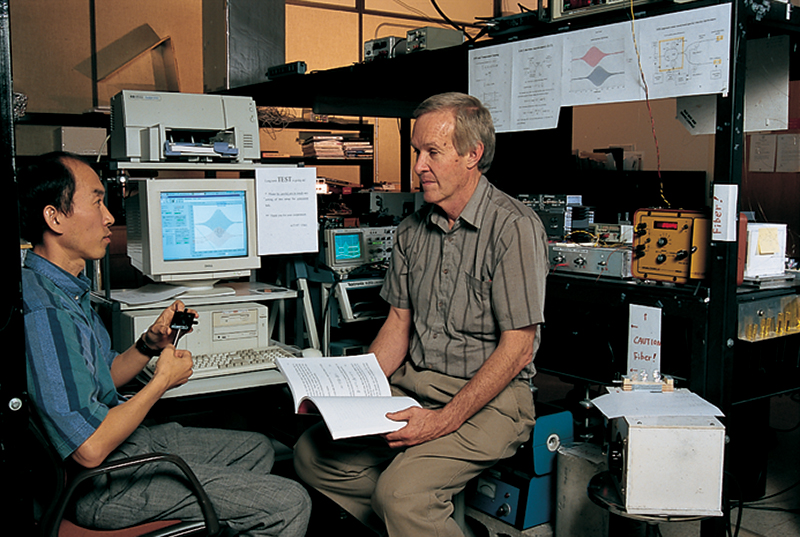
Pressure Measurement Sensor
At one time or another, everybody is forced to work under high pressure. But that stress is no match for the cruel and harsh conditions inside internal combustion engines.
FFPI Industries, Inc. of Bryan, Texas is the manufacturer of fiber-optic sensors that furnish accurate pressure measurements in internal combustion chambers. Such an assessment can help reduce pollution emitted by these engines.
A chief component in the sensor owes its seven year-long development to Lewis Research Center funding to embed optical fibers and sensors in metal parts. NASA support to Texas A&M University played a critical role in developing this fiber optic technology and led to the formation of FFPI Industries and the production of fiber sensor products.
FFPI Industries draws its name from use of a fiber optic Fabry-Perot interferometer. This sensing element is the basis for the company's in-cylinder pressure transducer. Engine pressure sensors and signal conditioning units were introduced in 1995 as the first products from FFPI Industries.
Robert Atkins, President and CEO of FFPI Industries predicts that a vast market for the firm's products is likely to emerge. "Sensors are the key to industrial monitoring and control systems designed to lower equipment maintenance cost, improve fuel economy, reduce atmospheric pollution, and provide a safer workplace," Atkins says.
FFPI sensors are enclosed in a housing similar in dimension to a spark plug. A metal jacket protects the device from the high temperatures and pressures that it is to measure. The sensor can be mounted in a threaded port in the engine's cylinder head or in a standard pressure monitoring port external to the engine.
Fiber optic technology allows the sensor to survive at much higher temperatures than conventional pressure sensors. Additionally, the FFPI sensor is immune to electromagnetic interference, offering another advantage over conventional sensors for industrial applications. Once in place, the sensor relays information to a control system that can automatically adjust the engine for smoother operation.
Clean Air Act provisions and energy savings are sparking keen industrial interest in the FFPI sensor. Legislation has called for operators of large internal combustion engines to seek a reduction in harmful emissions to 10-50 percent of present levels. Retrofitting the largest class of reciprocating engines with precombustion chambers and/or catalytic converters would entail significant cost. Utilizing the fiber optic engine pressure sensor as one economical solution to emission reduction in large engines is a reasonable idea.
FFPI sensors have measured pressure reliably for thousands of hours in large Clark and Worthington engines in facilities operated by Tenneco Energy Corporation and Transcontinental Gas Pipeline Company. Some 40,000 hours of in-cylinder operation by the sensors, without mechanical failure, have been attained in a pipeline engine. Pressures up to 1000 psi under maximum load at 300 rpm were experienced by the sensors, along with soaring temperatures upwards of 300 degrees centigrade. The sensors have also operated in General Electric and AMD Diesel Locomotive engines under even more demanding conditions: temperatures over 800 degrees Celsius and pressures over 2500 psi.
The simple, rugged design of the sensor offers the potential for mass production at low cost. The company envisions many other sensing applications for the basic technology, including:
- vibration sensors for turbine engines and pumps;
- temperature sensors for semiconductor integrated chip processing;
- biomedical pressure and temperature sensors;
- embedded strain and acoustic sensors for "smart structures" such as aircraft wings and bridges; and
- sensors for monitoring chemical constituents in gases and liquids.
Widespread application of the new technology is foreseen, says Atkins of FFPI Industries, from natural gas transmission, oil refining and electric power generation to rail transport and the petrochemical paper product industry.
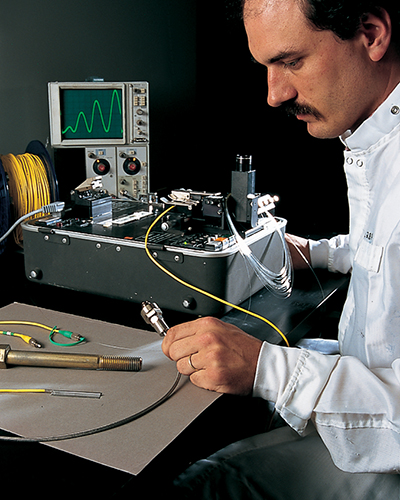
When mounted in an engine, FFPI Industries' fiber optic sensors can relay information to a control system that automatically adjusts the engine for smoother operation.
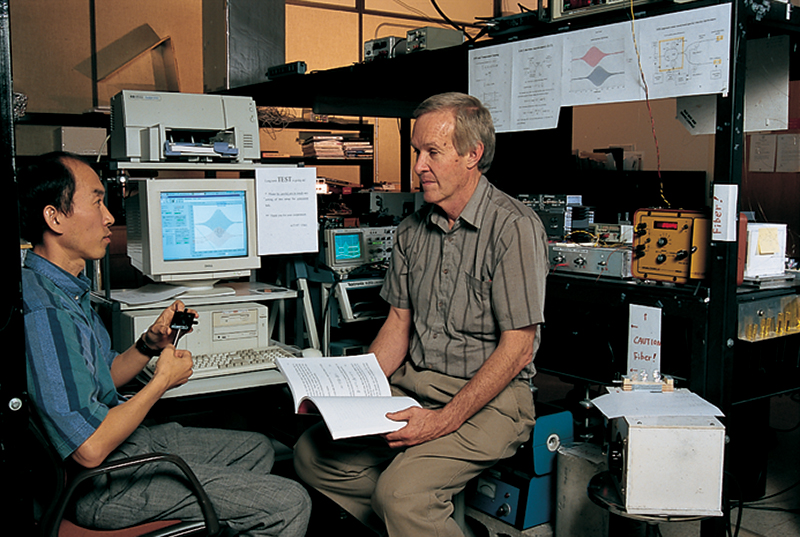
Graduate student Han-Sun Choi (left) and Dr. Henry Taylor of Texas A&M University test fiber optic temperature sensors. FFPI Industries tests each of its sensors on an engine with a computer calibration system before shipping.