The Imagery of Sound
Engineers and designers can enjoy the benefit of software that measures the acoustical performance of products. Automated Analysis Corporation (AAC) of Ann Arbor, Michigan, and NASA have made this innovation possible.
With the help of Small Business Innovation Research (SBIR) funds from NASA's Langley Research Center, AAC developed computer technology that creates images of the acoustical characteristics of systems and components in many industries, such as the aircraft, automotive, and audio systems industries. This type of software is useful in Langley's efforts to optimize the acoustical performance of aircraft by predicting design effects, such as those within aircraft sidewalls and seating. AAC has made this technology available to its customers by offering COMET®--a suite of acoustic analysis software for advanced noise prediction. COMET is used during the design and analysis cycle of product development and offers engineers and designers the benefit of cost reduction and sound quality improvement by predicting the product's sound performance even before the first prototype is built.
COMET analyzes the origin, radiation, and scattering of noise, and supplies information on how to achieve noise reduction and improve sound characteristics. This software is a valuable tool in reducing design time and expense, while simultaneously optimizing a final product's acoustical performance.
COMET's Structural Acoustic Foam Engineering (SAFE) module extends the sound field analysis capability of foam and other absorptive materials. SAFE shows how noise travels while airborne, how it travels within a structure, and how these media interact to affect other aspects of the transmission of noise. Although foams themselves are not useful as sound barriers, they are useful for sound absorption, and for this reason, SAFE can help users optimize those absorptive qualities.
The interactions among various domains are generalized so that all types of interface conditions can be accurately modeled. This is especially important in foam-like materials, because the type of interaction among domains can significantly affect the acoustical performance of the product.
"[SAFE] enables product engineers and designers to predict the noise performance of a wide variety of materials, such as glass fiber, mineral wool, and open or partially open cell foams," according to Kim Novak, AAC company representative. These materials are found in a variety of products such as headliners, seats, carpets, trim lining, panel damping, aircraft skin insulation, building wall insulation, machinery, and enclosure liners, and its uses continue to grow. SAFE provides a powerful tool that can be used for the design of optimal modern noise control treatments, thereby solving many acoustic problems in foam materials.
AAC is a computer-aided engineering company, founded in 1983, and provides consulting services to the aerospace and automotive industries. Other NASA-inspired products are being commercialized by AAC as well, promising great strides in effective sound design.
Comet® is a registered trademark of Automated Analysis Corporation.
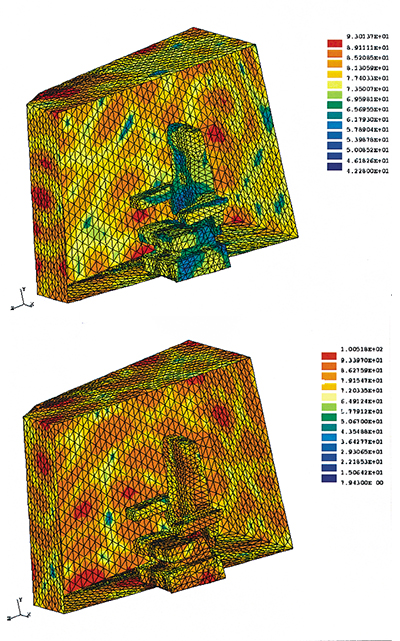
Both seats were modeled by Automated Analysis Corporation's SAFE. The top incorporates absorptive material and the bottom was modeled as rigid.