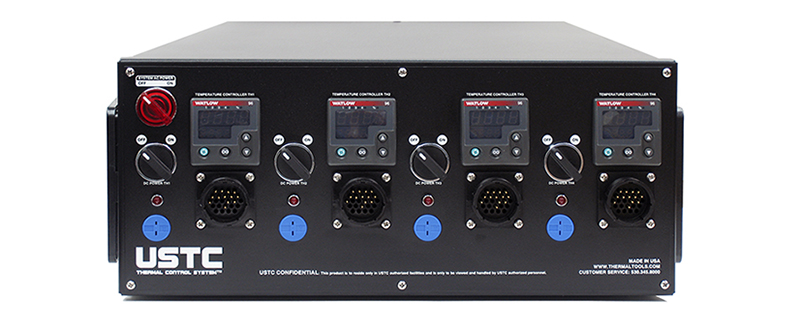
Thermoelectric Devices Advance Thermal Management
Originating Technology/NASA Contribution
When NASA programs need the ultimate reliability to power deep space probes, they repeatedly select thermoelectric (TE) devices as a system component. TE devices heat, cool, and generate electricity when a temperature differential is provided between the two module faces. Using radioactive isotope Plutonium 238 and TE devices to convert waste heat into electricity, NASA has depended on radioisotope thermoelectric generators (RTGs) in 25 U.S. missions since 1961.
NASA relied on RTGs launched in Apollo missions to the Moon, the Viking missions to Mars, and the Pioneer, Voyager, Ulysses, Galileo, and Cassini missions to the outer solar system. More than 30 years from its launch, and well beyond the orbit of Pluto, the RTGs on the Pioneer 10 spacecraft continue to operate.
A project like the Pioneer 10 RTG is an example of the rigorous standards imposed by NASA product specifications and long-life applications that have been known to validate the unique characteristics of TE devices. Like the RTG as a system, the TE device as a component exhibits resilient characteristics. Not only do they have proven long-life performance reliability, they also operate in a vacuum, withstand rigorous vibration, and are relatively insensitive to radiation and other environmental factors.
With confidence, TE devices were integrated into a myriad of niche applications by commercial enterprise. In the 1960s, there was a small handful of TE device manufacturers; in response to wide product utilization, today TE devices are readily available, manufactured by companies around the world.
With the legacy of reliability documented by successful NASA project use, there has been a proliferation of commercialized products using TE devices, and these components have been used in pacemakers, undersea defense and communication systems, and in Arctic weather stations. Where conventional compressor and chemical cooling methods are impractical, TE devices can be switched from coolers to heaters and operate over a broad range of power, while also able to be more temperature precise within tight tolerances than traditional systems. These qualities make TE devices perfect for integration in a wide array of temperature control applications like miniature infrared detectors, circuits in cruise missiles and aircraft, lasers, blood analyzers, sensors, air conditioners, refrigerators, and semiconductor controls.
Partnership
NASA application of TE devices and relative technologies was influential in the products developed by Jim Kerner, chief executive officer and president of the Chico, California-based United States Thermoelectric Consortium Inc. (USTC). Since the debut of his first thermoelectric product programs in 1983, Kerner has built an outstanding international team of individuals who have designed and delivered significant TE device product solutions, and the company continues to grow in the arena of thermal management technologies implemented in military, aerospace, industrial, and consumer product areas.
Kerner has organized several companies in research, development, and manufacture of numerous thermoelectric-based products, including microprocessor validation tools, high-purity water delivery systems, portable refrigerator/warmer units, and precision temperature control (PTC) chambers. In 1988, Spinoff featured the water delivery system and a customized PTC chamber delivered to Ames Research Center, called the Portabator, which was manufactured in support of NASA Space Life Sciences Projects.
In cooperation with NASA Lewis Research Center, now Glenn Research Center, USTC built a gas emissions analyzer (GEA) for that Center’s combustion research laboratory. As with the PTC product line, the GEA integrated TE devices in the design; a specification originated by NASA. This GEA precipitated hydrocarbon particles, preventing contamination that would hinder precise rocket fuel analysis. In addition to providing product development opportunities, affiliation with the NASA Industrial Application Center and Technology Transfer programs have been useful research tools for the company’s subsequent product development programs.
USTC continues to integrate the benefits of TE devices in its current line of thermal management solutions and has found the accessibility of NASA technical research to be a valuable, sustainable resource that has continued to benefit and positively influence its product design and manufacturing.
Product Outcome
TE devices are an important element in the precise temperature control of the USTC test validation tools for thermal management in the semiconductor and information technology industry. A USTC Thermal Tool System can precisely control the temperature of a heat-generated device up to 100 W/cm2 in the range of -30 to 120 °C.
Among the USTC Thermal Tool System products are the Integrated Thermal Management System (ITMS), Hybrid Air Thermal Management System (HATMS), Rack Integrated Thermal Management System (RITMS), Temperature Control System (TCS), and Thermal Heads (TH). Integrating cooling modules and the TCS in one enclosure with liquid as working fluid, combined with TH, the ITMS executes temperature control tasks without other components. Using air as cooling media, the HATMS executes the tasks like ITMS. The RITMS includes a smart TCS unit which automatically adjusts parameters for temperature control, with an ultra-low noise level and low power consumption. The TCS is a standard temperature control unit, and the TH dissipate heat from a heat-generated device, like a computer. The RITMS or TCS, combined with a chiller (or a heat exchanger) and TH, provide a standard way to control the temperature and dissipate heat on electronic components for production validation tests.
The USTC research and design team uses patent-pending dimple, pin-fin, microchannel and microjet structures to develop and design heat dissipation devices on the mini-scale level, which not only guarantee high performance of products, but also scale device size from 1 centimeter to 10 centimeters.
The smart TCS unit in RITMS for temperature control simplifies the operation of the device. USTC provides choices for cooling media (liquid, air, and chilled liquid), high-power level, high-temperature range, fast-temperature response, scalable size, remote control, low noise, highly reliable, low maintenance, and easy operation. USTC also creates, develops, and delivers solutions for custom thermal management requirements.
The USTC team has been constantly innovating with the latest relevant technologies to provide the best thermal solutions for computer, processor, chipset, board, drawer, server, and rack challenges, as well as other thermal management areas like laser, microwave, radar, backup energy storage, and thermo-stabilization systems.
Since 1997, USTC solutions have been integrated into microprocessor tests, validation processes, and design debugging, and have been deployed to all major development centers in the United States and abroad, including to China, the United Kingdom, Israel, India, Malaysia, and the Philippines.
Kerner organized USTC with a vision to build a world-class team of experts to deal with Moore’s Law: as processor speed increases, power and heat will also increase, and at a certain point, processors cannot continue to operate with increased speeds unless thermals are managed. A unique team of scientists and engineers are organized to focus on research and design, as well as the application of new technologies in thermal management.
The USTC team includes 15 Ph.D. scientists and other specialists with core expertise in thermal management, amplified by a wide spectrum of experience in areas including thermophysics, aero and fluid dynamics, porous materials, capillary structures, microchannels, and refrigeration systems. USTC has received over 30 U.S.- and foreign-issued patents and pending patent applications on new methods and devices.
USTC Thermal Tool System™, Integrated Thermal Management System™, Hybrid Air Thermal Management System™, Rack Integrated Thermal Management System™, and Temperature Control System™ are trademarks of United States Thermoelectric Consortium Inc.
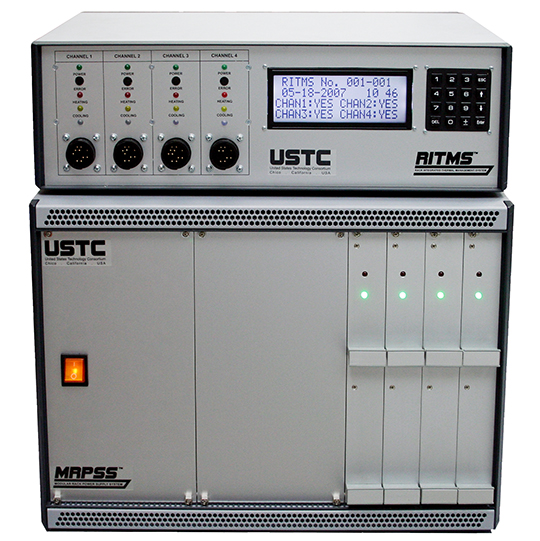
United States Thermoelectric Consortium Inc. (USTC) has experienced great success in the development of thermal management devices based on micro-technologies, like this Rack Integrated Thermal Management System.
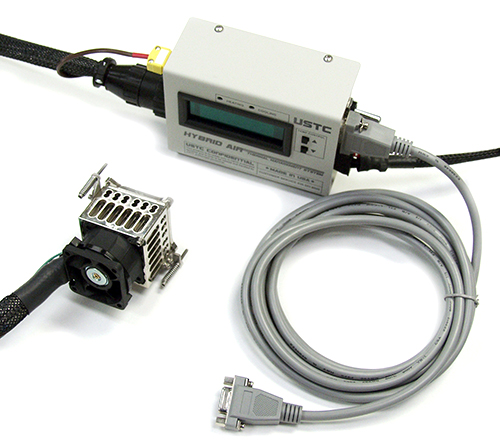
USTC is an experienced provider of fully integrated, turnkey thermal management solutions designed to meet stringent user requirements.
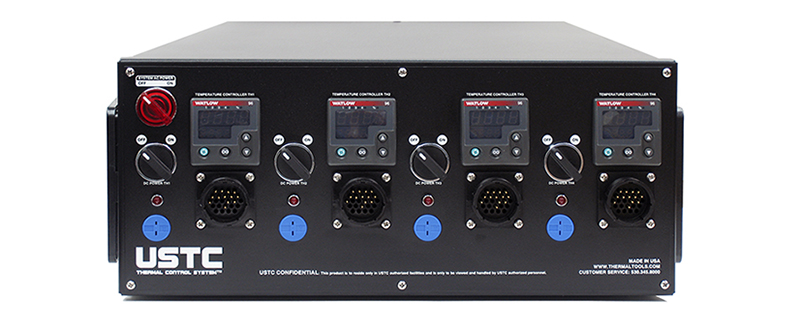
USTC has received over 30 U.S.- and foreign-issued patents and has patent applications pending on new methods and devices.