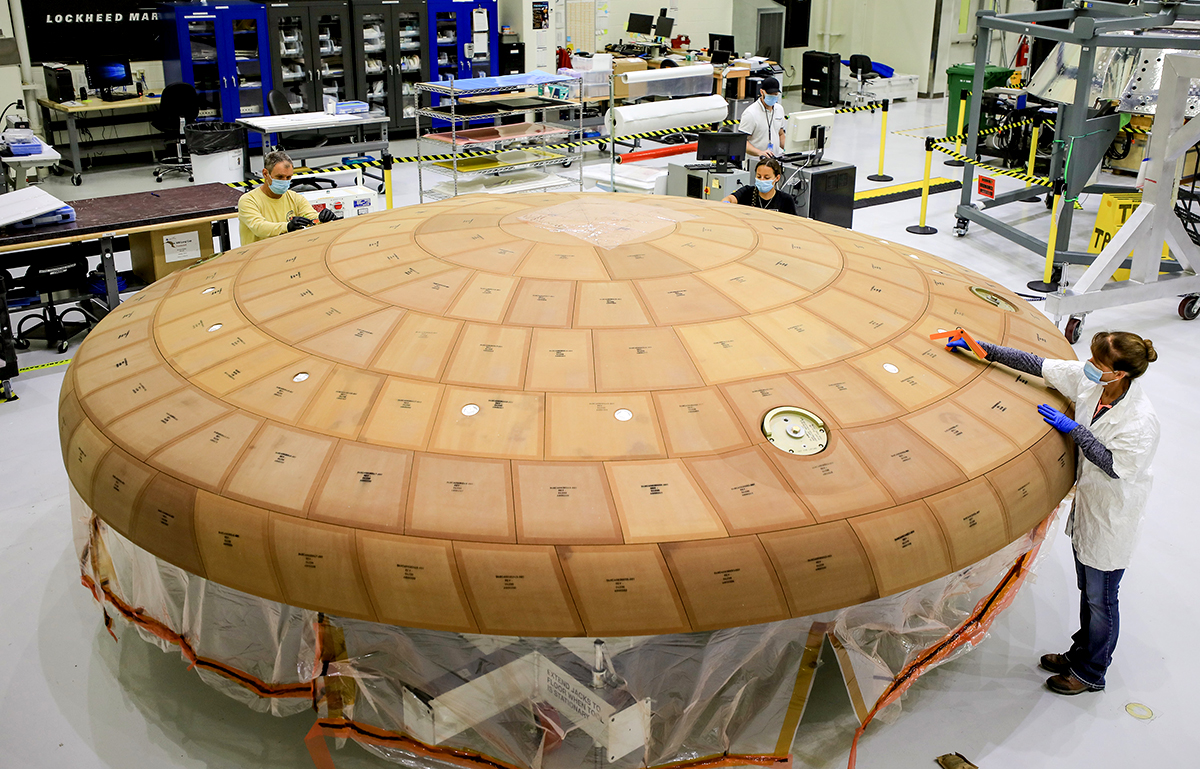
Ultrasonic Inspections Protect Astronauts, Boat Owners
Subheadline
Technology for inspecting Orion heat shield now checks integrity of composite materials in boats
Shipbuilders didn’t have the option of fiberglass when the nonprofit American Bureau of Shipping (ABS) was established 160 years ago to help safeguard life and property on the seas. Fortunately, technology to help better ensure the safety of ocean vessels has also come a long way in that time, in part because people have become a spacefaring species.
ABS Group of Companies Inc. of Spring, Texas, an ABS subsidiary that provides risk management solutions and extends marine technical services to smaller vessels like yachts and fishing boats, has now taken a technology developed to inspect the heat shield on NASA’s Orion spacecraft and is offering it for evaluating seacraft hulls made with advanced composite materials.
Ships longer than 175 feet or so require the strength of a metal hull. Because metal conducts sound easily, these can be inspected using traditional ultrasonic scanning, which sends high-frequency sound into the material and detects damage by spotting irregularities in the echoes returned to the device. Smaller vessels can save weight with composite hulls, often made of layers of fiberglass, epoxy resin, or carbon fiber, but these materials absorb and dampen sound, making them much harder to evaluate with ultrasonic technology.
“We looked at industries that were already more advanced in their ability to detect defects in nonmetallic materials, and the aerospace industry is really leading that sector,” said Nick Obando, director of asset integrity management at ABS Group.
The weight savings provided by composite materials, as well as reliable inspections to ensure safety, are among the very highest priorities for NASA and other spacecraft designers.
So when the space agency chose a new construction method for the Orion module’s heat shield, its engineers needed an inspection technique that could help guarantee its integrity. They ended up turning to the nonprofit R&D company Aerospace Corporation to create a new ultrasonic technology for examining composites – one that would also turn out to fit the needs of ABS Group and its smaller, lighter clientele.
From Space to the Seas
Orion is the spacecraft that will carry astronauts to the Moon and back under NASA’s Artemis missions in the coming years. Its heat shield will protect it on its return, as it streaks through Earth’s atmosphere generating temperatures up to 5,000°F. The shield was originally to be made by injecting Avcoat, a lightweight epoxy resin previously used for the Apollo capsule’s heat shield, into the cells of a honeycomb structure. However, when a test shield was built, cracks formed at some seams, so NASA and contractor Lockheed Martin decided to glue blocks of Avcoat directly to the shield’s base.
“In doing so, they created a situation where that bond line now became critical,” said William Prosser, technical fellow for nondestructive evaluation in the NASA Engineering and Safety Center at the agency’s Langley Research Center in Hampton, Virginia. “And they didn’t have a good way to test it because the strength of the bond was greater than the strength of the Avcoat material, so they couldn’t do pull tests on them like they did with shuttle tiles.”
The Engineering and Safety Center maintains networks of experts that extend beyond NASA and happen to include Shant Kenderian, director of Aerospace Corporation’s Materials Processing Department and the company’s Nondestructive Evaluation Laboratory.
When Prosser reached out to Kenderian in 2015, Aerospace Corporation was already dabbling with a technology that had potential to solve the problem. Recent hire Toby Case had brought along advanced scanning technology he had developed as a graduate student, and the team demonstrated it could perform a simple spot check on a heat shield sample. “But to do a big scan on a production scale, that’s a completely different level of robustness,” Kenderian said.
What followed were two years of refining the focusing and signal-processing techniques, and even the hardware, until a user could hand-scan a large area of composite materials and get a clear image of any damage or defects beneath the surface. “All these signal processing tricks or steps that we applied, every step enhanced the signal more and more until it became clear,” Kenderian said. “That level of development all happened under the funding from NASA.”
NASA and Lockheed Martin engineers were also involved in the effort, especially when the time came to test and validate the technology. “And then we had to actually translate that into a system that could be used on the actual flight hardware at Kennedy Space Center by the inspectors,” said Prosser. “And that was another significant activity.”
Aerospace Corporation received a patent on the technique in late 2019, and it wasn’t long before ABS Group came calling, licensing the technology in early 2021 and turning it out as a commercial service the following year. “So as far as I know, we’re first to bring a true ability to evaluate through the thickness of these nonmetallic composites for the maritime industry,” said Obando.
Sounding Out Markets
He said the company is targeting three main types of users: manufacturers and retailers, both of which can use the technology for quality assurance, and repair shops that need to assess damage or defects. “It’s trying to protect all of the parties involved, with better assurance about the integrity of the asset during fabrication and post-fabrication,” said Obando. The manufacturer or reseller can better guarantee quality, and customers can have more faith in their purchase. He also noted insurers might have a use for these thorough inspections.
But he said the company is still working to determine other niches it can fill in the boating industry and beyond. “We’re excited about the technology,” Obando said. “So now it’s really about translating that excitement to our clients to say, ‘Hey, we think this could help you, can you help show where there’s a use case for this in this industry that’s really underserved?’”
One future market with potential is offshore platforms, where composite materials could be preferable for repairs to pipes and topside structures if there’s a way to test their integrity, Obando said.
Offshore platforms are also major users of composite pressure vessels. These high-pressure storage tanks are lightweight but difficult to assess for damage – and dangerous if they fail. “The main cause of failure in those is a disbond or delamination between the layers,” Obando said – exactly the kind of defect the new technology is designed to spot.
Meanwhile, Kenderian said his group has been approached by automotive and petrochemical companies interested in the technology.
“I think it may generate interest for a lot of composite materials that are covered by a more complicated material, like foams and cork. We don’t know yet,” he added. But he said the technology will have to keep evolving. “I really think there’s a conspiracy where, the more we advance our technology, they start to design things on the edge of our capabilities, always,” he laughed.
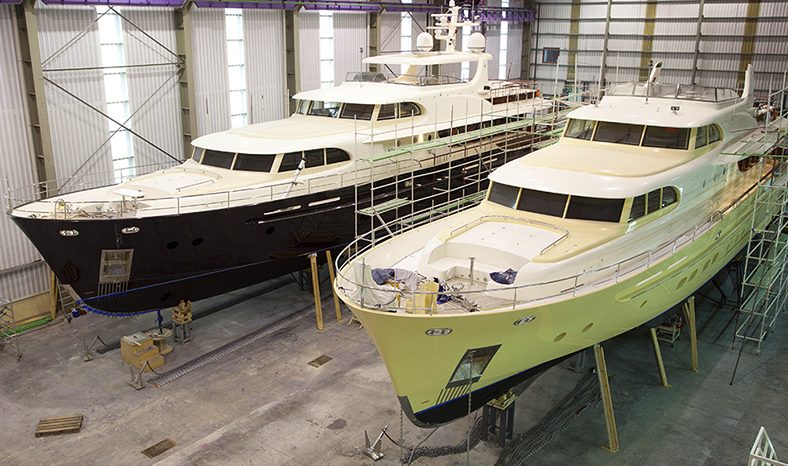
One market that ABS Group is targeting for its ultrasonic scanning technology for composite materials is the boat repair industry, where it can assess damages or defects that can’t be seen on the surface. Credit: Getty Images
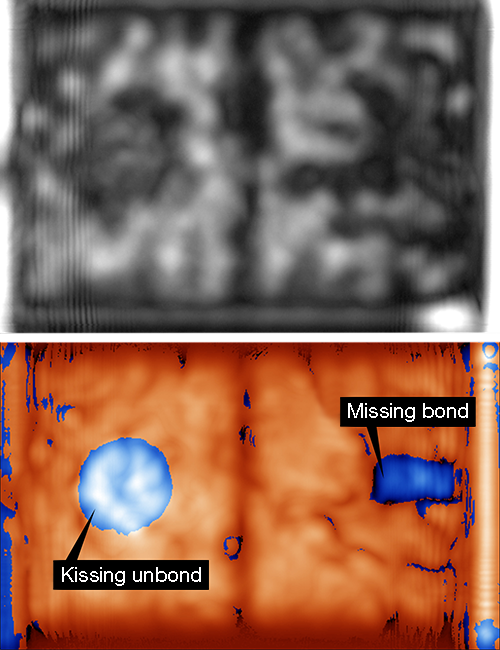
A raw ultrasonic scan of a block of Avcoat, the epoxy resin on the Orion spacecraft’s heat shield, yields little useful information (top). Extensive signal processing that Aerospace Corporation developed for NASA, however, is able to detect defects like a missing bond and a “kissing unbond” – a spot where the surfaces meet but aren’t bonded to each other (bottom). Credit: NASA
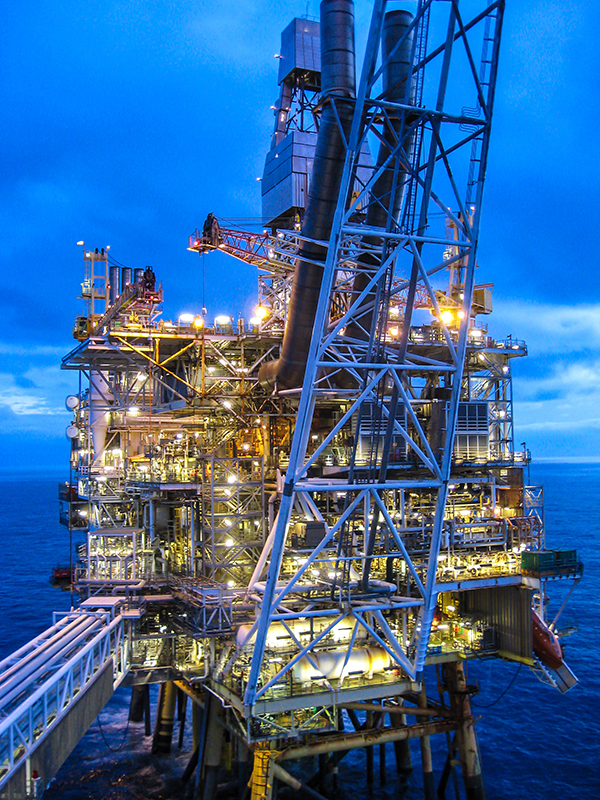
One potential market for composite material inspection is in offshore platforms, where damaged composite pressure vessels can pose a hazard and composite materials could better repair pipes and topside structures if there was a way to test their integrity. Credit: Getty Images
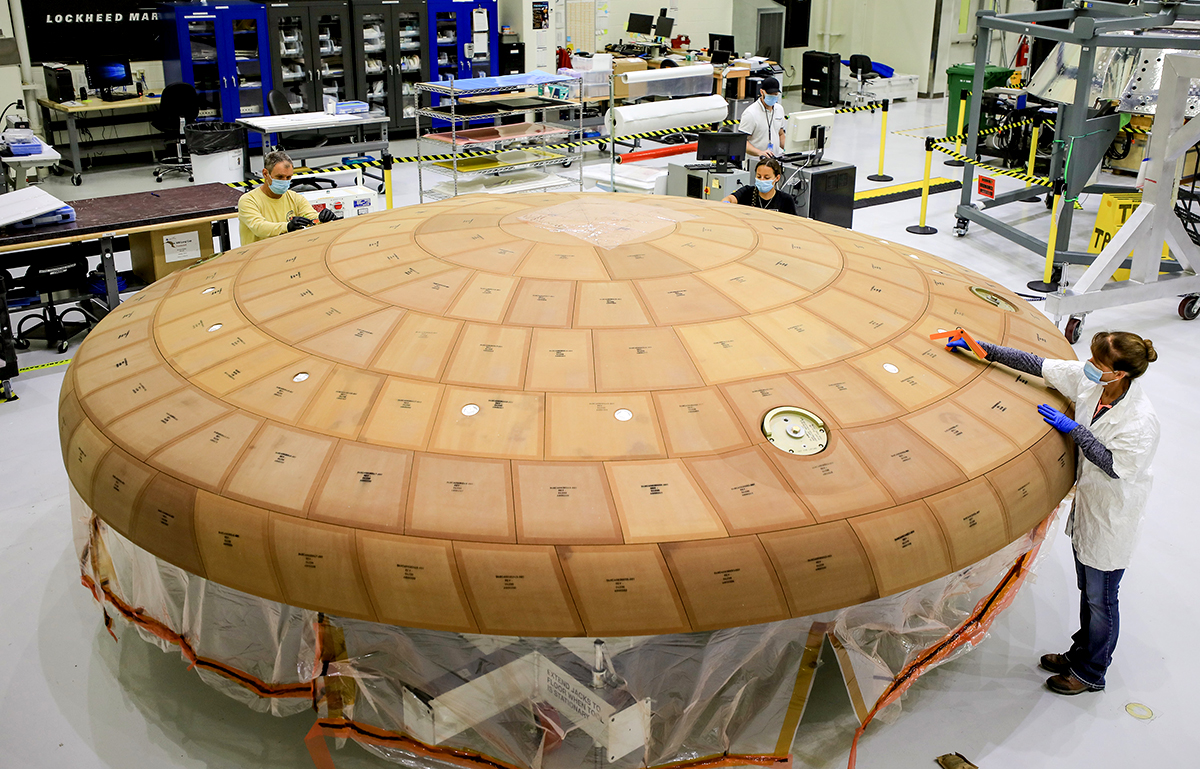
Technicians at Kennedy Space Center finish applying blocks of Avcoat, a lightweight epoxy resin, to the heat shield for the Orion crew module. To examine the blocks’ bond to the shield, NASA turned to Aerospace Corporation to develop an ultrasonic sensor that could spot defects in or under the material despite its resistance to sound. Credit: NASA