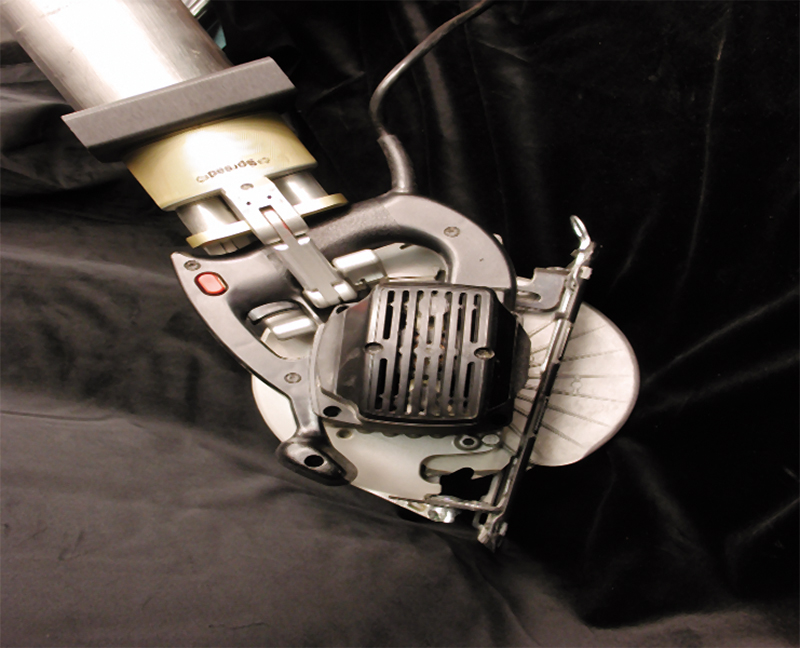
Lending a Helping Hand
Barrett Technology,® Inc., of Cambridge, Massachusetts, received the 2003 Robotic Industries Association's Joseph Engelberger Award for Technology Leadership based on successful commercialization of its novel robotic manipulators. Designed for applications requiring superior adaptability, programmability, and dexterity, Barrett's devices provide state-of-the-art functionality and capability, as well as product integration with existing technology. The cutting-edge robotic manipulators originated through collaboration with NASA, the National Science Foundation, and the U.S. Air Force.
In the 1990s, NASA's Johnson Space Center awarded Barrett four Small Business Innovation Research (SBIR) contracts, leading the company to develop the first commercially available cable-driven robots. Today, the company supports two robotic manipulator product lines: the Whole-Arm Manipulation System (WAM™) and its BH8-Series™ hands, both of which received funding through SBIR contracts. During a Phase II SBIR contract with Johnson, Barrett designed the EVA-Retriever WAM arm for NASA's use as an autonomous robot to recover crew or tools outside of the Space Station.
The WAM arm outperforms today's conventional robots through its extraordinary dexterity, transparent dynamics, high bandwidth, zero backlash, and near-zero friction. The device can reach around objects and clasp them, much like a person holding a large item between his or her forearm and upper arm without compromising the use of hands for small items. Conventional robotic arms are strictly limited to the use of hand end-effectors and therefore small payloads. The WAM arm is also distinguished from other arms with its use of gear-free cable drives to manipulate its joints.
Listed in the Millennium Edition of The Guinness Book of World Records (2000) as the world's most advanced robotic arm, the WAM arm closely resembles its human counterpart. The arm consists of a shoulder that operates on a gearless differential mechanism, an upper arm, a gear-free elbow, forearm, and wrist. This arrangement of joints coincides with the human shoulder and elbow, but with much greater range of motion. Like a person's arm, but unlike any industrial robotic arm, the WAM arm is backdriveable, meaning that any contact force along the arm or its hand is immediately felt at the motors, supporting graceful control of interactions with walls, objects, and even people. With a human-scale 3-foot reach, it is so quick that it can grab a major-league fastball, yet so sensitive that it responds to the gentlest touch.
Like the WAM arm, the BH8-262 BarrettHand™ offers many benefits in dexterity. A multi-fingered programmable grasper, the BarrettHand can pick up objects of different sizes, shapes, and orientations. According to the company, integrating this device with any robotic arm is fast and simple, and immediately multiplies the value of any arm requiring flexible automation. The BarrettHand is compact and completely self-contained, weighing only 1.18 kilograms (kg). The newest product in the series is the soon-to-be-released BH8-601 Wraptor,™ a large-capacity 7-kg, three-fingered system featuring enhanced dexterity, a vision-camera mount, and user-accessible sensor support on all finger and palm surfaces. In addition to wrapping its fingers around an object, the device can perform internal grasps by reaching its fingers inside of an object and then spreading them open.
The WAM arm, BarrettHand, and Wraptor have commercial applications ranging from human-collaborative medical surgery to emergency response to chemical, biological, and nuclear materials. Barrett is also targeting markets such as physical therapy, rehabilitation, assisted-living aids, metrology, short-run manufacturing, and entertainment.
WAM,™ BH8-Series,™ BarrettHand,™ Wraptor,™ and the Barrett Technology® logomark are trademarks of Barrett Technology, Inc.
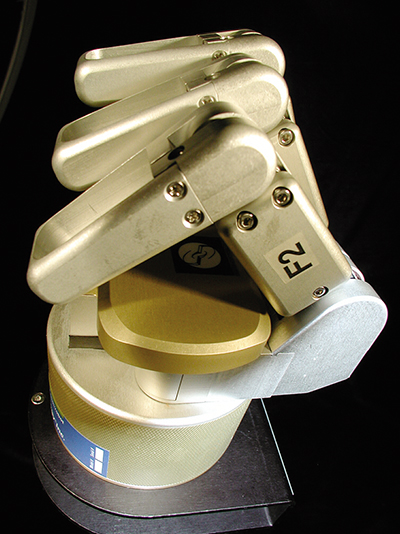
The BarrettHand,™ a multi-fingered programmable grasper, can pick up objects of various shapes and sizes.
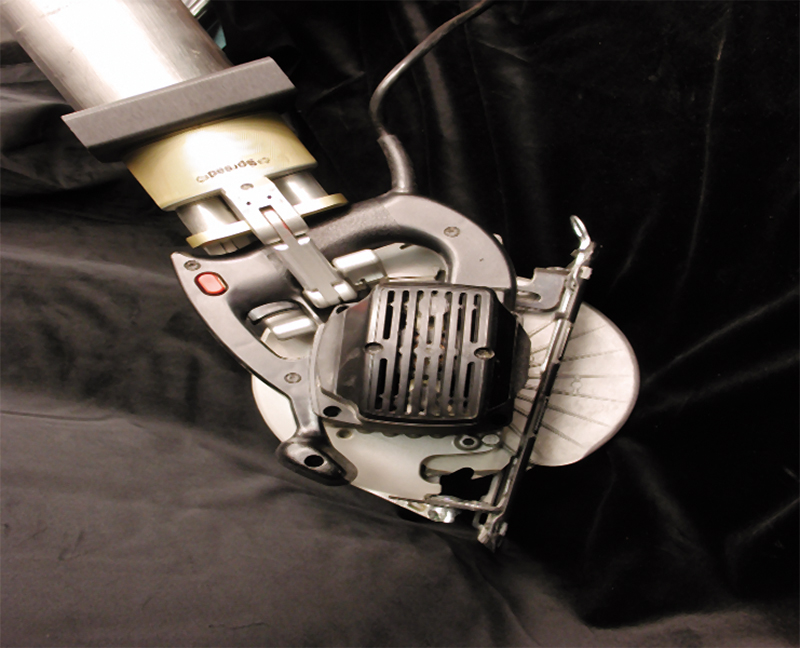
The WAM™ arm consists of a shoulder that operates on a gearless differential mechanism, an upper arm, a gear-free elbow, forearm, and wrist. This arrangement of joints coincides with the human shoulder and elbow, but with much greater range of motion.