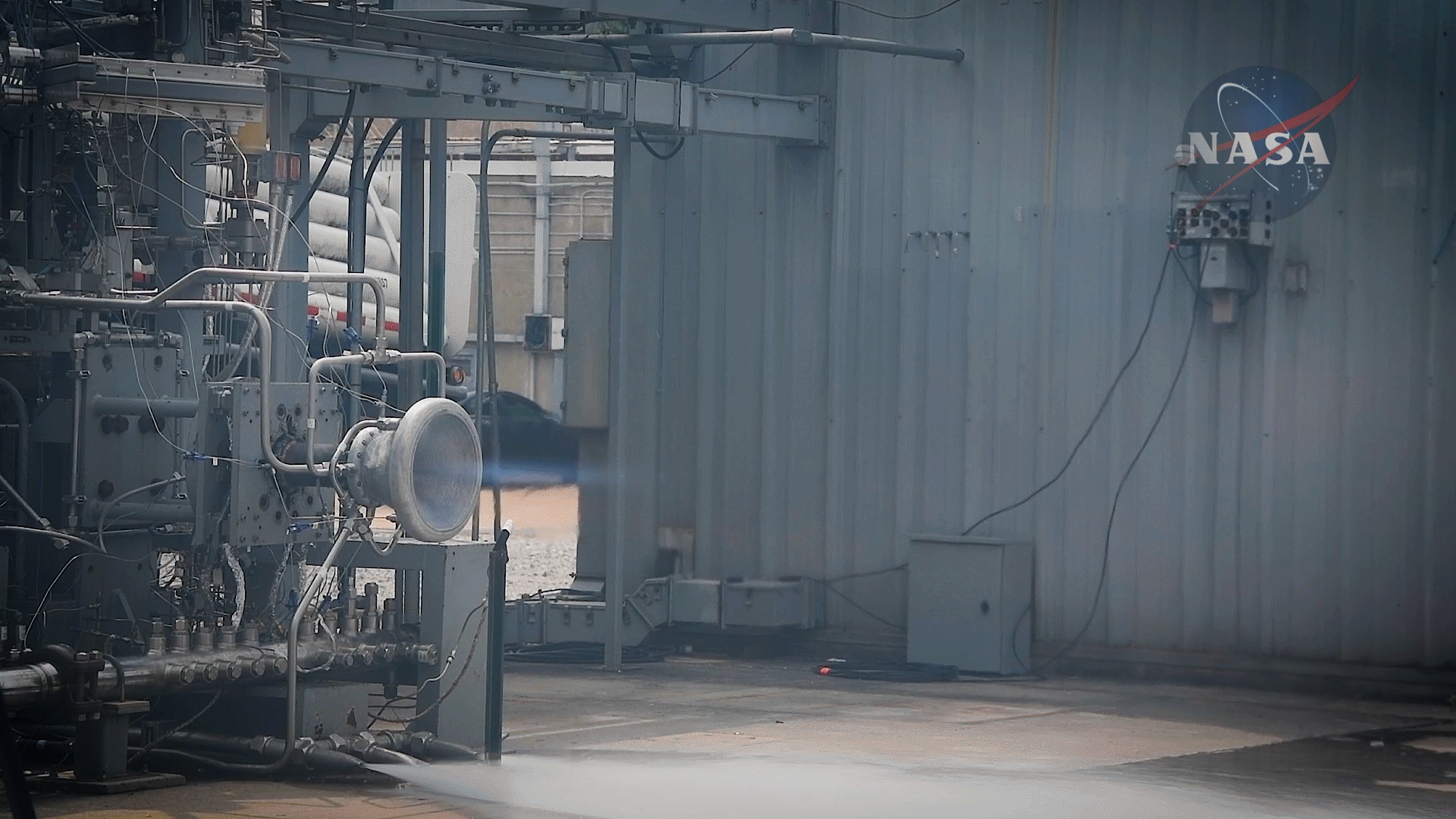
3D Printed Engines Propel Next Industrial Revolution
Subheadline
Converging efforts to 3D print engines promise major savings in rocketry and beyond
In the fall of 2023, NASA hot fire tested an aluminum-based, 3D printed rocket engine nozzle. What made the event remarkable is that aluminum isn’t typically used for additive manufacturing because the process causes it to crack, and it isn’t used in rocket engines due to its low melting point. Yet the test was a success.
The new possibility of printed aluminum engine parts will mean significant savings for NASA in terms of time, money, and, most importantly, the weight of future spacecraft. And Elementum 3D Inc., a partner on the project, is now bringing the benefits of that technology to its customers, including not only rocket engine manufacturers but also makers of race cars, lighting fixtures, computer chips, and more.
NASA’s Marshall Space Flight Center in Huntsville, Alabama, has been working on making engines with 3D printing — also known as additive manufacturing — for several years. NASA is interested in the technique because it would allow engines to be developed and built much more quickly, and they could be made in a few large pieces rather than hundreds of small components fastened together. The ability to print engine parts with aluminum promises all these advantages, along with substantial weight savings.
This was the culmination of a relationship between NASA and Elementum 3D that began shortly after Jacob Nuechterlein founded the company in 2014 with the goal of expanding the number and quality of materials available for 3D printing. In its early days, the Erie, Colorado-based company worked on infusing alloys — mostly aluminum — with particles of other materials to alter the metal’s properties and make it amenable to additive manufacturing. This became the company’s signature Reactive Additive Manufacturing (RAM) process. Without this treatment, aluminum alloys cannot be welded and therefore can’t be 3D printed.
The work drew the attention of the Materials Development and Manufacturing Technology Group at NASA’s Jet Propulsion Laboratory in Southern California, which became the RAM technology’s first customer. Soon, JPL qualified the RAM version of a common aluminum alloy for 3D printing. “NASA was one of the very first early adopters, which helped us translate our understanding and findings to then find commercial customers,” said Nuechterlein.
Engine Printing Takes Off
One company whose interest was piqued was Masten Space Systems, which ended up working with Elementum 3D on a couple of NASA-funded projects before being acquired by another company in 2022. In 2017, the two companies won Tipping Point funding from the space agency to work on a 3D printed aluminum rocket engine, the experimental Broadsword engine that had begun under military funding. That engine, printed from one of Elementum 3D’s earliest metal alloy composites, was tested in late 2019. It operated at lower chamber pressures than an engine would in real-world applications but began to prove the viability of the 3D printed, aluminum-based engine concept.
Meanwhile, a team at Marshall was working with a 3D printing company called RPM Innovations to adapt an emerging metal additive manufacturing technology, known as laser powder directed energy deposition (LP-DED), to print entire rocket engines from various alloys. LP-DED had the potential to print much larger pieces than laser powder bed fusion, the technique used to build the Broadsword engine, but it needed to be refined. The Rapid Analysis and Manufacturing Propulsion Technology (RAMPT) initiative spent about five years honing LP-DED printing and building larger and larger parts, ultimately leading to a nozzle five feet in diameter and selection as NASA’s 2024 Invention of the Year.
The Next Industrial Revolution
In early 2021, the LP-DED process was maturing, and an Announcement of Collaborative Opportunity (ACO) was awarded to Elementum 3D to modify its RAM technology for this new 3D printing technique. This was the Reactive Additive Manufacturing for the Fourth Industrial Revolution (RAMFIRE) project that culminated with hot fire testing in late 2023. Overseeing the work was Paul Gradl, a principal propulsion engineer at Marshall, who was also the principal investigator for RAMPT.
Elementum 3D reengineered its A6061 RAM2 aluminum alloy powder for the large-scale printing process, and RPM Innovations again provided the printing technology. As an ACO, RAMFIRE was managed by Marshall with costs split between NASA and the participating companies.
“We went through various iterations of the powder to make sure it flowed in the LP-DED machines, and there are a lot of challenges with that,” said Gradl. “So we basically had to reinvent the way the powder was being manufactured to make it usable for the LP-DED process.”
Aluminum weighs about a third as much as the iron-nickel-based alloys used in RAMPT, and Elementum 3D’s new LP-DED-printable materials can now offer that weight savings to NASA, commercial rocket builders, and others as a result of all this work.
Cutting weight at this scale has major implications for space missions because it means they can carry that much more payload.
Rocket Tech RAMs Its Way into New Markets
The work got the attention of Ball Aerospace, which is now using the same aluminum alloy that was reengineered for RAMFIRE to print large satellite components.
Not by accident, A6061 is one of the world’s most commonly used aluminum alloys, and the RAMFIRE work has now made it available for large-scale 3D printing in industries beyond aerospace. Elementum 3D already had customers for its original A6061 RAM2 alloy in the microchip manufacturing industry, where aluminum is used in components that handle caustic materials, and its most common application is in parts for Formula 1 race cars, where it can replace heavier steel parts to save weight. Neuchterlein said some of these companies are now investigating the possibility of using the reengineered version of the alloy for LP-DED printing.
Meanwhile, the company Ceramic Disc Technology is using the printable aluminum alloy refined under Tipping Point funding, known as A1000-RAM10, in aftermarket brake rotors for the Dodge Challenger SRT Hellcat, where it offers advantages in weight, strength, wear resistance, thermal conductivity, and temperature tolerance. Nuechterlein said other automakers are looking at it as a lighter-weight option for high-strength suspension and structural components.
Another company is turning A1000-RAM10 into prototype lighting fixtures because it’s inexpensive, scratch-resistant, and strong without requiring heat treatment, and because 3D printing allows for designs that are otherwise impossible.
“We’re not just building for rocket industries,” said Anthony Manerbino, senior materials and applications engineer at Elementum 3D. “We’re building materials and alloys that can help people in their everyday life.”
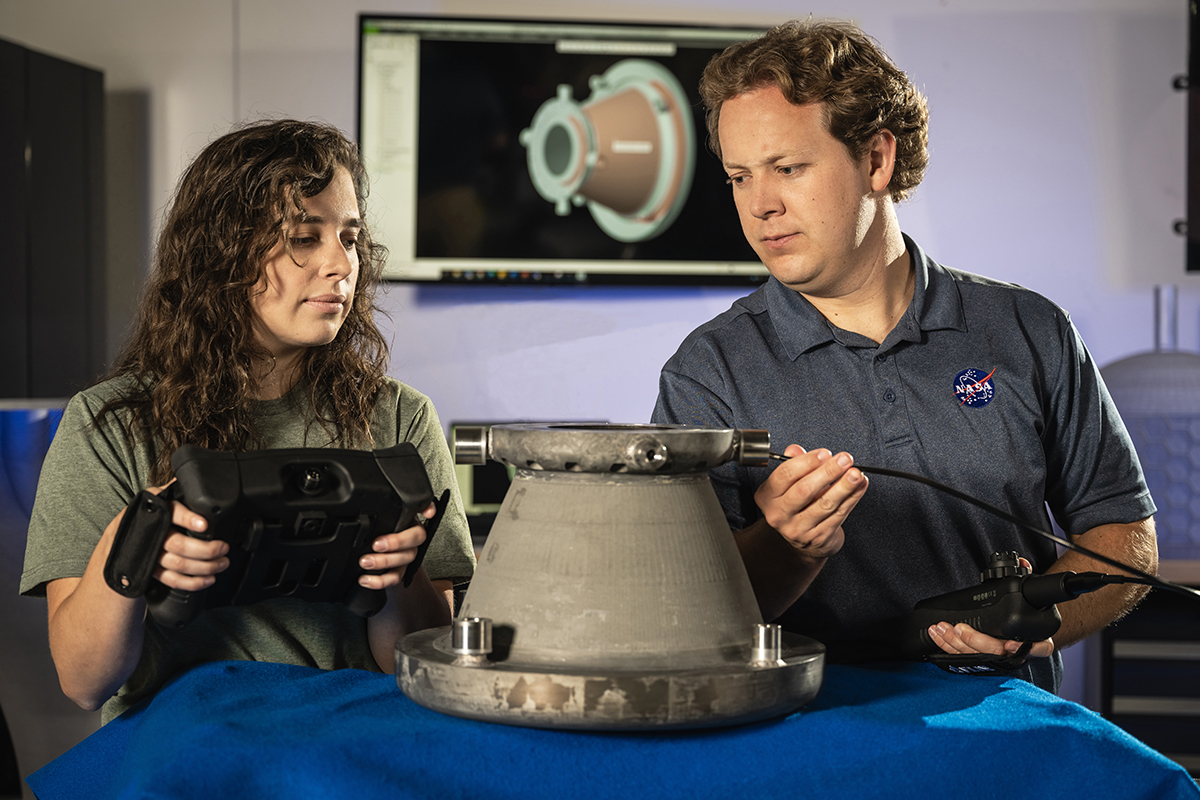
NASA engineers Tessa Fedotowsky and Ben Williams inspect an aluminum nozzle that was 3D printed under Marshall Space Flight Center’s Reactive Additive Manufacturing for the Fourth Industrial Revolution (RAMFIRE) project, following its successful hot fire testing. Credit: NASA
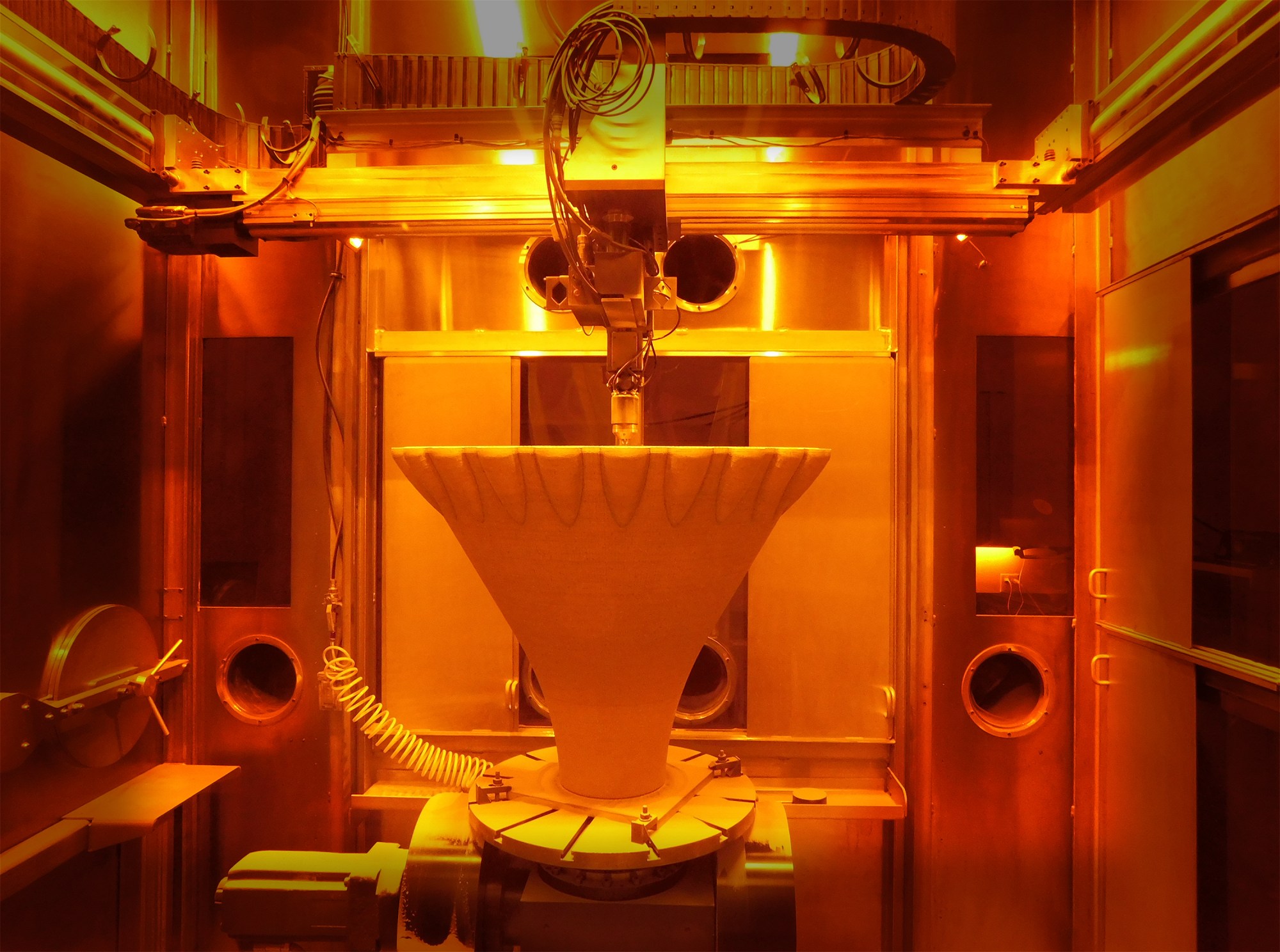
A laser powder directed energy deposition (LP-DED) 3D printer at RPM Innovations’ facility additively manufactures a large-scale aerospike rocket engine nozzle from one of Elementum 3D’s specialized, 3D printable aluminum alloys. Credit: RPM Innovations Inc.

This 3D-printed aluminum nozzle was then welded with wire from Elementum 3D spinoff Fortius Metals. Credit: NASA
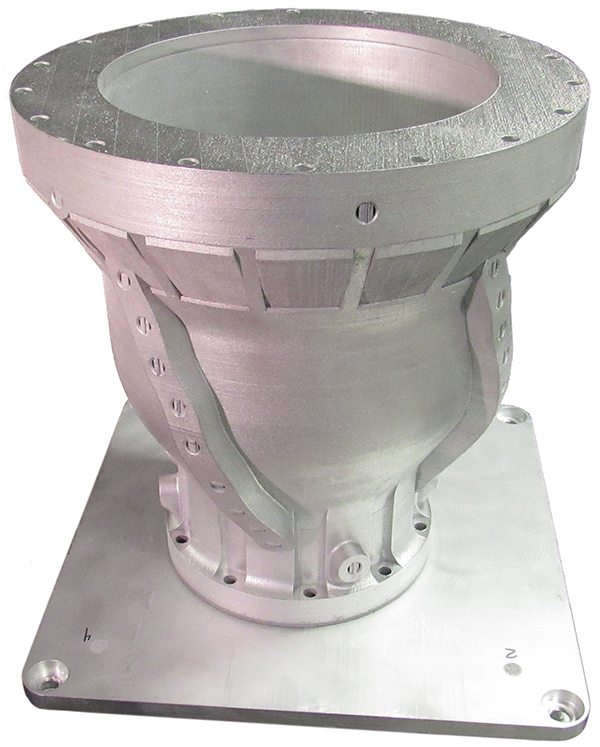
Under Tipping Point funding from Marshall, Elementum 3D worked with Masten Space Systems to 3D print this experimental rocket engine, known as Broadsword, from Elementum’s A1000-RAM10 3D printable aluminum alloy. Credit: Masten Space Systems Inc.
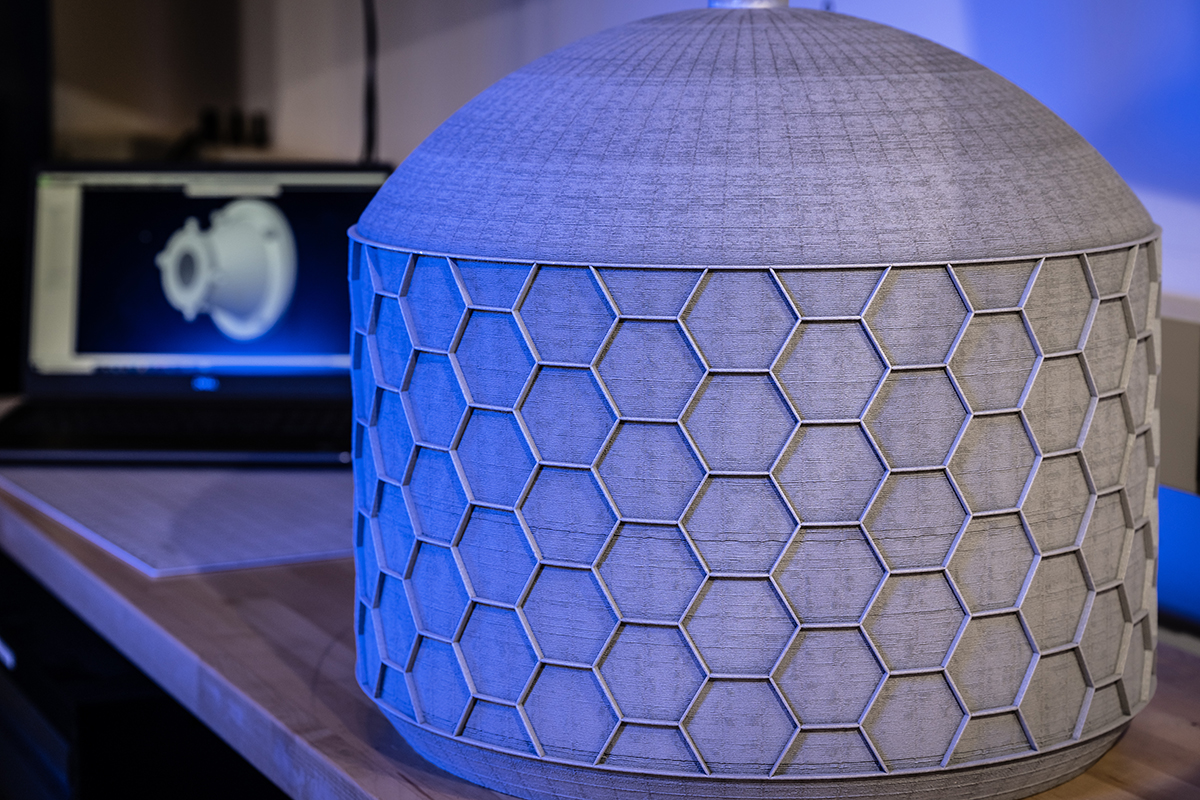
This vacuum jacket manufacturing demonstrator tank, made for cryogenic fluids, was 3D printed at Marshall with Elementum 3D’s A6061 RAM2 aluminum alloy. Credit: NASA
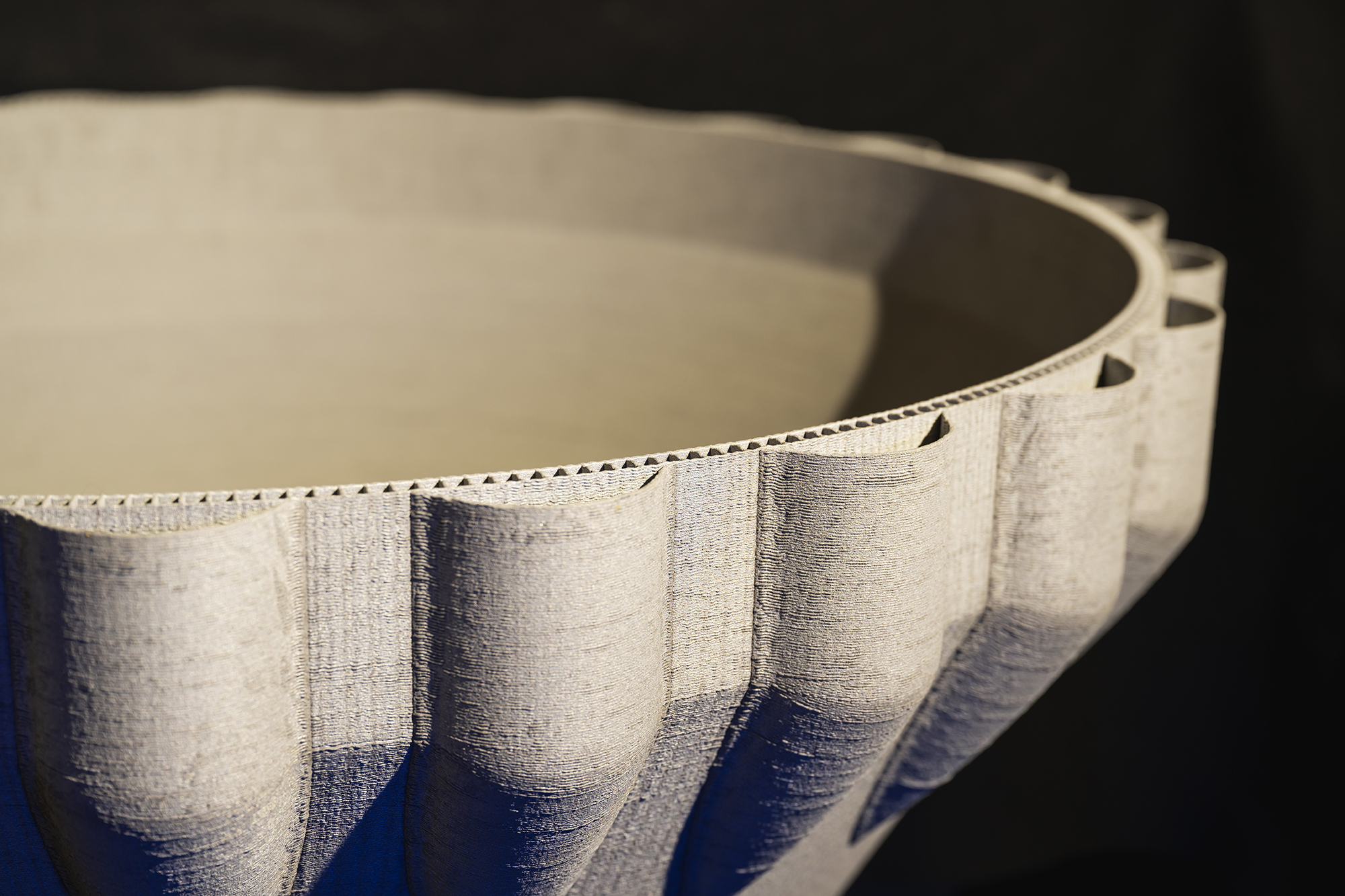
Thin as it is, the wall of this 3D printed aluminum rocket engine nozzle is actually hollow, filled with tiny channels that the cryogenic fuel flows through to cool the nozzle. Credit: NASA
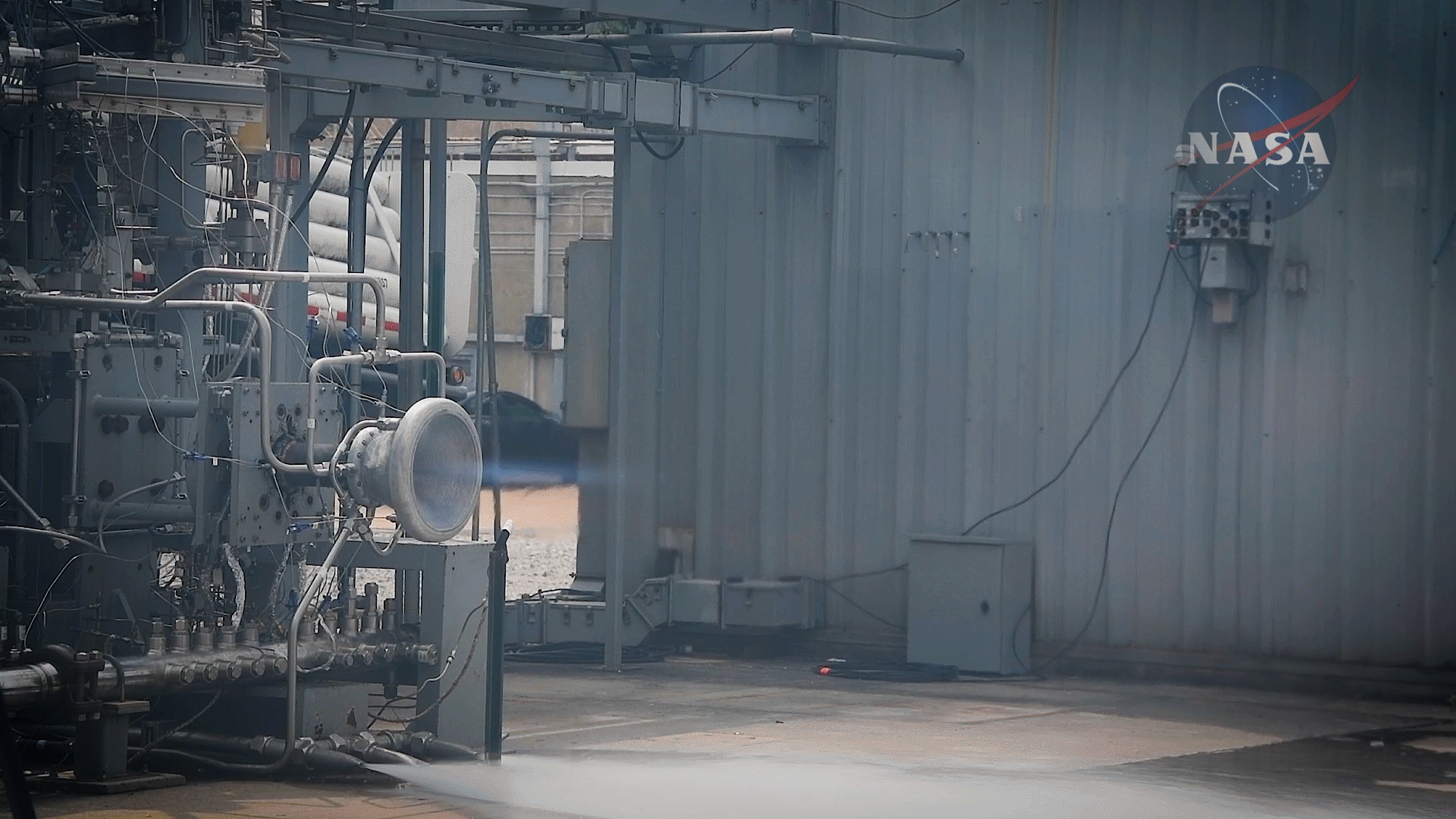
A rocket engine nozzle 3D printed from Elementum 3D’s A6061 RAM2 aluminum alloy undergoes hot fire testing at Marshall. Credit: NASA