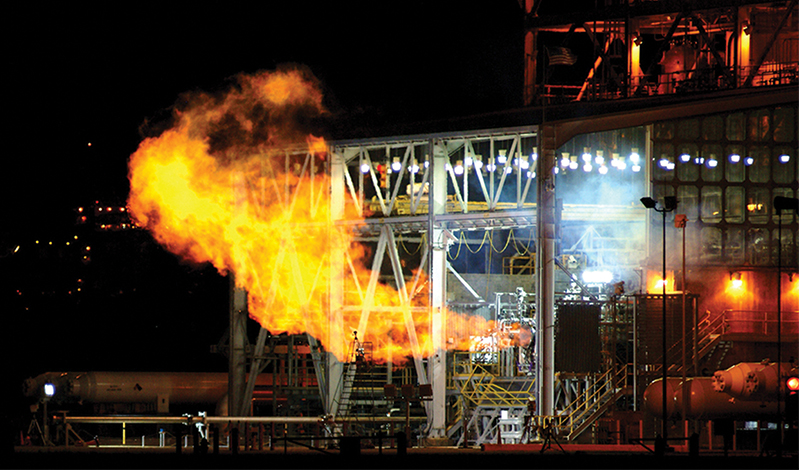
Smart Sensors Gather Information for Machine Diagnostics
NASA Technology
Surrounded by electronics and hovering over a work bench in the Data Acquisition and Control Systems (DACS) Laboratory, Scott Jensen startles when he hears the phone ring. He had been focused on what he was doing. After answering the phone—and a couple of questions about cooperative agreement opportunities—he returns to his work where he has his own questions to answer.
Jensen wonders how to engage technology development while reducing the costly test equipment failures at the E-Complex,to three propulsion test stands at NASA’s Stennis Space Center. Tests at the E-Complex monitor all of the parameters of rocket engine performance. When failures happen during a rocket engine test, the test is scrubbed and then repeated.
To help avert equipment failures and save thousands of dollars in costs, Jensen was interested in using smart sensors to monitor various components on the test stands. Smart sensors can process information on their own, are capable of two-way communication, and can, in some instances, even make their own decisions. At Stennis, such sensors could quickly report a problem and inform operators when something on a test stand requires maintenance. When issues are revealed during an engine test, a minor problem can be addressed before it becomes a major one.
Technology Transfer
Don Martin, president of St. Paul, Minnesota-based Lion Precision, a company that manufactures displacement sensors to measure small distances, learned about NASA’s interest in smart sensors while reading a NASA Tech Briefs publication. At the time, Martin was working with the MTConnect Institute on an industry standard to integrate devices from different manufacturers and communicate information through a standard interface. Martin knew NASA’s systems would be a good match with Lion Precision’s sensor technology as well as with his development work on MTConnect.
Martin contacted the Agency, and in 2010 Lion Precision partnered with Stennis through a Cooperative Agreement to develop a smart sensor and the associated communication protocols for use at the E-Complex. The partners’ goal was to monitor the valves responsible for the flow of liquid oxygen and liquid hydrogen during rocket engine tests. At the time, the sensors used on the valves were limited in the type of information they could obtain.
As Jensen explains, what is happening with these valves is critical. “The valves regulate highly combustible fluids under extreme pressure to supply the propellants for the test articles. Something could vibrate loose or the valve could get stuck and not close completely. Circumstances like that have caused problems, even shutdowns, during testing,” he says.
Because the duo also wanted to pursue technical advancements that were deployable within the explosive propulsion test environment, as part of the agreement, the measurements from Lion Precision’s sensors were transmitted using MTConnect.
“MTConnect allows you to get information from a lot of different machines and monitor different variables. The goal is to be able to take that data and look for trends so you can see if certain equipment was down, and what the causes were,” Martin says.
As a result of the partnership, Lion Precision produced sensors for the test stand valves that were able to obtain the precise rates at which the valves closed; whether the valves were sticking; and how near to open or closed the valve plugs were. The partnership was also the first implementation of the sensor protocols of MTConnect, an implementation that proved to be a significant contributor to the development of the larger MTConnect standard.
Benefits
The same smart sensor developed for NASA is now commercially available, and Lion Precision is incorporating the same diagnostic capabilities into its next generation of sensor products. “Even if you don’t use the MTConnect protocol, you can still get information from the sensors through the embedded software that provides diagnostic information,” says Martin. “The sensors can be used with or without MTConnect.”
In addition, the company has used its NASA experience to create a battery-powered wireless device that can transmit data on battery voltage, battery current, and temperature. So far, Lion Precision has built two prototypes of the wireless device for measuring the position of a machine tool that is used to make metal parts. The projected use is for manufacturing high-cost parts in the aerospace industry.
Martin says future applications for the sensor protocol for MTConnect also include the manufacturing or machining of metal parts. “It can track the wear on a cutting tool, how much the machine is running, or why it isn’t running,” says Martin. “It can also be used to sense vibration or temperature. The sensors plug on to a network and the data gets combined with other data from other devices. The real advantage is being able to combine data from all the different sources and figure out what the root causes of the problems are or when things are running smoothly.”
Martin compares MTConnect to the diagnostic device that a mechanic uses when working on an automobile. The device relays information from all the different sensors on a vehicle to see what is going on with each component. The same interconnectivity is the goal of MTConnect, but for devices on a manufacturing floor. Ultimately, the goal is to link technologies and move toward seamless manufacturing operation.
Thanks to the partnership, Jensen will be able to obtain some answers to his own questions about seamless operation. “You can show a failure with the test stand valves in a preventive manner,” he says. “And the same MTConnect protocol can be used for all types of equipment at NASA. There are a lot of different areas that could benefit.”
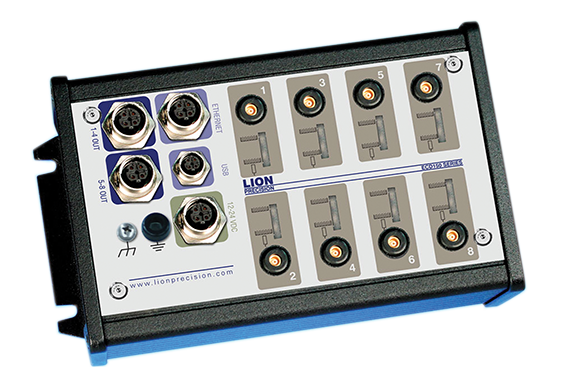
Lion Precision developed a smart sensor, which is now commercially available, through its work with Stennis.
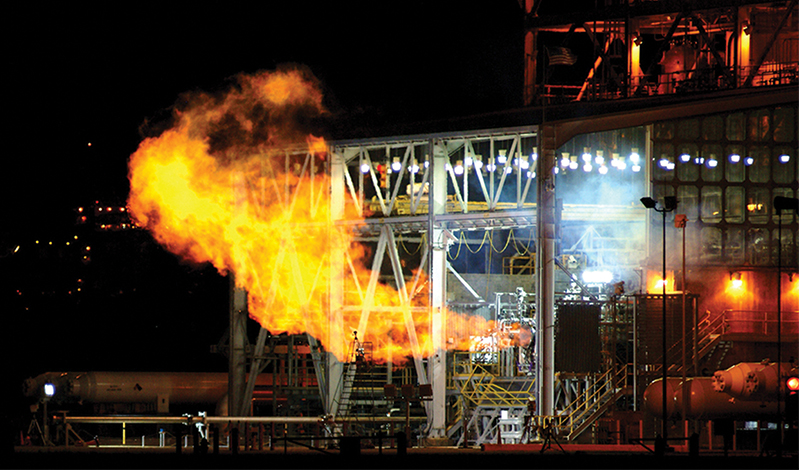
A plume of fire emerges from a rocket engine test stand at Stennis Space Center’s E-Complex, where Stennis worked with a private company to develop sensors and communication protocols to monitor valves during testing.