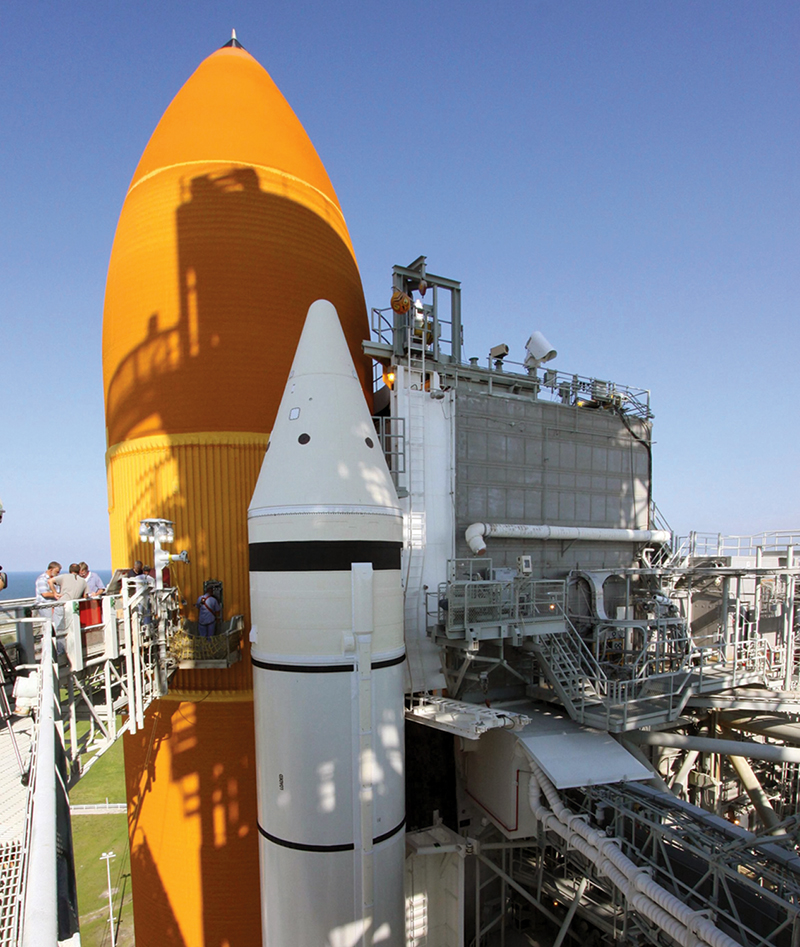
Ultrasonic Detectors Safely Identify Dangerous, Costly Leaks
NASA Technology
In 1990, NASA grounded its space shuttle fleet. The reason: leaks detected in the hydrogen fuel systems of the Space Shuttles Atlantis and Columbia. Unless the sources of the leaks could be identified and fixed, the shuttles would not be safe to fly.
To help locate the existing leaks and check for others, Kennedy Space Center engineers used portable ultrasonic detectors to scan the fuel systems.
As a gas or liquid escapes from a leak, the resulting turbulence creates ultrasonic noise, explains Gary Mohr, president of Elmsford, New York-based UE Systems Inc., a long-time leader in ultrasonic detector technologies. “In lay terms, the leak is like a dog whistle, and the detector is like the dog ear.” Because the ultrasound emissions from a leak are highly localized, they can be used not only to identify the presence of a leak but also to help pinpoint a leak’s location. The NASA engineers employed UE’s detectors to examine the shuttle fuel tanks and solid rocket boosters, but encountered difficulty with the devices’ limited range—certain areas of the shuttle proved difficult or unsafe to scan up close.
To remedy the problem, the engineers created a long-range attachment for the detectors, similar to “a zoom lens on a camera,” Mohr says. “If you are on the ground, and the leak is 50 feet away, the detector would now give you the same impression as if you were only 25 feet away.” The enhancement also had the effect of reducing background noise, allowing for a clearer, more precise detection of a leak’s location.
Technology Transfer
While the shuttle fleet was soon deemed flightworthy again, UE recognized the potential benefit of the NASA innovation for many ultrasound detection applications. The company licensed the long-range module from Kennedy (Spinoff 1998) and began offering it as a component for its Ultraprobe line of commercial ultrasound detectors.
“By the very nature of it, we probably would not have spent the money to develop this technology on our own,” says Mohr. “It would have been hard to see the commercial value until it was already developed. NASA developed the technology to address its need, and we licensed it for the potential commercial success.”
Benefits
The long-range module has since proven to be a valuable addition to UE’s commercial offerings.
“We have maintained the original design since the beginning of the license. It works really well for our customers, and that’s what we care about,” Mohr says.
UE Systems’ detectors play a key role in managing safety, cost, efficiency, and environmental impact across a broad range of industries. In addition to leak detection, the major applications for the technology include ball bearing and mechanical inspection, electrical inspection, and valve testing.
Detecting leaks in factory compressed air systems is perhaps the technology’s most valuable use, says Mohr. “Intuitively, from an operating point of view, compressed air seems to be free. It’s just air. But it in reality, it is the single most expensive utility a plant will have.” Almost every plant leaks at least 20 percent of its compressed air, if not 30 or 40, Mohr explains. This represents enormously expensive energy inefficiencies; for an automotive plant, these costs could be in the millions, says Mohr, while a big mining plant could incur losses in the several millions.
Using a UE ultrasound detector with the NASA-developed long-range module, factory inspectors can easily scan compressed air lines, which are typically run overhead, from below.
“It acts as a virtual ladder allowing customers to gather data safely and effectively from the ground,” says Mohr.
Coupled with UE’s proprietary software, the detector not only locates leaks but can calculate the impact each leak represents, helping companies save costs and reduce their carbon footprint. “If you go through a whole plant, you might determine you have 50 leaks costing you this much in compressed air, this much in electricity,” says Mohr.
In the case of ball bearing and mechanical inspection, UE’s detectors pick up the ultrasound produced by friction in mechanical components, allowing users to detect subtle changes that may indicate impending failure. In electrical applications, the detectors can scan substations, transformers, and switchgear for costly and potentially dangerous electrical discharge. While infrared cameras are often used to detect the discharge, these cameras do not detect coronas, a common indicator of an electrical “leak,” and do not work if the user is out of the line of sight. With the addition of the NASA long-range module, inspectors can survey electrical equipment comprehensively and from a safe distance, identifying discharge through the high-frequency noise the emission produces.
The enhanced functionality and safety offered by UE Systems’ NASA technology represents a boon for the company’s worldwide customer base, Mohr notes.
“NASA’s expertise in research and development has allowed us to provide our customers with a value-added solution that has enhanced our technology,” he says. “It’s been a great partnership with NASA, sharing with them our expertise and in turn getting to take advantage of theirs. It’s definitely been a win-win.”
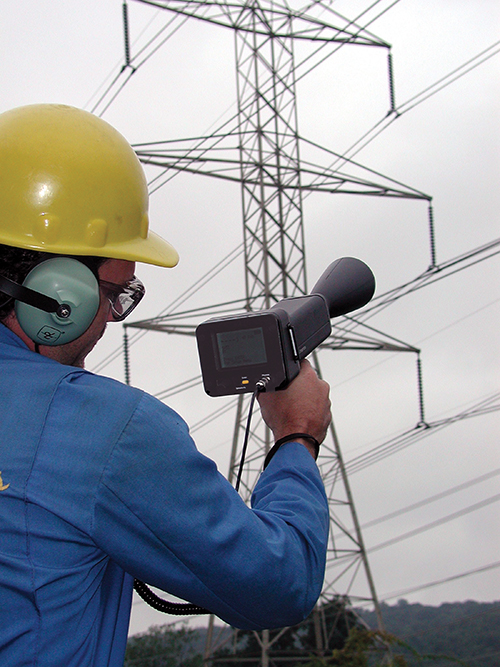
Using its licensed NASA technology, UE Systems’ detectors allow users to scan for electrical leaks (left) and compressed air leaks (right) safely and with ease.
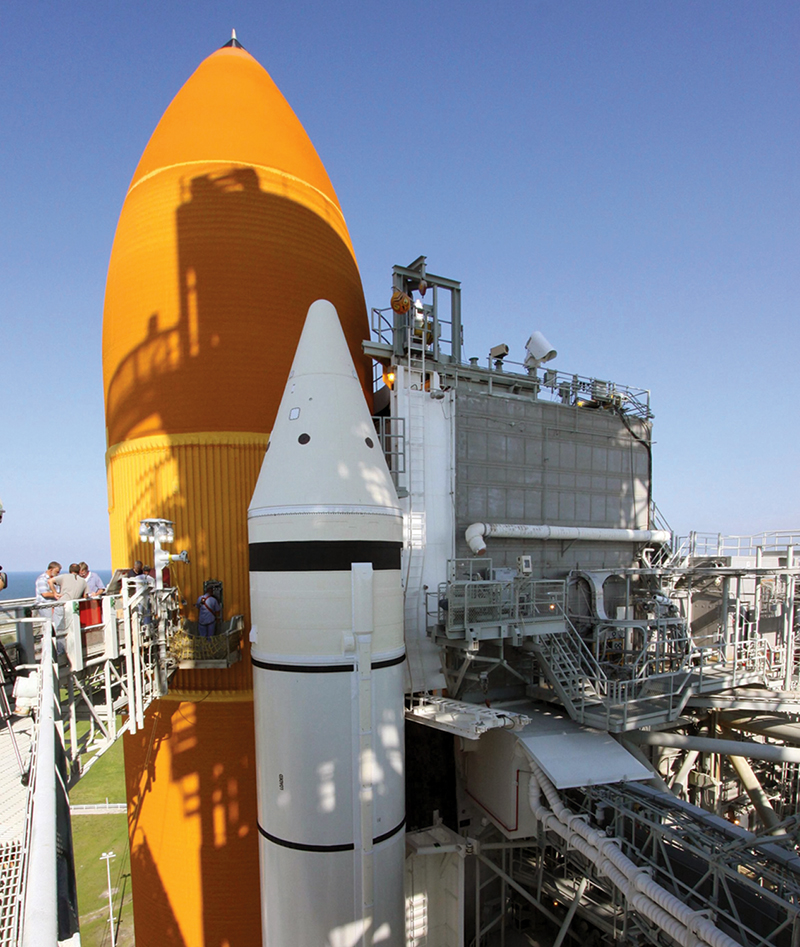
In order to scan unsafe or difficult-to-approach areas of the space shuttle for hydrogen leaks, NASA developed a long-range module to enhance a private industry partner’s ultrasonic leak detection technology.