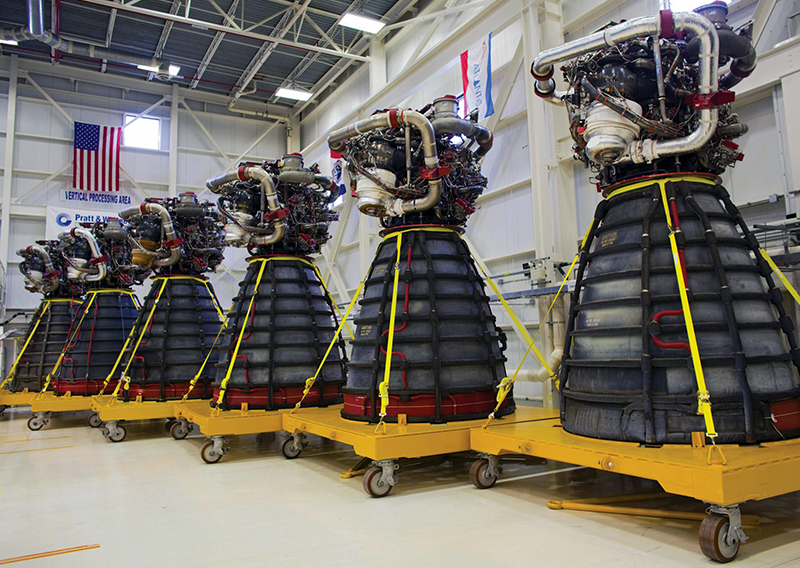
Meter Designs Reduce Operation Costs for Industry
NASA Technology
The space shuttle engines changed drastically from the drawing board to the launch pad. The engine—and each of its intricate parts—required extensive testing and modification before launch. Even in the final moments before use, NASA continuously monitored and measured their performance to ensure fail proof operation.
Years ago, during routine ground testing of a shuttle engine at Stennis Space Center, the measuring device for liquid oxygen (LOX) failed and resulted in a fire that burned the test stand beyond repair. Anthony Kelley, an engineer at Marshall Space Flight Center, says the event prompted NASA to consider alternative approaches for measuring LOX fuel. “We started thinking about safe ways to accurately measure LOX flow without inducing serious failure,” he says.
Although it might sound like a small detail, measuring the flow rate (the amount of fluid that flows in a certain time) is very important in liquid rocket engines, as it provides the basis for evaluating the engine’s performance and reliability.
Technology Transfer
At the time, there were no meters that met NASA’s stringent requirements for rocket engine LOX flow. The flow meter needed to perform with high accuracy in extreme temperatures and pressures and in various states—while ensuring no catastrophic failures.
To address the challenge, NASA’s Marshall Space Flight Center collaborated with a company called Quality Monitoring and Control (QMC) of Humble, Texas, through a 2001 Space Act Agreement. Together, the team brainstormed concepts and came up with a unique mathematical formula that was employed to make the new technology. Called a balanced flow meter (BFM), the invention was successfully applied in two of NASA’s rocket engine programs.
“The meters have operated accurately during highly dynamic flow conditions, which most metering technologies cannot do,” says Kelley. “The ability to meter and control propellants to very high levels of precision was proven.”
When NASA’s technology transfer office saw the potential of the BFM for applications outside of NASA, it funded a test program to evaluate its performance. “In most applications, the BFM produces typical flow measurement accuracies around 0.2 percent in very harsh environments and with no moving parts,” says Kelley.
To commercialize the technology, QMC founded A+ FlowTek (now APlus-QMC LLC), also of Humble, Texas. A+ FlowTek licensed the BFM from NASA, and by 2004, the company made its first commercial sale. In 2007, the technology was designated the Marshall Space Flight Center Invention of the Year. In 2010, it won the prestigious Federal Laboratory Consortium National Excellence in Technology Transfer award across all Federal agencies.
Benefits
BFMs are now used at chemical plants, refineries, power plants, pharmaceutical plants, and pulp and paper plants to determine the flow rate in piping, channel, and conduit systems. Aside from routine measurements, the technology also takes measurements for environmental standards reporting, facility certification, and for safety and process control systems. Sold around the world from the United States to China, Europe, and Australia, industry leaders such as Dresser-Rand, ABB, DuPont, and Rosemont are now using the NASA-derived BFM.
According to Paul Van Buskirk, the owner of APlus-QMC, approximately 5,000 different versions of the BFM have been manufactured since the company was founded—resulting in the creation of 100 new jobs and approximately $250,000 in annual sales.
APlus-QMC designs the devices using software that performs all the calculations necessary to manufacture custom meters for particular conditions, temperatures, pressures, and flows. Traditionally, flow meters have a single hole. The NASA-derived BFMs use a multi-hole design with a particular number and size of holes. They can be made of any material—stainless steel, titanium, or special alloys—and can be anywhere in size from half an inch to 10 feet in diameter.
Compared to the single hole design, BFMs provide a 10-fold increase in accuracy and a 15 to 1 reduction in audible noise. In some cases, says Van Buskirk, the company’s technology proves desirable because the Occupational Safety and Health Administration requires less noise in certain environments.
Another advantage of the technology is reduced energy use. “The payback compared to a single hole meter is a matter of weeks for energy efficiency,” says Van Buskirk.
BFMs also provide overall cost savings thanks to simpler installed-piping requirements, lower manufacturing costs, lower operating costs, and a longer lifespan. According to the company, the technology has saved an estimated $10 million for industrial facilities.
“It can save millionans per year compared to standard plates,” says Van Buskirk. “Accurate measurements are critical to plant operational efficiency, and the difference between an accurate and an inaccurate flow reading can mean a significant cost savings.”
Over the next 5 years, Van Buskirk aims to multiply the number of BFMs being manufactured. “We’re looking at contracts with companies like Shell and Exxon as exclusive flow-meter providers. We are also looking to open up the markets in two-phase flow for liquid and gas,” he says.
While many of the benefits of BFMs concern industrial productivity, there is an important application that has improved consumer safety. Through a Space Act Agreement between NASA and a commercial pool company, a BFM was used to test swimming pool safety systems. Tests showed the existing meter was not properly configured, and resulted in major changes in pool safety system test results on a National level.
“NASA technology transfer to benefit Americans was specified in our original charter and I believe it is one of the more important things NASA does. The efforts often create new capabilities, leading to benefits like more American jobs, greater energy efficiency, and improved industrial processes,” says Kelley. “In this case, the improved pool safety information will provide consumer benefits in safety for many years to come.”
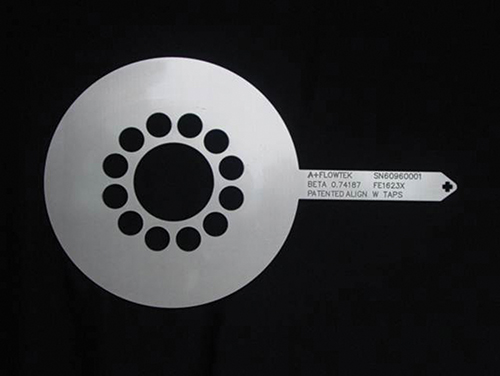
The NASA-derived flow meter uses a multi-hole design that consumes less energy than traditional meters.
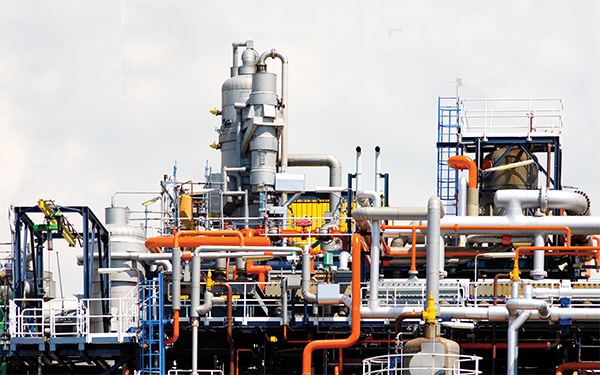
The technology has saved an estimated $10 million for industrial facilities.
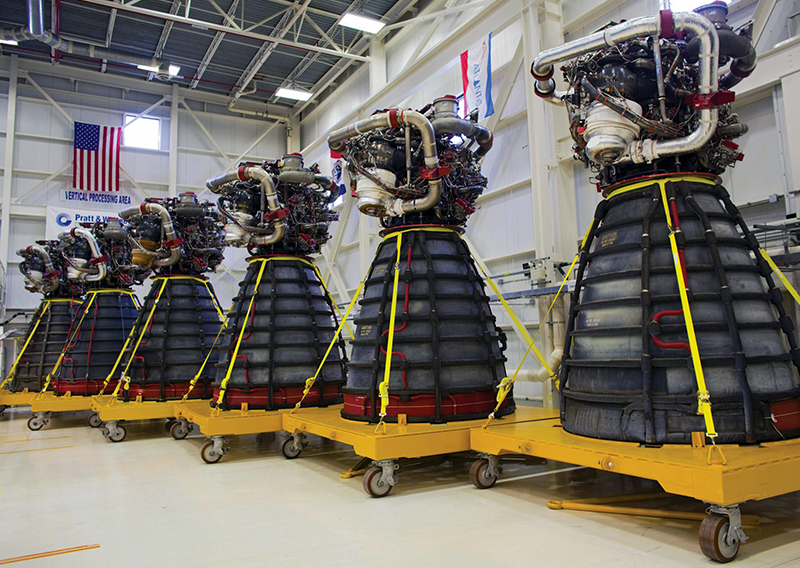
NASA worked with APlus-QMC LLC to develop a new meter for the shuttle engines (shown here being prepped for the next generation heavy lift rocket).