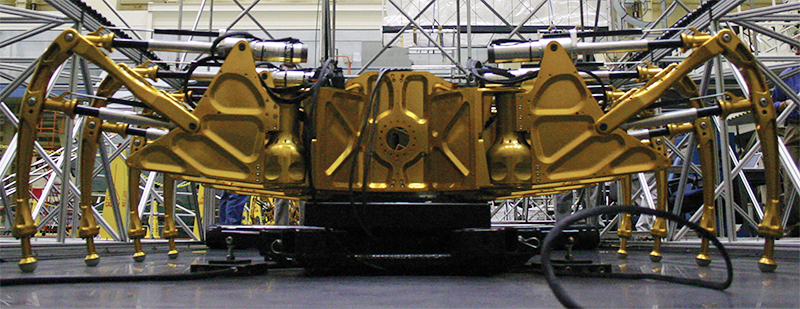
Autonomous Robots Take On Dangerous Warehouse Jobs
NASA Technology
“Where does a 600-pound spider go? Anywhere she wants to.”
The spider in question, dubbed “Spidernaut,” was part of a prototype robot team built in 2005 to assemble a solar array on the moon. The goal was not only to have robots do the manual labor but for them to work cooperatively without human direction.
To achieve that, engineers needed robots optimized for various tasks as well as software capable of directing the entire operation from start to finish. That work continues to this day, and some of the team involved in programming Spidernaut and her sisters have taken that experience into the commercial sector, where their software is poised to automate difficult and dangerous drudge work in warehouses and beyond.
The slightly menacing-looking Spidernaut was designed to climb up the truss that supported a solar array, carrying flat panels to where they needed to be installed. “For a given mass, we wanted to get the most acreage possible, which means a very lightweight truss,” explains Rob Ambrose, principal technologist of the Software, Robotics, and Simulation Division of Johnson Space Center’s Game Changing Development Program.
“And what’s the best kind of machine that can climb on a web-like truss? A spider, of course.” The team also designed a six-limbed robot that could fasten joints with torque tools, and a third robot with a camera mounted on a thin tendril-like limb.
Designing the software to drive three very different robots through such a complex task was a big job. The NASA team, led by Ambrose at Johnson with contributions from the Jet Propulsion Laboratory and Langley Research Center, turned to computer programmers at Carnegie Mellon University.
Among other challenges, recalls Fred Heger, who was a graduate student when he worked on the project at Carnegie Mellon, was ensuring the robots completed each task in the right order, “so you don’t have a robot on the inside of a half-finished building with no way out.”
Technology Transfer
Within just nine months in 2005, the NASA and Carnegie Mellon team had working prototypes of all three robots and the software to drive them, Ambrose says.
Although that program was ultimately cancelled amid shifting Agency priorities, Ambrose says, “a number of key component technologies led to major innovations in later robots that NASA built.”
The work also paid dividends for Heger, now a senior research scientist at Cambridge, Massachusetts-based Vecna Technologies. The company recently released a suite of robots designed to move items through warehouses, which is built in part on the work Heger did for NASA.
“The physical shape is standard, commercially available equipment that people use today in warehouses. Except today, people are riding them and controlling them. Our computers, sensors, and robot software based on artificial intelligence enhance traditionally manual equipment to automate that,” explains Vecna cofounder and chief innovation officer Daniel Theobald.
With this system, “we’ve got a bunch of basic robotic drivers and then a robot supervisor that’s telling them where to go,” he says.
The software, which Heger was integral in developing, traces directly back to the software he worked on for NASA. “The math and the models are the same, but new lines of code have been written to implement it in more modern frameworks,” Theobald explains.
Benefits
Vecna’s autonomy kit is designed to work in places like shipping warehouses, where one truck brings packages that must be distributed to different delivery trucks.
It’s already a highly automated system, explains Heger, with conveyor belts and scanning machines, but “with the rise of e-commerce and people wanting more strangely shaped things more and more quickly, shipping companies end up having to transport material that they can’t put on a conveyor belt.”
For example, a rolled-up carpet or a bicycle would instead require a person to unload it from the truck and onto a cart, which would then be driven by a person to the outgoing truck, where another person would have to manually load it up again.
Vecna’s smart robots can drive the cart and other equipment themselves, leaving people to only do the loading and unloading. And because the software links a fleet of robots, it can direct them to deliver the packages in the most efficient way across the entire warehouse, making the whole process faster.
“The software knows where all the trucks are and knows where packages are piling up. It can figure out, based on known demand and predicted or learned demand patterns, where it should send these robots,” Heger explains, noting that this is a type of problem-solving humans aren’t particularly good at.
The robots also make people more efficient, he adds, because the software is able to, for example, “always make sure they have empty carts they can load onto, so they’re not waiting for a robot to come by.”
Beyond speeding up the process, the robots also significantly reduce accidents, which cause thousands of injuries each year. “We designed a safety-certified system to have a check, a double check, a triple check that if the robot is potentially going to hit something, it will automatically shut down before that happens.”
That means, Heger says, “even if the robotics system only worked as efficiently as a human for the cost for the delivery from point A to point B, you’d still come out way ahead in terms of the reduction in accidents.”
Currently, Vecna has a contract with a major U.S. shipping company, and they see big potential for the market even beyond the warehouse. “One of the neat things is that our system doesn’t require a brand-new piece of equipment. You can add our sensors and software to existing equipment, and that becomes a robot,” Theobald explains.
The company envisions a day when “anything you see in your office will be delivered by a robot in its journey from wherever it’s manufactured to your door,” Heger says.
“That was part of the strategy: we designed a robotic system that could work on any vehicle—pallet jacks, forklifts, golf carts, larger, smaller—anything that moves can be automated.”
That kind of system, Ambrose says, is something he sees as also being crucial for NASA’s plans. “The challenges we’re looking at for sending people into deep space are best met by having robots predeployed to set things up. It’s not cost-effective to have people go there for the very first effort,” he says. The robots could also maintain equipment during long absences between human visits and help support astronauts on the ground.
“So Fred’s experience orchestrating very different robots as a team is the kind of thing we’re going to have to focus on.”
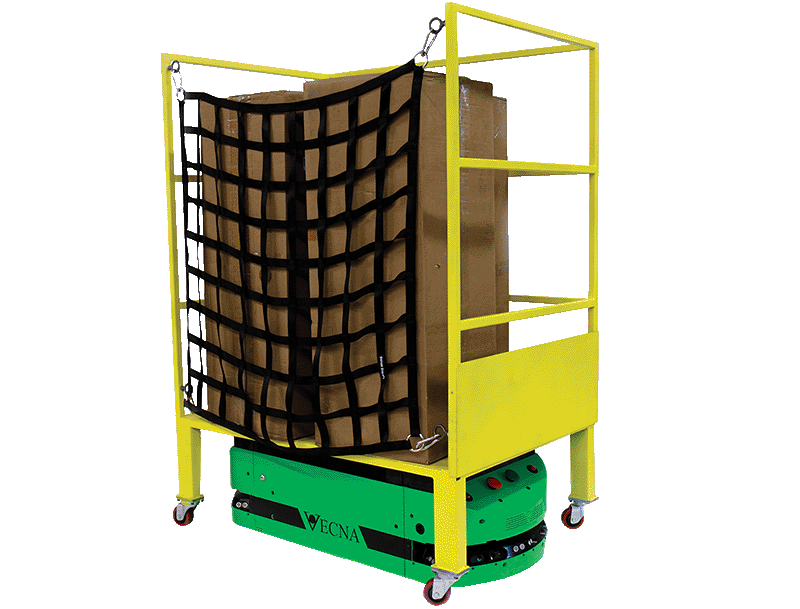
Using expertise built on NASA projects, Vecna Technologies has built an “autonomy kit” for commercial warehouse equipment to automate, for example, package handling. Software coordinates the robot’s tasks to ensure packages are moved through the warehouse in the most efficient possible manner.
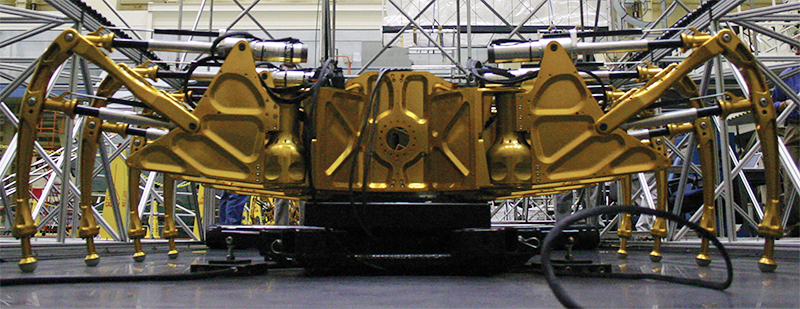
“Spidernaut” is part of a team of robots designed at Johnson Space Center to autonomously assemble a solar array on the moon. Vecna Technologies senior research scientist Fred Heger honed his programming skills on the project, developing a system to ensure the robots completed the tasks in the optimal order.