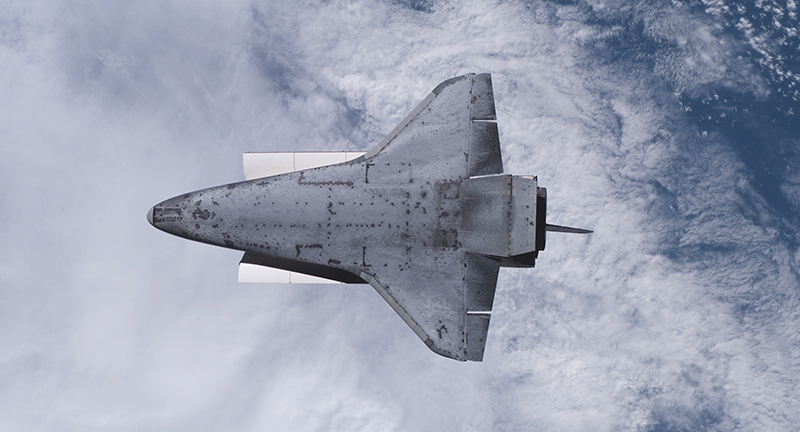
Space-Ready Durometers Measure Hardness on Earth
NASA Technology
There are no mechanic shops in space.
Following the Space Shuttle Columbia accident in February 2003, NASA implemented additional safety inspections to be conducted in space to ensure returning Shuttles weren’t in danger of fracturing or losing integrity upon reentry into Earth’s atmosphere.
Every time a Shuttle landed at either Edwards Air Force Base or Kennedy Space Center, engineers and mechanics painstakingly examined every square inch for damage, says Mark Dub, an extravehicular tool engineer at Johnson Space Center. “You’d see these little dings, dents, chips, cracks, divots on the underside of the Shuttle,” he says, adding that prior to the Columbia accident, it was unclear whether the damage was inflicted in space or during reentry.
Once spaceflight resumed two years later, NASA began using the orbiter boom sensor system, an extension of a robotic arm carried by the Shuttle, to “carry a package of cameras and lasers that you would use underneath the Shuttle to inspect it and check for damage,” Dub says.
Shuttles would also perform a 360-degree pitch maneuver, in which the Shuttle would flip nose-over-engines onto its back while approaching the International Space Station (ISS). Astronauts on the ISS would examine the tiles on the Shuttle’s underbelly as it approached, taking photos to be sent back to Mission Control for analysis.
If missing or damaged tiles were found, one of several in-space repair options called for astronauts on a spacewalk to don special backpacks filled with a two-part “goo” called a cure-in-place ablator (CIPA) that both filled cracks and could be used to replace entire tiles if needed, Dub says. The two parts of the CIPA, which he compares to caulk, would mix as dispensed, allowing a catalyst to enable the goo to harden within about 24 hours.
Carrying replacement tiles was out of the question, as most of the Shuttle’s estimated 22,000 tiles were precisely shaped according to placement on the Shuttle, Dub says. Tiles closer to the nose and wing edge were thicker to better withstand the greater heat of reentry in those regions, for example.
But in order to ensure the repair work was strong enough to withstand the flight back through Earth’s atmosphere, NASA needed a little help.
Technology Transfer
Durometers are gauges used to determine the hardness of a nonmetallic substance—anything from sporting equipment and tires to shoe soles and lobster shells, explains JC Blum, vice president of operations at Buffalo Grove, Illinois-based Rex Gauge Inc. One of three durometer manufacturers in the country, Blum says his company was initially approached by Lockheed Martin on NASA’s behalf before working directly with the Agency.
Rex Gauge has been making gauges and specializing in durometers since 1942 and, in general, the design hasn’t changed much in that time, Blum says. The bottom of the gauge is a spring-loaded indenter, which is pushed into whichever substance needs to be tested for hardness and measures the amount of penetration into the material under a given spring force. The gauge has a dial to display the hardness of the substance on a scale of zero to 100 durometers, he says.
Rex Gauge had an advantage over the other durometer manufacturers in that its parent company, Schultes Precision Manufacturing, is a machine shop and could quickly turn around any custom work needed by clients, Blum says.
Most of the standard durometer’s functionality aligned with NASA’s needs in space, but the Agency needed something that could be easily seen through the visors astronauts wear to protect from the unfiltered light of the sun.
“If you look at our standard product line, the dials are much smaller on top,” Blum says. To meet NASA’s requirements, Rex Gauge adopted a larger dial, roughly the size of a pocket watch face at about 2 ½ inches in diameter, and instead of relying solely on numbers, added a red and green background. That way, astronauts would be able to tell at a glance whether the goo was hard enough or needed more curing time.
The durometer’s barrel was given a matte finish for easier gripping by pressurized gloves, and the top was modified to have more of a mushroom shape to make it easier to grab. Additionally, the barrel was given a tether point and bayonet probe, common attributes on tools used for extravehicular activities, to allow for ease of access and securing into an astronaut’s tool belt or toolbox.
“Putting the bayonet probe on the durometer made it a lot easier to carry it out there, to store it when you’re not using it and to use it when you are,” Dub explains. “The tether point on top of the handle was a spot where you could attach a hook to it, and that hook would keep the durometer from floating away.”
Benefits
The durometer modified by Rex Gauge for NASA was crucial when making CIPA applications and tile repairs, Dub says. Readings in the red area indicated the CIPA had not yet cured sufficiently to protect the Shuttle from the searing heat of reentry. A green reading meant the tile was ready to withstand the return trip.
Blum says NASA was pleased with the durometer, noting that it “was and remains an integral part of the thermal protection tile repair system.”
Back on Earth, Blum says, the company made a special Web site to highlight its work with NASA.
“We enjoyed having the opportunity to work with NASA, for sure,” he says. “It was very cool to have a gauge go up into space.”
The durometer has certainly became something of a conversation piece, he adds.
“All our gauges have model numbers. This one is the SG-5000, and everyone’s like, ‘What’s SG?’ That’s for space gauge,” he says with a chuckle.
The company has since incorporated the larger dials into its new line of digital durometers for easier readability. The first year the new, larger display was the standard option for the Model DD-4 durometer, sales increased 35 percent, Blum notes.
Following the work on NASA’s durometer, the company established a partnership with the Space Foundation, earning a Space Certification which allows Rex Gauge to use a “Space-Certified” logo on marketing materials as well as the company’s Web site. The gauge made for NASA is also featured as a highlight on another section of the company’s Web site promoting custom-made gauges.
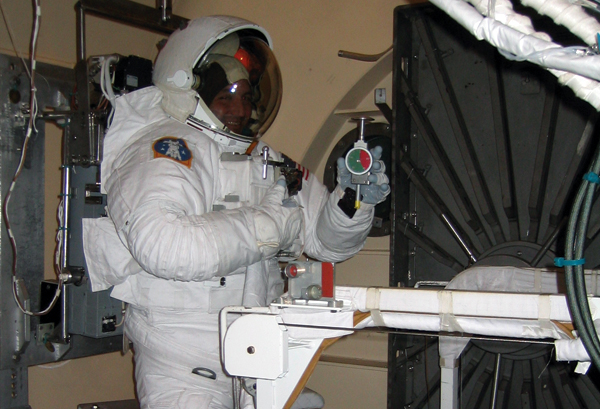
An astronaut in training holds the modified durometer, made by Rex Gauge, that was used to ensure any repaired or replaced tiles on the underside of a space Shuttle were hard enough to withstand the heat of reentry from orbit.
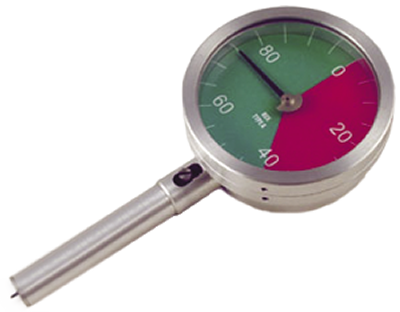
Rex Gauge modified a durometer to meet NASA’s needs for repairing and replacing the thermal protection tiles on the underside of the Space Shuttle, including enlarging the device’s dial. When the resized dial was applied to the company’s digital model, sales increased 35 percent.
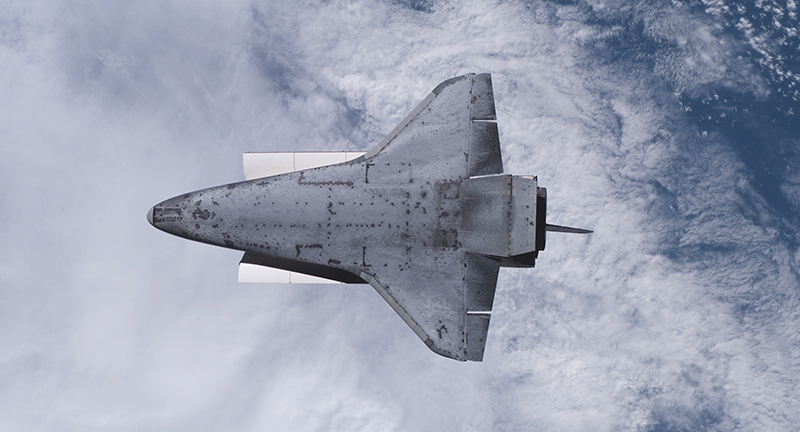
A view of the Space Shuttle Endeavour as the STS-118 crew puts the spacecraft though a rendezvous pitch maneuver, allowing the crewmembers on the nearby ISS to document the vehicle’s thermal protection system condition.