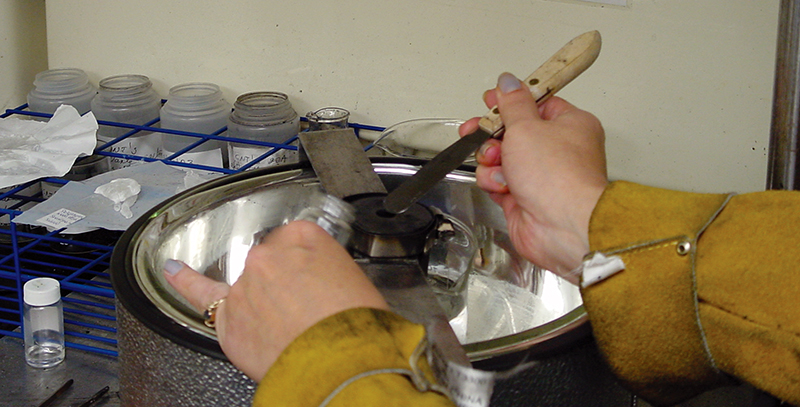
NASA Innovation Builds Better Nanotubes
Originating Technology/NASA Contribution
One of the basic nanotechnology structures, the carbon nanotube, is a graphite sheet one atomic layer thick that is wrapped on itself to create an extraordinarily thin, strong tube. Although carbon nanotubes were discovered more than 15 years ago, their use has been limited due to the complex, dangerous, and expensive methods for their production. This unwieldy process has made widespread application of single-walled carbon nanotubes (SWCNTs) cost-prohibitive up until now.
Goddard Space Flight Center has made a major step forward in limiting these drawbacks. While traditional manufacturing methods use a metal catalyst to form the tubes, NASA researchers pinpointed this step as the cause of many of the drawbacks that were impeding development of SWCNTs. NASA researchers, under the direction of Goddard’s Jeannette Benavides, discovered a simple, safe, and inexpensive method to create SWCNTs without the use of a metal catalyst. Benefits of this process include lowered manufacturing costs, a more robust product, and a simpler, safer process that produces a higher purity nanotube. NASA’s SWCNT manufacturing process eliminates the costs associated with the use of metal catalysts, including the cost of product purification.
The removal of the catalyst not only reduces cost, but results in high-quality, very pure SWCNTs. Because NASA’s process does not use a metal catalyst, no metal particles need to be removed from the final product. Eliminating the presence of metallic impurities results in the SWCNTs exhibiting higher degradation temperatures (650 °C rather than 500 °C) and eliminates damage to the SWCNTs by the purification process.
In addition to saving costs and creating a purer product, this new method also introduces features that make production simpler and safer. Unlike most current methods—which require expensive equipment (e.g., vacuum chamber), dangerous gasses, and extensive technical knowledge to operate—NASA’s simple SWCNT manufacturing process needs only an arc welder, a helium purge, an ice-water bath, and basic processing experience to begin production. This simple method also offers an increase in quantity. Whereas traditional catalytic arc discharge methods produce an “as prepared” sample with a 30 to 50 percent SWCNT yield, NASA’s method produces SWCNTs at an average yield of 70 percent.
Partnership
Nanotailor Inc., a nanomaterials company specializing in SWCNTs, based in Austin, Texas, licensed Goddard’s unique SWCNT fabrication process with plans to make high-quality, low-cost SWCNTs available commercially.
“The nanotech industry is growing by more than 40 percent a year, but multi-walled carbon nanotubes have been the primary technology used. Single-walled technology just hasn’t taken off because of the cost,” notes Ramon Perales, president and chief executive officer of Nanotailor. “If we can get the cost down, we can be a step ahead and make higher quality nanotechnology more affordable.” Other companies that have licensed the process include Idaho Space Materials Inc., a start-up in Boise, and American GFM Corporation, in Chesapeake, Virginia.
With a license agreement in place, Nanotailor built and tested a prototype based on Goddard’s process. Device integrators and nanotechnology-based device companies are among Nanotailor’s first customers, though the company hopes to cater to a wide variety of industries and research organizations.
According to Dr. Reginald Parker, chief technical officer of Nanotailor, “Most industries using multi-walled tubes and technologies that require property improvement without a shift in weight will be able to benefit from this technology. A better product at a lower price will bring higher quality nanotechnology to biomaterials, advanced materials, space exploration, highway and building construction . . . the list seems endless as nanotubes have diverse and excellent properties.”
Product Outcome
Nanotailor produces an optimized product based upon intellectual property licensed from NASA. Carbon nanotubes are being used in a wide variety of applications, and NASA’s improved production method will increase their prevalence in the following areas:
- Medicine: SWCNTs offer the opportunity for improvements in many medical technologies, including implantable defibrillators (pacemakers); portable/field equipment; implantable biosensors; improved hearing aids; electrochemical analysis of biological materials; composites for long-lasting bone and joint implants; delivery of medicines and other treatments at the cellular level.
- Microelectronics: SWCNTs offer low resistance, low mass density, and high stability for improved microcircuits, nanowires, and transistors for miniature electronics; and consumer products, including pagers, cell phones, laptop and hand-held computers, toys, power tools, and automotive components.
- Scanning force/tunneling microscopy: Probing tips made with SWCNTs last longer and perform better than conventional silicon tips, improving materials science research and development; production quality control of semiconductor materials and data storage media; and evaluation of biological samples.
- Materials: SWCNTs do not affect a polymer’s mechanical properties, allowing stress, transition, and thermal strain to be observed. SWCNTs also can be used to reinforce composites. Applications include dopants to create electrically conductive polymers; and easier monitoring of composites in critical applications (e.g., aircraft).
- Molecular containment: SWCNTs can be used to contain various elements, such as hydrogen for fuel cells and lithium boron hydrate for radiation shielding.
During September 2007, Nanotailor announced that its method for manufacturing high-quality carbon nanotubes was selected as a winner of the third annual Nanotech Briefs Nano 50 Awards. Jeannette Benavides, the inventor of the technology now retired from Goddard and serving as Nanotailor’s director of research, was recognized at the NASA Tech Briefs National Nano Engineering Conference in Boston, November 14 and 15, 2007.
“We are very pleased that our technology received a Nano 50 award,” commented Perales, “Nano 50 nominations are judged by a panel of nanotechnology experts of which the 50 technologies, products, and innovators with the highest scores are named winners. We are excited that our peers in the nanotechnology community believe that our technology has significantly impacted, or is expected to impact, the nanotechnology industry.”
Nanotech Briefs® is a registered trademark, and Nano 50™ is a trademark of ABP International Inc.
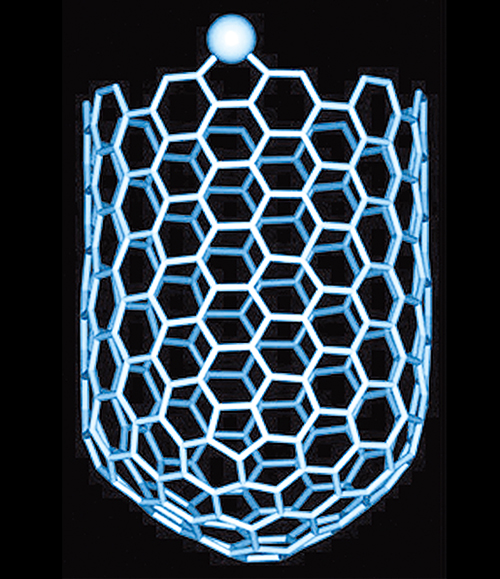
Thousands of times smaller than the average human hair, carbon nanotubes are extremely long and thin yet strong, making them a key nanotechnology structure.
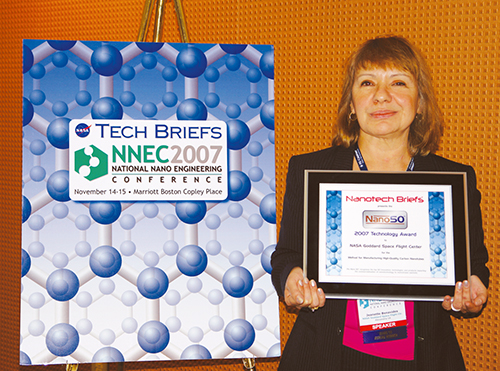
Inventor Jeannette Benavides was honored at the Nano 50 Awards ceremony.
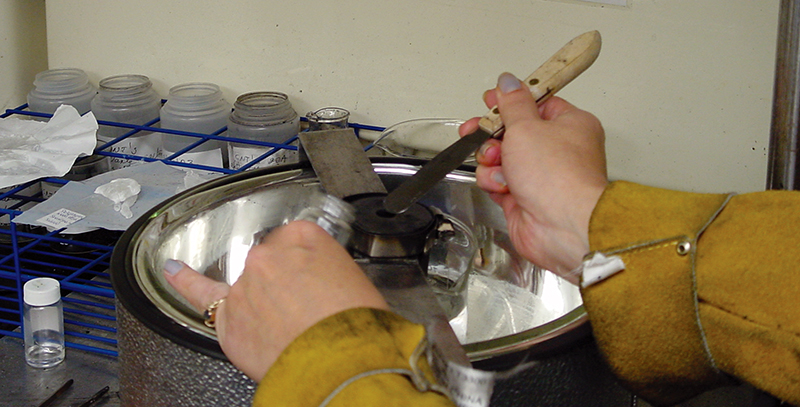
Retired Goddard Space Flight Center researcher Jeannette Benavides prepares her award-winning, low-cost process for manufacturing high-purity, single-walled carbon nanotubes. This innovative manufacturing process uses helium arc welding to vaporize a carbon rod (anode), with the nanotubes forming in the soot deposited onto a water-cooled carbon cathode.