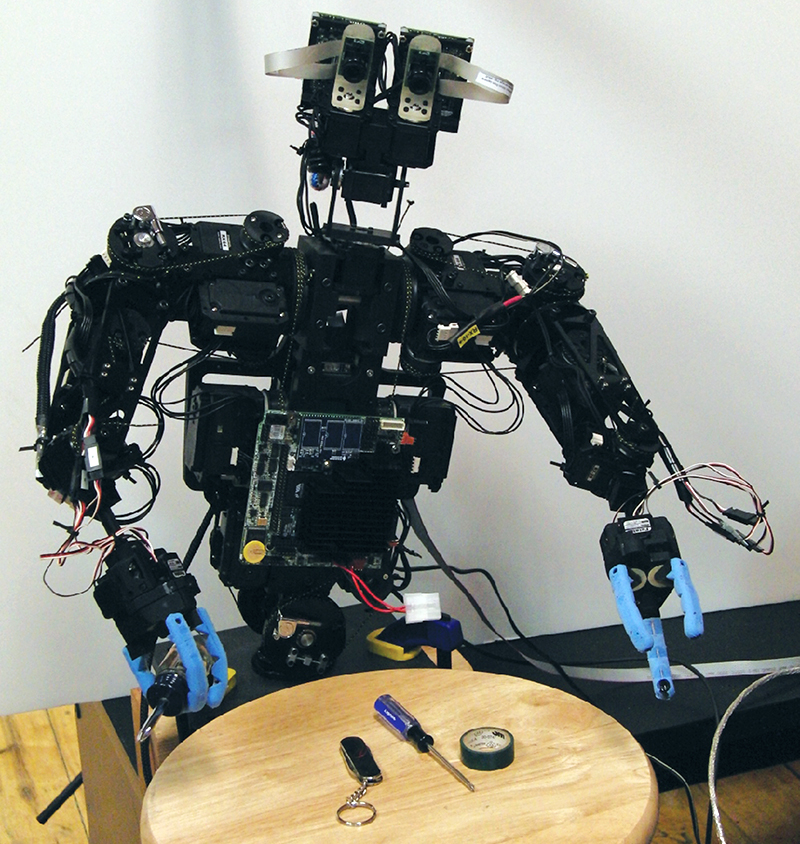
Toolkits Control Motion of Complex Robotics
Originating Technology/NASA Contribution
That space is a hazardous environment for humans is common knowledge. Even beyond the obvious lack of air and gravity, the extreme temperatures and exposure to radiation make the human exploration of space a complicated and risky endeavor. The conditions of space and the space suits required to conduct extravehicular activities add layers of difficulty and danger even to tasks that would be simple on Earth (tightening a bolt, for example). For these reasons, the ability to scout distant celestial bodies and perform maintenance and construction in space without direct human involvement offers significant appeal.
NASA has repeatedly turned to complex robotics for solutions to extend human presence deep into space at reduced risk and cost and to enhance space operations in low Earth orbit. At Johnson Space Center, engineers explore the potential applications of dexterous robots capable of performing tasks like those of an astronaut during extravehicular activities—and even additional ones too delicate or dangerous for human participation. Johnson’s Dexterous Robotics Laboratory experiments with a wide spectrum of robot manipulators, such as the Mitsubishi PA-10 and the Robotics Research K-1207i robotic arms. To simplify and enhance the use of these robotic systems, Johnson researchers sought generic control methods that could work effectively across every system.
Partnership
In 2001, Energid Technologies Corporation, of Cambridge, Massachusetts, was contracted to develop robot control technology through Small Business Innovation Research (SBIR) agreements with Johnson. Providing the company with its first funding, these Phase I and II SBIR partnerships, allowed Energid to build unique robot control and simulation software that is now the basis of the company’s operations and a solution for a host of robotics applications. The company has also received SBIR funding from NASA’s Jet Propulsion Laboratory for additional work related to robotics.
Product Outcome
The human arm is a marvel of engineering; with three joints and seven degrees of freedom (the ability to pivot in seven different ways), the arm’s main purpose is to move the hand, allowing a person to grip and manipulate objects in any number of ways and from any number of angles. A “kinematically redundant” robotic arm with seven degrees or more of freedom is designed for the same purpose: to move its hand or other end effector to accomplish tasks. But without the benefit of the natural programming of the human nervous system that enables a person to pick up a pen or turn a doorknob with hardly a conscious thought, a robot arm’s velocity, force, direction, and other variables must be carefully controlled through complex algorithms. Energid’s patented Actin software, derived from the company’s NASA SBIR work, essentially provides a nervous system for kinematically redundant robotic hardware.
“What our software does is let you think only about the hand while we take care of the robot,” explains James English, Energid’s president and chief technical officer. The Actin toolkit lets the operator put constraints on a robot’s motion—such as where the hand should be, how it should move—and then automatically converts those constraints into real-time algorithms to control joint motions for the robot to achieve the desired actions. The result is fluid motion that optimizes key qualities like strength and accuracy while avoiding collisions and joint limits. Actin provides control capabilities for virtually any kind of robot (fixed-base, wheeled, walking), any joint type or tool type, and with any number of joints, degrees of freedom, and bifurcations (branches).
In addition, the software provides machine vision and 3-D visualization tools, as well as powerful simulation capabilities, allowing developers to rapidly devise and test robot designs before the robot is built—a cost- and time-saving measure that results in more efficient and effective robots.
Actin’s flexibility across a range of robotic platforms has made the toolkit a go-to solution for multiple cutting-edge robot projects. For the military, Actin provides control capabilities for the U.S. Navy SUMO/FRIEND refueling robotic satellite, in development to extend the lifespan of expensive satellites by keeping them in orbit after their fuel has been exhausted. The software has been adapted to control the U.S. Army’s Battlefield Extraction Assist Robot, or BEAR, a powerful lifting robot designed to carry wounded soldiers out of harm’s way. Energid has also partnered with iRobot (Spinoff 2005) and other companies to develop a robotic bioagent detector based on iRobot’s PackBot platform and controlled by the Actin software.
In other areas, Energid’s NASA-derived software is at the heart of the company’s effort to revolutionize citrus fruit harvesting, using a robotic system with multiple cameras and disposable picking mechanisms to mass harvest fruit for juice processing. Through funding from the National Science Foundation, Energid is developing an Actin-based robotic grasping and manipulation framework that will allow robot manipulators or hands to grasp virtually any object without the need for reprogramming. And through affiliate company Robai, Energid provides its Actin toolkit to control low-cost commercial robot arms.
Energid now has 20 employees and opened an office in India to promote Actin’s capabilities in Asia. The foundation of the company’s success, English says, lies in the collaboration between government and private industry.
“Someone needs to take the risk to fund the research, and the government is in a good position to do that,” he says. “But then someone needs to take the initiative and carry it through to completion, and that is something private industry can do because the motivation is in place. Combining those two is the key.”
Actin™ is a trademark of Energid Technologies Corporation.
PackBot® is a registered trademark of iRobot Corporation.
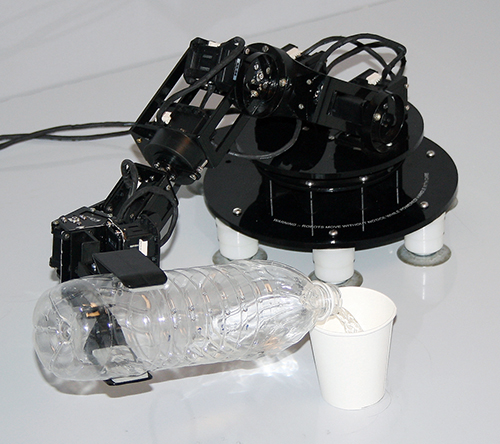
Energid Technologies Corporation’s NASA SBIR-derived Actin software provides control of robot manipulators like this Robai Cyton model.
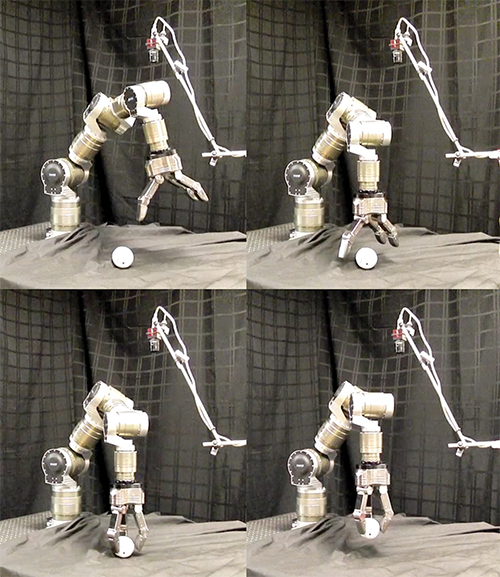
Here Energid’s NASA-derived software provides precise motion and grasping capabilities for a modular robot arm designed by German company SCHUNK GmbH & Co. KG. The Actin toolkit allows such robots to make fluid movements with optimized strength and accuracy.
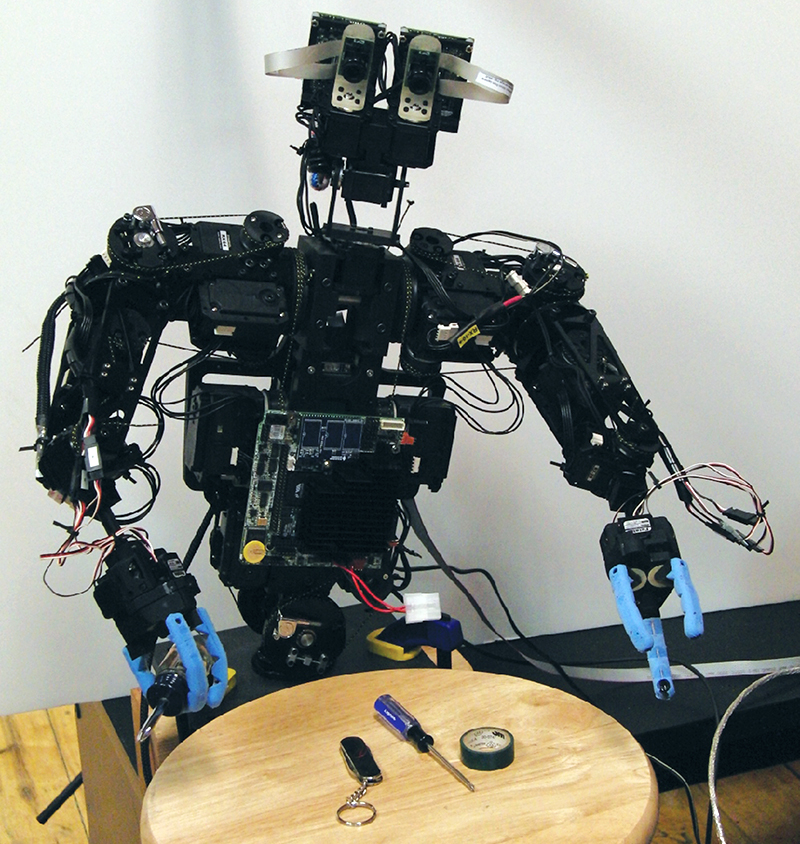
This robot, developed by Energid and its partners, utilizes Actin-based grasping software tools that allow the robot to grasp nearly any object without reprogramming.