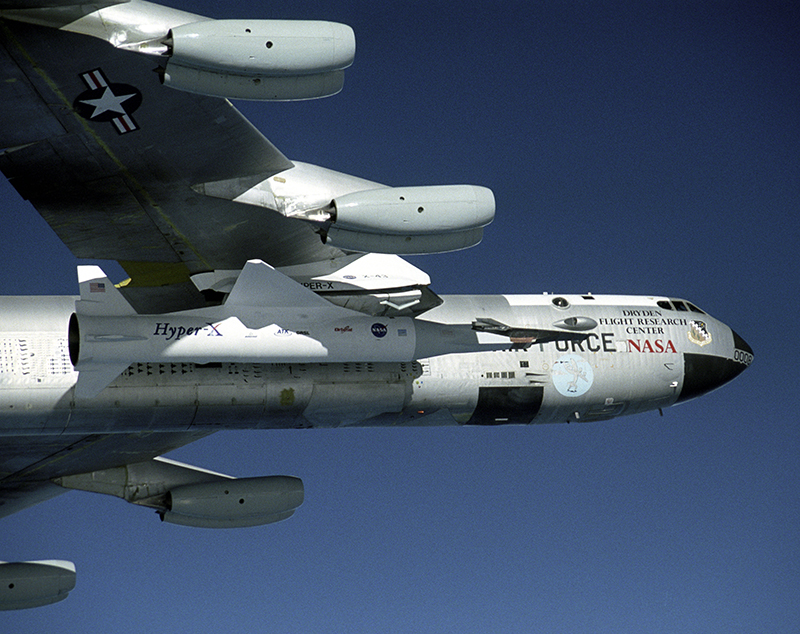
Hypersonic Composites Resist Extreme Heat and Stress
Originating Technology/NASA Contribution
On October 14, 1947, Captain Charles “Chuck” Yeager made history when he became the first pilot in an officially documented flight to ever break the sound barrier. Flying a Bell XS-1 test jet over the Mohave Desert, Yeager hit approximately 700 miles per hour, when a loud boom thundered across the barren landscape as he crossed from subsonic to supersonic speeds. The sonic boom, akin to the wake of the plane’s shockwaves in the air, occurred at Mach 1—the speed of sound (named after Ernst Mach, an Austrian physicist whose work focused on the Doppler effect and acoustics).
This eventually led to the famous 3-hour trans-Atlantic flights of the Concorde, traveling at Mach 2, and the development of fighter jets, which began routinely crossing the sound barrier—the era of supersonic flight. At NASA, however, aerospace engineers wanted to go faster—hypersonic or Mach 5; five times the speed of sound. They continued to push the limits of speed, setting a world record in October 1967, which held for 35 years at Mach 6.7, in the NASA-designed X-15 aircraft.
Never content to rest on its laurels, the Space Agency wanted to go even faster. NASA began the X-43A project, the purpose of which was to go Mach 10. The “X” in the name, as in X-1 and X-15, signifies that these are experimental aircraft, not intended for mass production, but built solely for flight research, and the 43 indicates that it was the 43rd such aircraft.
The major experimental feature of this particular aircraft was a scramjet engine, which kicks in at about Mach 6. In a normal jet engine, blades compress the air, but in the scramjet, the combustion of hydrogen fuel in a stream of air is compressed by the high speed of the aircraft itself. To achieve Mach 10, the X-43A was first carried up into the air attached to a B-52 and then “jumpstarted” with a Pegasus rocket.
It was a multiyear experiment and involved building three test vehicles. The first two were meant to reach speeds of up to Mach 7, and the third was reaching for double digits: Mach 10. NASA hoped that these three unmanned crafts would allow aerospace engineers to further advance understanding of hypersonic flight and that the lessons learned could be applied to increase payload capacity for future vehicles, including hypersonic aircraft and reusable space launchers.
Tullahoma, Tennessee-based ATK-GASL built the X-43A and its engine, while the Huntington Beach, California-based Boeing Company’s Phantom Works designed the thermal protection and onboard system. The booster, a modified Pegasus rocket, was built by Orbital Sciences Corporation at the company’s facility in Chandler, Arizona. The program was jointly managed by NASA’s Dryden Flight Research Center and Langley Research Center.
The first X-43A dropped from the B-52 carrier aircraft on June 2, 2001 and spun out of control when the booster rocket failed to operate properly. It was destroyed and allowed to fall into the ocean. The second test vehicle launch was a success, making the X-43A the fastest free-flying, air-breathing aircraft in the world. On November 16, 2004, NASA launched the third X-43A scramjet aircraft, which reached record-breaking speeds near Mach 9.8 at an altitude of around 110,000 feet. The aircraft still holds the Guinness World Record.
Partnership
Through research contracts with NASA, Materials and Electrochemical Research Corporation (MER), of Tucson, Arizona, contributed a number of technologies to these record-breaking flights. Over the course of 6 years, MER completed Phase II Small Business Innovation Research (SBIR) contracts with Goddard Space Flight Center, Langley Research Center, the Jet Propulsion Laboratory, Johnson Space Center, and Marshall Space Flight Center. By partnering with NASA through these contracts, MER developed a coating that successfully passed testing at simulated Mach 10 conditions, and provided several carbon-carbon (C-C) composite components for the flights.
MER created all of the leading edges for the X-43A test vehicles at Dryden. Considered the most critical parts of this experimental craft, the leading edges had several specific requirements. As the vehicle’s speed increased, so did heat and thermal load, approaching 4,000 °F, well above the temperatures the shuttle is exposed to during reentry. In addition to being very heat resistant, the coating had to be very lightweight and thin, as the aircraft was designed to very precise specifications and could not afford to have a bulky coating.
In total, 11 C-C leading edges were created for the nose, the chines (the areas where the body meets the wing), the verticals, and 2 horizontals. These parts were made with P-30X graphite fibers, using a liquid matrix process. A very high process temperature was utilized to render the high-thermal conductivity. The parts were first processed in the form of a C-C billet, and then machined to NASA specifications. Oxidation protection was achieved by a dual chemical vapor reaction and chemical vapor deposition process.
Product Outcome
To take advantage of commercializing these specialized composites, MER patented its C-C composite process and then formed a spinoff company, Frontier Materials Corporation (FMC), in Tucson, Arizona. FMC is using the patent in conjunction with low-cost PAN (polyacrylonitrile)-based fibers to introduce these materials to the commercial markets.
The C-C composites are very lightweight, yet still have great strength and stiffness, even at very high temperatures. They can be produced with either low- or high-thermal conductivity, and when graphitized, they have superior electrical conductivity. Even with all of these characteristics, the carbon composites are still relatively inexpensive.
The composites have been used in industrial heating applications, the automotive and aerospace industries, as well as in glass manufacturing and on semiconductors. C-C composites have been used in industrial heating fixtures in the form of structural flat panels, structural members for panel support, and for nuts and bolts. In the automotive industry, the composites have been useful for engine components, brakes, cylinder liners, and panels. Aerospace applications have included missile bodies, leading edges, and structured components. Applications also include transfer components for glass manufacturing and structural members for carrier support in semiconductor processing.

The X-43A flights were the first actual flight tests of an aircraft powered by a scramjet engine capable of operating at hypersonic speeds (above Mach 5, or five times the speed of sound).
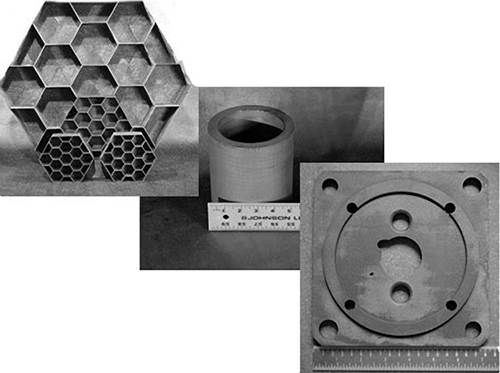
MER’s carbon-carbon composites are very lightweight, yet still have great strength and stiffness, even at very high temperatures.
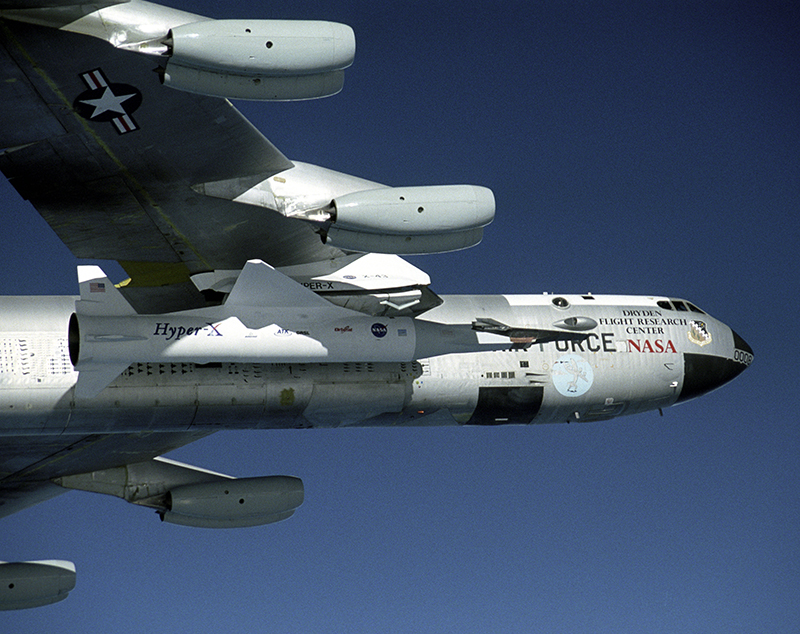
The first X-43A hypersonic research aircraft and its modified Pegasus booster rocket were carried aloft by NASA’s B-52 carrier aircraft from Dryden Flight Research Center on June 2, 2001, for the first of three high-speed free flight attempts.