Improving the Flow
Originating Technology/NASA Contribution
In early 1995, NASA’s Glenn Research Center (then Lewis Research Center) formed an industry-government team with several jet engine companies to develop the National Combustion Code (NCC), which would help aerospace engineers solve complex aerodynamics and combustion problems in gas turbine, rocket, and hypersonic engines. The original development team consisted of Allison Engine Company (now Rolls-Royce Allison), CFD Research Corporation, GE Aircraft Engines, Pratt and Whitney, and NASA. After the baseline beta version was established in July 1998, the team focused its efforts on consolidation, streamlining, and integration, as well as enhancement, evaluation, validation, and application. These activities, mainly conducted at NASA Glenn, led to the completion of NCC version 1.0 in October 2000.
NCC version 1.0 features high-fidelity representation of complex geometry, advanced models for two-phase turbulent combustion, and massively parallel computing. Researchers and engineers at Glenn have been using NCC to provide analysis and design support for various aerospace propulsion technology development projects. NASA transfers NCC technology to external customers using non- exclusive Space Act Agreements. Glenn researchers also communicate research and development results derived from NCC’s further development through publications and special sessions at technical conferences.
Partnership
A Space Act Agreement between Glenn and Flow Parametrics, LLC, enabled the New Castle, Delaware-based company to commercialize the NCC. Engineers from Glenn’s NCC team provided Flow Parametrics with technical support in accordance with the Space Act Agreement as the company developed its product, the FPVortex™ Computational Fluid Dynamics (CFD) Flow Solver. FPVortex particularly benefited from NASA’s research efforts in the computation and simulation of propulsion system flow fields. Through the terms of the Space Act Agreement, the company’s combustion and modeling engineers continue to frequently exchange technology and modeling ideas with Glenn’s team, further improving the code.
Product Outcome
FPVortex provides design engineers and scientists with a detailed understanding of complex flow fields, leading to design and performance improvements in many types of flow devices. Flow Parametrics originally developed FPVortex to solve the flow fields in gas turbine fuel nozzles, combustors, diffusers, and augmentors. Due to the inherent geometric complexity of such devices, it was necessary to closely couple the flow solver with the types of geometry representations exported by computer-aided design, and to utilize the output of grid generators formerly used in the finite-element analysis field.
After this was completed, the company soon realized that the FPVortex code could be applied to a very wide range of flow problems, from low-speed laminar flows to hypersonic turbulent flows with chemical reactions, including liquid spray droplet tracking, evaporation, mixing, and combustion. Engineers added advanced numerical simulation methods to speed up the code execution, including parallel processing over networked computer processing units and a versatile grid adaption strategy for mesh refinement based on flow variable gradients, and near-wall grid clustering for improved resolution of boundary layers and heat transfer effects.
With the successful development of FPVortex, Flow Parametrics met its goal of providing a state-of-the-art computational combustion dynamics capability that meets designer requirements for geometric model accuracy, turnaround time for cases, and solution accuracy. While the product is targeted at PC computing hardware, UNIX versions of the code can be made available for special purposes. The code is easily coupled with commercially available pre- and post-processing tools, which together form a cost-effective solution to complex, large-scale flow simulation problems.
FPVortex has been successfully applied to design problems in the aerospace propulsion, automotive, and land-based power generation industries. In addition to solving complex aerodynamics and combustion problems in engines, FPVortex’s applications extend to other market sector areas such as heat exchangers, particle separation machinery, land speed record vehicles, and medical devices, to name just a few. The code is being applied routinely in design analysis and optimization studies, as its capabilities continue to expand. New modeling capabilities include advanced finite-rate chemistry for hydrocarbon fuels, conjugate heat transfer for solving solid boundary temperature distributions, and automated liquid fuel spray cone parameter specifications. An increasingly popular use of the code is for unsteady flow analysis and design-oriented studies of pollutant emissions formation and transport.
FPVortex is available in executable form, under license from Flow Parametrics. The company provides full turn-key solutions for CFD-code application, including training in the use of its software, and has the flexibility to tailor FPVortex’s use to specific applications, providing expert engineering consulting services to industry for advanced projects.
FPVortex™ is a trademark of Flow Parametrics, LLC.
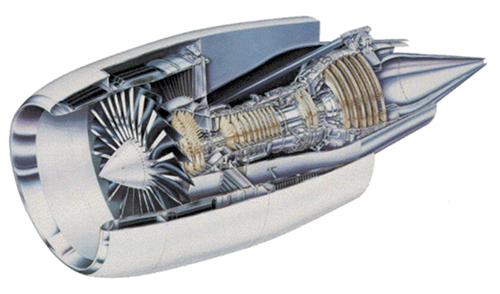
FPVortex™ solves complex aerodynamics and combustion problems in engines.
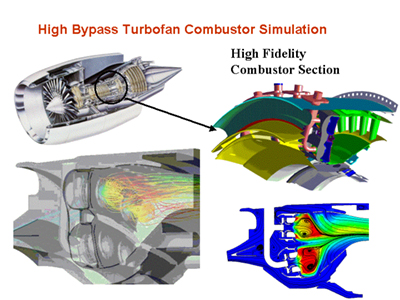
By providing design engineers with a detailed understanding of complex flow fields, FPVortex™ facilitates design and performance improvements in many types of flow devices.