Think Tanks
Storage tanks are absolutely critical to the needs of the petroleum and chemical industry. However, they must be periodically inspected in order to prevent leakage that could result in soil and groundwater contamination. Present inspection methods require that tanks be completely drained and then cleaned before inspection workers can enter the tank. The workers then conduct an in-depth visual inspection to search for flaws. This method presents a serious health risk as residual contaminants can lead to asphyxiation or even explosion.
A new inspection robot from Solex Robotics Systems, of Idaho Falls, Idaho, was designed to eliminate hazardous inspections. The submersible robot, named Maverick, is used to inspect the bottoms of petroleum and chemical storage tanks, keeping the tanks operational during inspection.
Maverick was developed through an agreement between the Idaho National Engineering and Environmental Lab and Solex's parent company, Solex Environmental Systems. By working with NASA/MSU TechLink, of Bozeman, Montana, Solex Robotics gained NASA assistance under a Space Act Agreement from Johnson Space Center.
Maverick's first swim lesson took place at the Johnson Neutral Buoyancy Laboratory, a 40-foot-deep, 6.5-million-gallon pool used to simulate weightlessness. NASA provided the unique testing capabilities that could not be offered elsewhere. Because of Maverick's many control and supply hoses, Solex was interested in relating NASA's experience with tether management back to their robot. Should its hoses become entangled, the tanks would have to be drained and refilled; so Maverick had to prove extremely efficient in managing its lines. Needless to say, Maverick took to the water like a fish and is now able to provide services that will make manual tank inspections obsolete.
During a typical Maverick inspection, the robot is lowered into the full storage tank. With traction wheels, it moves across the tank floor using a specialized sensor and imaging system to inspect the welded steel of the tank, carefully searching for corrosion and wear. Ultrasound technology measures the thickness of the metal. While the inspection is conducted, Maverick's remote human operators remain safe outside of the tank.
The risk to human health and life is now virtually eliminated. The risk to the environment is also minimal because there is a reduced chance of spillage from emptying and cleaning the tanks, where previously, tons of pollutants were released through the process of draining and refilling.
Using Maverick also saves about 80 percent of the cost associated with inspections. The costs of draining and cleaning the tank, combined with lost revenues from downtime, can be upwards of $50,000 to $500,000 per tank. These time-consuming, labor-intensive, and costly steps are no longer necessary since the tanks remain operational while Maverick is in use.
As Maverick changes the face of tank inspection, it strengthens the robotic inspection standard set forth by the American Petroleum Institute.
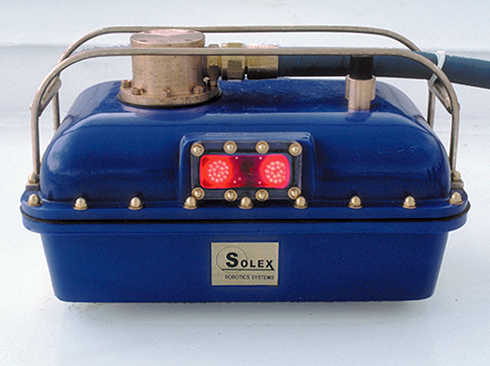
The submersible Maverick robot allows for the safe inspection and cleaning of storage tanks.