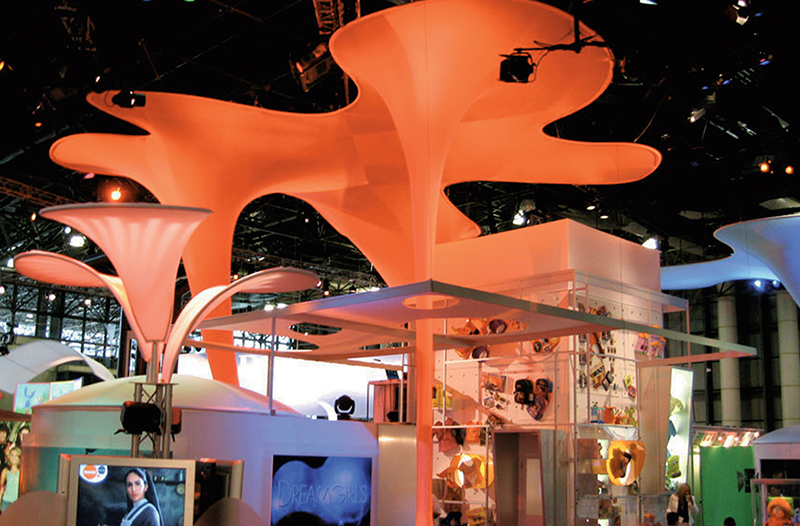
Design Application Translates 2-D Graphics to 3-D Surfaces
Originating Technology/NASA Contribution
When it comes to solving some of NASA’s most challenging technical problems, the mathematical minds that make up the Computational Sciences Branch at NASA’s Glenn Research Center are ready and waiting to crunch some numbers. Calculating complex algorithms and mathematical equations like it’s child’s play, the group has worked out many technical issues for NASA over the years.
Bruce Auer was a member of the Computational Sciences Branch for 43 years until he retired in 2005. When he started in 1962, he worked on a wide variety of problems in the fields of aeronautics and space technology. A key component of his job was developing complex algorithms that contributed to solving mathematical problems and modeling chemical and physical phenomena. Early on, the projects ranged from solving difficult heat equations for rocket nozzle technology used to prevent nozzles from burning up with multiple restarts, to studying cutting-edge turbulent flow theories.
In the late 1980s, Glenn started developing technologies for designing and manufacturing carbon graphite composite turboprop fan blades and turbofan inlet fan blades, ranging in size from 2.5 inches to 30 inches. (Glenn specializes in the development of jet engine and turbomachinery technology.) Some of these projects required making hollow blades with internal passages to dampen jet engine noise. Several years later, in 1994, Auer’s group was called on for help when one of these projects, a joint Glenn-Pratt & Whitney experimental turboprop fan blade project, was not going as expected, because the experimental blades being designed and manufactured at Glenn were failing to meet Pratt & Whitney’s specifications during testing.
The technical shortcomings experienced in this joint project were traced to three-dimensional (3-D)-to-two-dimensional (2-D) commercial flattening software, which was not able to accurately flatten a 3-D surface into a 2-D surface. Flattening software of this nature is required, because the fan blade was being made from 50 to 250 separate 2-D carbon graphite composite sheets, or plies, that were cut and stacked in a mold where heat and pressure was applied to create a solid carbon graphite blade.
According to Auer, to determine any one 2-D pattern, first a 3-D surface internal to the blade had to be computed. Then, this 3-D surface had to be flattened into its corresponding 2-D pattern. When the Glenn engineers making the fan blades could not find a commercial vendor who could supply accurate 3-D-to-2-D software, they came to Auer for a solution. Specifically, the engineers asked Auer to write a 3-D-to-2-D flattening program that could accurately flatten any 3-D ply internal to a blade whose external surfaces had complex, continuously changing double curvatures.
Auer went to work on writing an optimized, 3-D-to-2-D blade-flattening software program that could address the fan blade engineers’ needs. By taking several mathematical algorithms and weaving them together with “tight logic,” he came up with a solution: a program that could handle any 3-D surface fed into it.
Auer considered the outcome to be both simple and sophisticated for flattening. It could be used in either a very straightforward or advanced manner, depending on the user and his or her requirements and applications. He stated that the advantages of the program are that it is highly accurate, fast, and robust. Furthermore, he noted that it can address stretching and shrinking issues, which are inherent in some manufacturing processes.
The software program was successfully put to use in designing and manufacturing blades for the Glenn-Pratt & Whitney joint project, as well as in several other blade-manufacturing projects from other departments within Glenn over the years. All of the great results were adding up and, in 2002, several blade engineers recommended that Auer seek commercial applications for his software program.
Auer agreed with this assessment, so he pursued commercialization of his software through Glenn’s Commercial Technology Office. This office accepted his proposal and arranged for his software program to be featured in the March 2002 issue of NASA Tech Briefs, thus giving it exposure to the outside engineering community.
Partnership
In the spring of 2005, Joseph Settipani was combing the Internet in an effort to track down a software program that could help with the flattening of fabric surfaces and, therefore, help the company cut down production time and limit the waste of materials. During his Internet search, he came across information on Auer’s software for optimal flattening of fan blade patterns. After several correspondences with Auer, Settipani recognized the potential for the NASA software to bolster his Elgin, Illinois-based Fabric Images Inc. fabric-design process.
Additional Internet research brought Settipani to the Great Lakes Industrial Technology Center (GLITeC), which works with regional companies to acquire and use NASA technology and expertise, especially from Glenn. A meeting was arranged between Settipani and Auer.
For the meeting, Auer visited the Fabric Images manufacturing plant and learned all about the company’s design and manufacturing processes. Auer saw the value that his software could bring to Fabric Images and determined that the company was a great fit as a commercial partner. GLITeC subsequently facilitated an agreement that would entitle the company to utilize the NASA software code as a resource for its commercial applications.
Product Outcome
Fabric Images specializes in the printing and manufacturing of fabric tension architecture for the retail, museum, and exhibit/trade show markets. The company has the difficult task of correctly designing 2-D graphics for 3-D surfaces. Since the displays it assembles serve as advertisements for its clients, there is the necessity of making sure the words and logos are visually correct on the 3-D surfaces.
The goal in the design process is to achieve 2-D template-based production, based on the corresponding 3-D surface geometry. The advantages of template-based production are many, but there are many variables involved that complicate the process, as well. In order to control variables during actual production, Fabric Images now relies on a novel and reliable flattening process based on the NASA software.
Fabric Images’ fabric-flattening design process begins with the modeling of a 3-D surface based on computer-aided design specifications. The surface geometry of the 3-D model is utilized in the formation of a 2-D template, similar to NASA’s flattening process. This template or pattern is then applied in the development of a 2-D graphic layout. To achieve the desired visual graphic look on a 3-D surface, repositioning and distortion of 2-D graphics is necessary. When printed fabric graphics are not repositioned and/or not distorted for 3-D construction, fabric is wasted and money is lost in having to initiate graphic layouts and another production run.
Fabric Images developed a 2-D template pattern-based production process with the use of the NASA technology as a resource. This eliminated an entire step from the actual fabric sewing/construction process, creating an 11.5-percent time savings per project. Additional benefits included less material wasted and the ability to improve upon graphic techniques and, thus, offer new design services.
Today, Fabric Images is wowing its business-to-business partners and end-user clients with intricate and innovative displays and designs, using the NASA technology. Partners include Exhibitgroup/Giltspur (end-user client: TAC Air, a division of Truman Arnold Companies Inc.), Jack Morton Worldwide (end-user client: Nickelodeon), as well as 3D Exhibits Inc., and MG Design Associates Corp.
Although the full potential of Auer’s “flattening math engine” has yet to be fully realized by Fabric Images, Marco Alvarez, the company’s president, believes the future of template-based production will be bright.
“The 3-D-to-2-D templates have given us tools to take our production to a new level of efficiency. They have also opened a new avenue of business in providing graphics for difficult, amorphic shapes,” stated Alvarez.
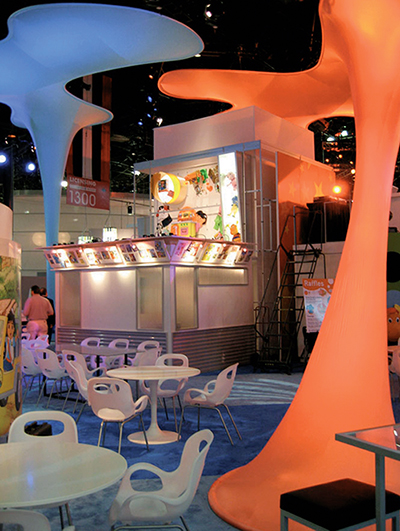
NASA helped overcome the unique design challenges of creating 3-D designs out of 2-D materials.
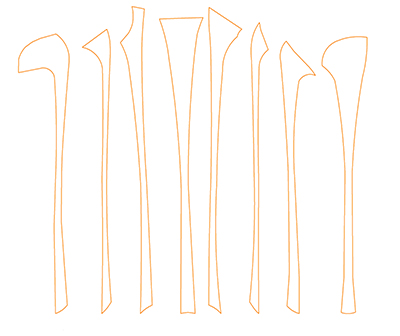
One of the technical challenges faced by the Computational Sciences Group at Glenn Research Center was creating software that was able to accurately flatten a 3-D surface into a 2-D surface.
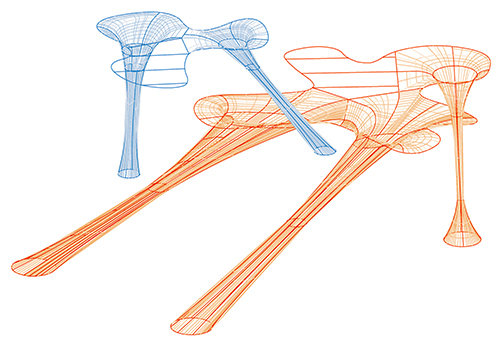
Fabric Images Inc. has the difficult task of designing the graphics for complex displays before it can see the actual, complete, 3-D displays come togethe
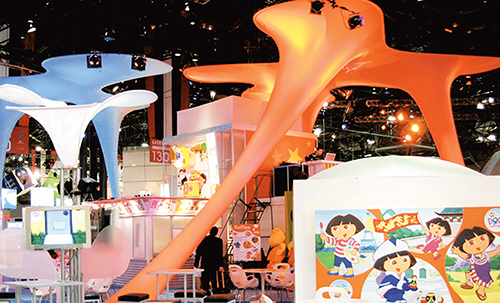
Fabric Images Inc. impresses its clients with intricate and innovative displays and designs.
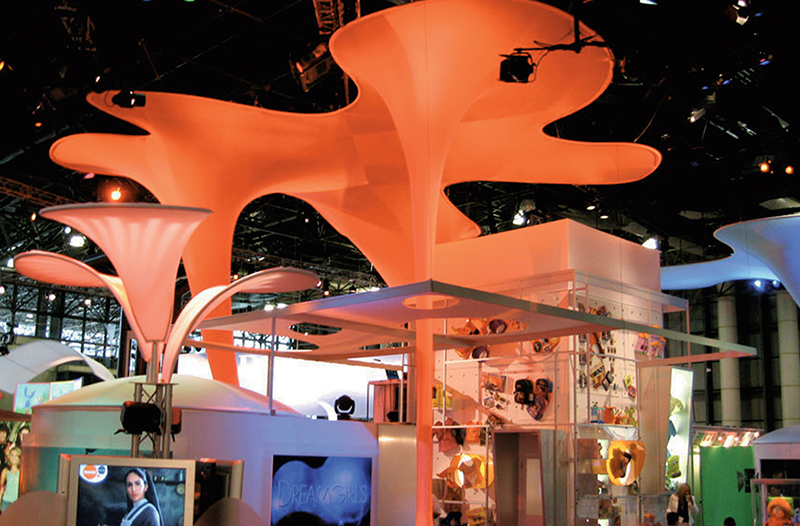
Since the displays Fabric Images Inc. assembles primarily serve as advertisements for its clients, there is the necessity of making sure the words and logos are visually correct on the 3-D surfaces.