Hybrid Tank Technology
Originating Technology/ NASA Contribution
Researchers have accomplished great advances in pressure vessel technology by applying high-performance composite materials as an over-wrap to metal-lined pressure vessels. These composite over-wrapped pressure vessels (COPVs) are used in many areas, from air tanks for firefighters and compressed natural gas tanks for automobiles, to pressurant tanks for aerospace launch vehicles and propellant tanks for satellites and deep-space exploration vehicles.
NASA and commercial industry are continually striving to find new ways to make high-performance pressure vessels safer and more reliable. While COPVs are much lighter than all-metal pressure vessels, the composite material, typically graphite fibers with an epoxy matrix resin, is vulnerable to impact damage. Carbon fiber is most frequently used for the high-performance COPV applications because of its high strength-to-weight characteristics. Other fibers have been used, but with limitations. For example, fiberglass is inexpensive but much heavier than carbon. Aramid fibers are impact resistant but have less strength than carbon and their performance tends to deteriorate.
Partnership
NASA’s Marshall Space Flight Center began doing initial work on the fabrication of hybrid tank structures through independent research and development (IRx) activities with additional support from technology transfer funding called the Technology Investment Projects. However, this IRx activity did not include the necessary depth to understand how a hybrid structure could be produced for pressure vessel applications.
To further the research, Marshall awarded Phase I and Phase II Small Business Innovation Research (SBIR) contracts to HyPerComp Engineering, Inc., a Brigham City, Utah-based company with expertise in the design and development of pressure vessels for commercial applications. HyPerComp Engineering’s James Patterson and Marshall’s Tom DeLay worked together on the development of a hybrid pressure vessel using a “design of experiments” approach on the type of fibers, resins, and lay-up sequences of the vessels. Over the course of their work, many test vessels were burst tested with and without impact damage. The results led to a refined tank design that NASA found to be beyond state of the art.
The new hybrid pressure vessels are aluminum lined, filament wound, and composite over-wrapped, with high-impact and fire-resistant properties. The unique hybrid technology has the potential to save weight while producing a more robust and safer pressure vessel that is applicable to both NASA and commercial missions. The vessels have passed many of the standard U.S. Department of Trans-portation tests and are currently being tested under more stringent means for military applications.
Product Outcome
NASA licensed the technology to HyPerComp Engineering, allowing the company to manufacture different sizes of the hybrid pressure vessels. HyPerComp Engineering has established a manufacturing sister company, Onyx Technologies, which will bring the technology to the commercial marketplace.
The applications for the new pressure vessels include improved breathing apparatuses for homeland security and firefighting, as well as lighter and safer storage systems for automobiles and buses that run on hydrogen fuel as an alternative energy source. The pressure vessels may be used for chemical processing and pharmaceutical manufacturing, as well as for offshore drilling, oil production, and petroleum refineries. The technology benefits fuel tanks for over-the-road tankers, as the vessels carry more fuel for the same weight as existing tanks. The Gunfire-Survivable Pressure Vessel was designed for robust environments. Its customers include the U.S. military, battlefield environment and fire safety personnel, and the automotive industry.
Another area of significant interest to NASA is regarding cryogenic tank development. Again, Marshall has awarded both a Phase I and Phase II SBIR contract to HyPerComp Engineering for in depth development of cryogenic tanks. The cryogenic tank is being developed for next generation launch systems for the U.S. Department of Defense and NASA. For the Space Agency, the technology can provide fuel tanks for reusable launch vehicles, upper-stage launch vehicles, and other spacecraft.
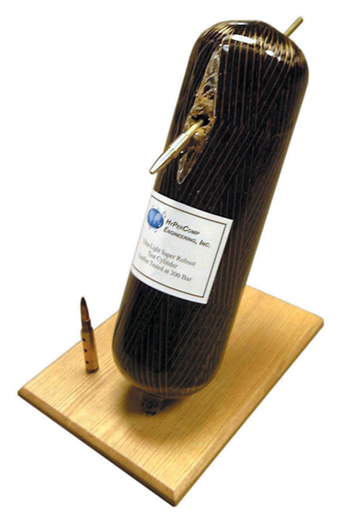
This image shows one of HyPerComp Engineering, Inc.’s test cylinders. Applications for the company’s hybrid pressure vessels include fire safety and the automotive industry.