Helping Aircraft Engines Lighten Up
Originating Technology/ NASA Contribution
High-temperature polyimide/carbon fiber matrix composites are developed by the Polymers Branch at NASA’s Glenn Research Center. These materials can withstand high temperatures and have good processing properties, which make them particularly useful for jet and rocket engines and for components such as fan blades, bushings, and duct segments. Applying polyimide composites as components for aerospace structures can lead to substantial vehicle weight reductions.
A typical polyimide composite is made up of layers of carbon or glass fibers glued together by a high-temperature polymer to make the material strong, stiff, and lightweight. Organic molecules containing carbon, nitrogen, oxygen, and hydrogen within the polyimide keep the material’s density low, resulting in the light weight. The strength of a component or part made from a polyimide comes mainly from the reinforcing high-strength fibers. The strength of the carbon fibers coupled with the stiffness of polyimides allows engineers to make a very rigid structure without it being massive. Another benefit of a polyimide’s suitability for aerospace applications is its reduced need for machining. When polyimide parts are removed from a mold, they are nearly in their final shape. Usually, very little machining is needed before a part is ready for use.
Partnership
Glenn awarded Maverick Corporation, of Cincinnati, Ohio, a Phase II Small Business Innovation Research (SBIR) contract to develop a family of nontoxic, high-temperature polyimide resins. The company successfully developed polyimides that exhibit high glass transition temperatures and excellent thermal oxidative stability for aircraft applications.
Maverick was then granted $500,000 from the Ohio Technology Action Fund to commercialize the polyimides for high-temperature Resin Transfer Molding, a low-cost manufacturing process commonly used in the aerospace and automotive industries. Glenn also contributed $50,000 to this effort.
In addition to its successful SBIR partnership with Glenn, Maverick also licensed a bundle package of four polymer technologies developed by the Center’s Polymers Branch. Maverick worked with Glenn’s Technology Transfer and Partnerships Office and the Great Lakes Industrial Technology Center (GLITeC) to sign the license. Through the license agreement, researchers in the Polymers Branch extended assistance to Maverick to further develop the technologies. Also as part of the partnership, GLITeC, NASA’s Midwest Technology Transfer Center, worked to help Maverick identify markets and customers.
Product Outcome
Maverick’s BIM product line, a family of affordable, low-toxicity polyimide resins, is the commercial result of the company’s SBIR relationship with Glenn. The technology, which has caught the attention of the aerospace industry, offers high-temperature performance and processing versatility. The resins, which contain no mutagenic or carcinogenic components, can be processed by compression molding, autoclave, solvent-assisted resin transfer molding, and conventional resin transfer molding.
The product line benefits aircraft engine and airframe applications. Since the resins can reduce the cost and weight of aerospace structures, they will help NASA with the development of future space vehicles. The U.S. military may also use the technology in both aircraft and ground transportation applications.
Maverick expects that new products derived from its NASA license will lead to sales of over $50,000 per year within 3 years, with increases from there. One of the first products commercialized from this license is DMBZ, a Glenn-developed/patented polyimide designed for applications requiring short-term exposure to temperatures up to 800 °F.
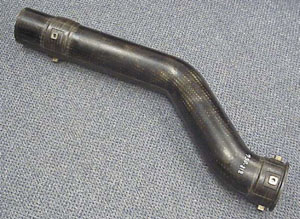
This 4-foot aircraft engine cooling duct was produced using the solvent-assisted Resin Transfer Molding process.