Computational Modeling Develops Ultra-Hard Steel
Originating Technology/NASA Contribution
Glenn Research Center’s Mechanical Components Branch routinely conducts research on transmissions and gearing for advanced gas turbines, promoting their safety, weight reduction, and reliability. The Mechanical Components Branch is staffed by both NASA and U.S. Army Research Laboratory employees, and the research program is designed and executed to meet the needs of both organizations. The researchers have developed a world-class set of instruments and test devices, including a spiral bevel or face gear test rig for testing thermal behavior, surface fatigue, strain, vibration, and noise; a full-scale, 500-horsepower helicopter main-rotor transmission testing stand; a gear rig that allows fundamental studies of the dynamic behavior of gear systems and gear noise; and a high-speed helical gear test for analyzing thermal behavior for rotorcraft. These are just a few examples of the highly specialized equipment the researchers at the Mechanical Components Branch have at their disposal.
Since 1972, the branch’s spur gear fatigue rig has set the standard for gear surface fatigue experiments, enabling development of robust, efficient, and safe gas turbines and rotorcraft. The test rig provides accelerated fatigue life testing for standard spur gears at speeds of up to 10,000 rotations per minute, and enables engineers to investigate the effects of materials, heat treat, shot peen, lubricants, as well as other factors, on the gear’s performance.
Partnership
QuesTek Innovations LLC, based in Evanston, Illinois, is an innovative materials solutions company that designs and develops new materials in less than 50 percent of the time and at less than 30 percent of the cost of traditional empirical methods.
QuesTek provides unique materials solutions to a variety of customers by using its powerful mechanistic computational models to design steels and alloys to customer requirements. The company’s methodology uniquely allows for design trade-offs, such as steels optimally balanced for strength, toughness, and corrosion resistance. Employing computational materials design techniques, QuesTek uses fundamental thermodynamic and kinetic data to predict alloy microstructures; in contrast to traditional empirical—trial and error—approaches.
QuesTek recently developed a carburized, martensitic gear steel with an ultra-hard case using its computational design methodology, but needed to verify surface fatigue, lifecycle performance, and overall reliability.
The Battelle Memorial Institute, a nonprofit global science and technology enterprise that develops and commercializes technology and manages laboratories for customers, introduced the company to researchers at Glenn’s Mechanical Components Branch and facilitated a partnership allowing researchers at the NASA Center to conduct spur gear fatigue testing for the company.
Testing revealed that QuesTek’s gear steel outperforms the current state-of-the-art alloys used for aviation gears in contact fatigue by almost 300 percent. This testing generated necessary data to demonstrate the superiority of the ultra-hard case alloy and quantified the contact fatigue benefit attainable using QuesTek’s material. However, bending fatigue testing demonstrated that the bending fatigue capability of the new steel was somewhat less than the capability of the current state-of-the-art alloys used for aviation gears. The test data has provided guidance for engineers to select the best combination of properties to satisfy the requirements of a given application.
Product Outcome
With the confidence and credibility provided by the NASA testing, QuesTek is commercializing two new steel alloys. These alloys combine maximum case hardness with a tough, ductile core, promoting high wear and contact fatigue life and offer a 20-percent increase (or more) in gear endurance in high-power density aerospace transmission systems.
Uses for this new class of steel are limitless in areas needing exceptional strength for high-throughput applications. The material is already being used in racing markets. For instance, QuesTek’s C61 material was the power behind the Class 1600 champion in last year’s Baja 1000 off-road race. Aside from racing, this high-performance material is in testing for heavy equipment gearing and in oil/gas gearing applications. NASA is interested in the materials for use in developing vertical takeoff and landing vehicles, based on conventional rotorcraft but with the speed and high-altitude performance of turbo propellers. Advancements in gear design and reliability make possible the development of these highly specialized vehicles.
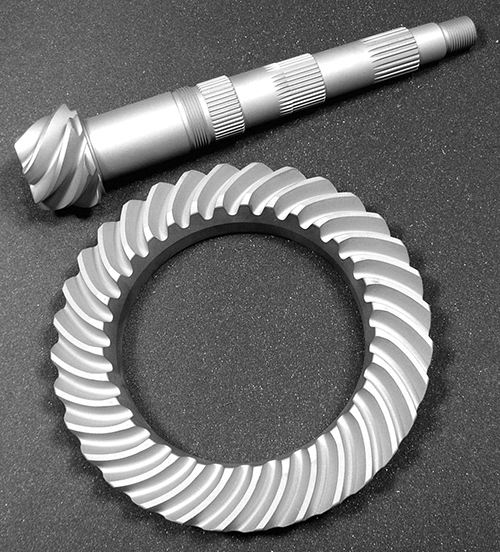
Uses for this new class of steel are limitless in areas needing exceptional strength for high-throughput applications.