temperature polyimide coating. In addition to the host of technical specifications that make RP-46 an incredible invention, one of the key features that makes RP-46 so appealing commercially is its versatility; the polyimide can be used as a molding, adhesive, coating, composite matrix resin, foam, or film. It is available as a liquid for prepreg of carbon, glass, or quartz fabric; or as a powder for compression molding. Although specifically designed for the Space Program, industry uses abound.
The traditional use of RP-46 is to impregnate fibers (such as glass, carbon, Kevlar, etc.) with the resin to produce rolls of fabric that can then be cut and shaped. These pieces, which are then heat and pressure cured, can be used in a traditional lay-up to make a structural part. Users employ this method for creating any number of pieces, primarily for use in high-temperature aerospace applications. It can serve as a composite material for thermal skins on aircraft and spacecraft and sees many uses in aerospace engines and exhaust duct systems, where the material is prized for its light weight, durability, and temperature resistance. Similar applications include the high-speed motor sports industry, where the company has already seen interest from NASCAR, Formula One, and motorcycle racing groups.
Parts built from RP-46 are also finding use in rocket nose cones, where in addition to the light weight and temperature resistance, the dielectric, insulating properties are prized. Rocket nose cones often experience a great deal of heat while also carrying sensitive electronics. The nose cone of a missile, for example, may contain that weapon’s guidance system, so RP-46 would be able to provide the temperature resistance as well as be able to butt against the electronics without risk.
RP-46 can also be used as a molding material. In this application, rather than using the prepregged fabrics, a customer would receive a powder form of the resin and then, depending on the intended use, employ various additives and fillers to create the desired composition. The material comes heated and staged but not completely cured. Once the customer mixes the powder, it is then compression-molded into the specific part. So far, one of the most common uses of this method has been to create bearings for high-temperature industry uses. Another application is in creating grinding wheels. The wheels use RP-46 to bond industrial diamonds in place for grinding extremely hard materials. Grinding wheels made from this material last longer and work longer at higher temperatures.
RP-50 is a coating material that shares many of the same qualities as RP-46, but would not be used for structural applications or making parts. Uses include high-temperature electrical insulation and flexible circuitry, where its electrical and thermal insulating properties are well-suited.
Kevlar® is a registered trademark of E. I. du Pont de Nemours and Company.
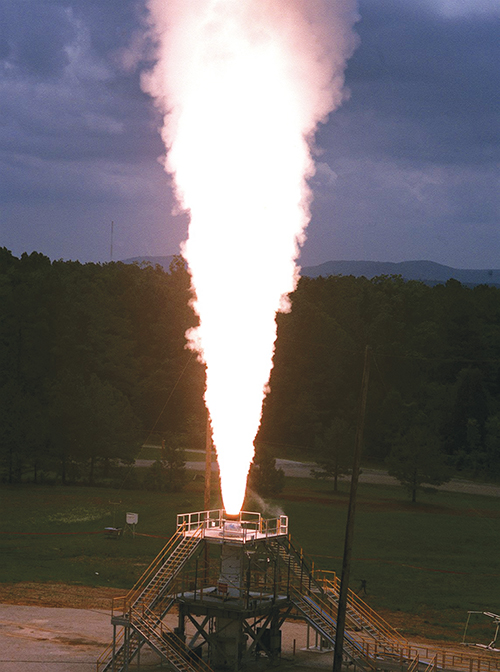
The temperatures in rocket engines can reach well over 5,000 °F.
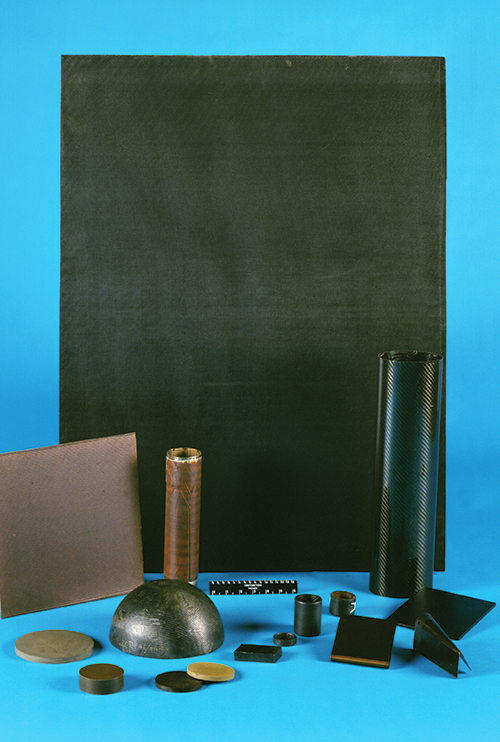
Unitech LLC received a license from NASA for commercialization of the cost-effective, weight- and space-saving high-temperature material.
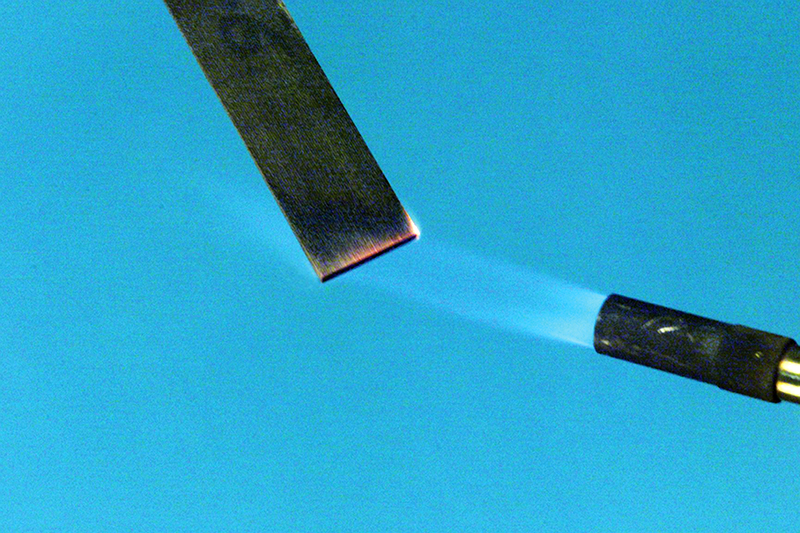
Dr. Ruth Pater of Langley Research Center developed RP-46, a polyimide resin capable of withstanding the high temperatures of aerospace applications.