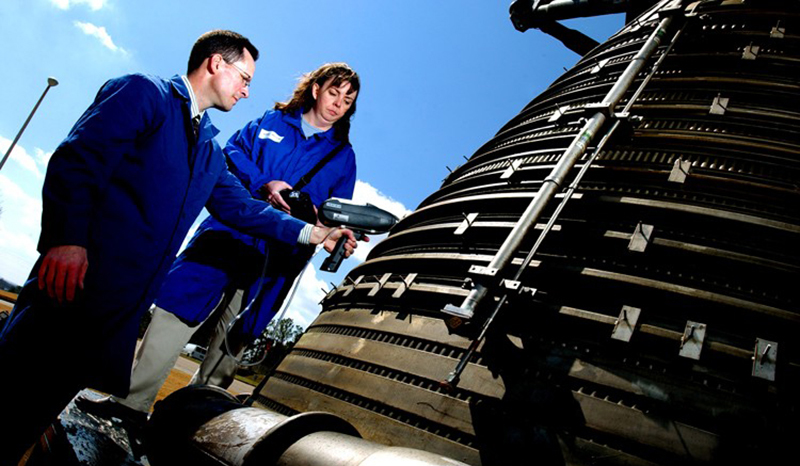
Material Analysis and Identification
Originating Technology/ NASA Contribution
KeyMaster Technologies, Inc., develops and markets specialized, hand-held X-ray fluorescence (XRF) instruments and unique tagging technology used to identify and authenticate materials or processes. NASA first met with this Kennewick, Washington-based company as the Agency began seeking companies to develop a hand-held instrument that would detect data matrix symbols on parts covered by paint and other coatings. Since the Federal Aviation Administration was also searching for methods to detect and eliminate the use of unapproved parts, it recommended that NASA and KeyMaster work together to develop a technology that would benefit both agencies.
KeyMaster agreed to meet with NASA, sharing the opinion that its XRF instrument could be adapted to fit these needs. Up until that point, the company’s instrument served extensively as an alloy analyzer in the metals industry.
Partnership
In January 2002, KeyMaster representatives visited NASA Marshall Space Flight Center’s Technology Transfer department to demonstrate their standard XRF instrument. The NASA participants, including technical personnel from the Engineering Directorate and the Science Directorate, were particularly interested in the instrument’s portability and capability to quickly analyze the composition of most materials in the environment. The group recognized the instrument could have an immediate benefit to NASA for analyzing materials and avoiding many hardware nonconformance issues.
After NASA and KeyMaster determined that merging their technologies could provide beneficial new capabilities for both NASA’s Space Flight program and the commercial market, they signed a Space Act Agreement in March 2002 establishing them as full partners in a research and development environment. The agreement stated that NASA and KeyMaster would work together on the increased capability of the hand-held XRF instrument, sharing any intellectual property that resulted, as well as the cost. NASA would purchase the parts and components for the prototypes, while KeyMaster would provide the design, engineering, and assembly services.
In June 2002, the company demonstrated its XRF instrument to personnel from NASA’s Reusable Solid Rocket Motor (RSRM) project office at Marshall. The instrument successfully identified and matched six samples of Marshall weld rods. The RSRM personnel then began producing bolts, fasteners, and other items that had been the subjects of recent materials problems. The XRF determined the composition of the items in only a few seconds and to a degree of accuracy within 1 percent of the Material Safety Data Sheets. Based on this meeting, the participants agreed that NASA could benefit from the XRF during the manufacturing of Space Shuttle hardware.
NASA tasked ATK Thiokol, a prime contractor to the RSRM project office, with purchasing a standard XRF instrument from KeyMaster and performing a detailed evaluation to determine the extent of capability and applicability of the technology for aerospace work. The first analyses at Marshall found that advances were needed to extend the instrument’s detection range to include aluminum alloys, since aluminum is used to build the Shuttle’s External Tank, the structure of the orbiter, and parts of the RSRM. However, further tests determined that when the instrument was operated in a vacuum, it would easily analyze the aluminum alloys.
The Marshall Space Shuttle Propulsion Office became involved with the project in order to incorporate a vacuum system with the standard XRF instrument, extending the instrument’s sensitivity to detect elements in the range of aluminum. NASA’s External Tank project office, RSRM project office, and the Space Shuttle Main Engine project office each agreed to purchase a vacuum-assisted instrument if KeyMaster developed it. KeyMaster developed the device, naming it the TRACeR III-V, and delivered three of the products to Marshall in April 2003.
KeyMaster and NASA filed two patent applications, demonstrating that the TRACeR brings value back to NASA in addition to yielding a commercial spinoff. One patent is for intrinsic product authentication through chemical tag identifiers that are converted to bar code language, benefiting primarily the commercial market. The other patent involves the merging of the Marshall innovation (the vacuum assist) to enable the instrument to detect certain low-energy elements or even certain contaminants within NASA hardware. KeyMaster signed an exclusive license to commercialize the technology.
Product Outcome
The TRACeR is now approximately the size of a portable drill, weighing less than 5 pounds. The instrument’s extended detection range has opened the dor to new markets, and KeyMaster has made the product available commercially across the globe. The company sold two devices abroad before the product was even announced in any news releases, and numerous orders were placed following the unveiling of the instrument at the 2004 National Manufacturing Week in Chicago.
In addition to the analysis of metals, sophisticated alloys, and lighter elements such as magnesium and silicon, the TRACeR applies an innovative process of tagging and detecting unique elemental codes for material analysis and identification. The TRACeR has software that allows users to mix chemicals with products to create tag identifiers, which the instrument can then read and convert to bar code language for product identification. In one application, the new instrument can analyze for many of the constituents of pharmaceuticals and read tags that authenticate the product. The automotive industry is exploring the new instrument’s capabilities for material composition analysis as well as its potential for product identification and authentication. The U.S. Department of Defense may be able to apply the device, as it is using lighter materials in product development and needs new ways to analyze their composition. Invisible, intrinsic identification that is detectable by only one method may be the authentication tool of the future. The first application of the product for NASA involved the Shuttle’s Return to Flight activities.
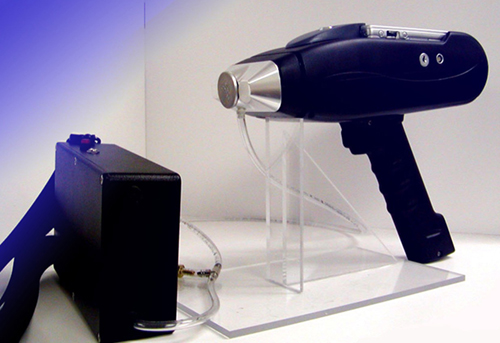
The TRACeR tags and detects unique elemental codes for material analysis and identification.
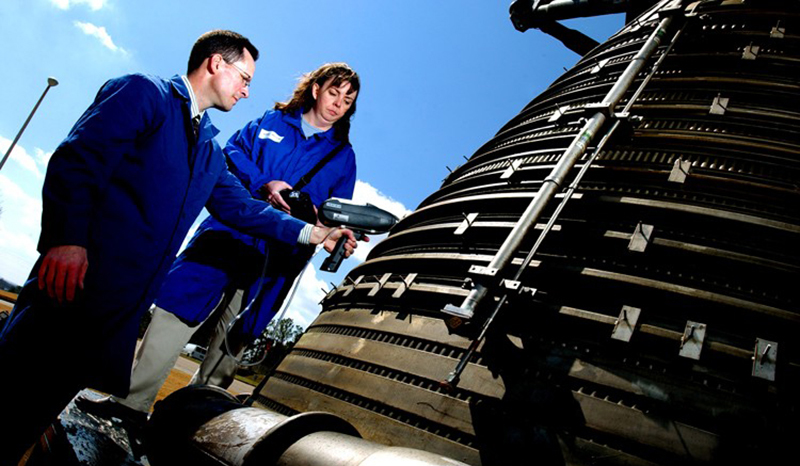
The TRACeR is approximately the size of a portable drill, weighing less than 5 pounds.