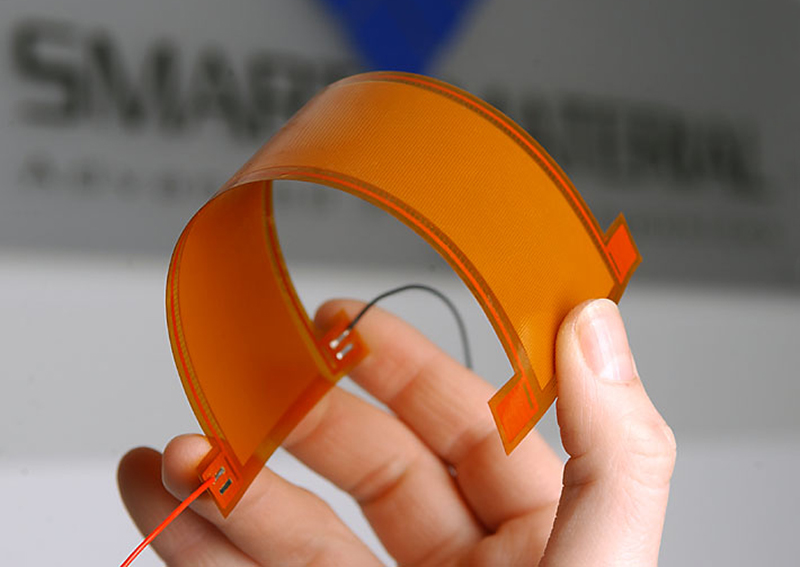
‘NASA Invention of the Year’ Controls Noise and Vibration
Originating Technology/NASA Contribution
Developed at NASA’s Langley Research Center, the Macro-Fiber Composite (MFC) is an innovative, low-cost piezoelectric device designed for controlling vibration, noise, and deflections in composite structural beams and panels. It was created for use on helicopter blades and airplane wings as well as for the shaping of aerospace structures at NASA.
The MFC is an actuator in the form of a thin patch, almost like a 3- by 2-inch bandage comprised of piezoelectric fibers, an epoxy matrix, and polyimide electrodes, and is also called a piezocomposite. If one applies a voltage to the MFC it will stretch, and if attached to a structure it will cause the surface to bend. The major advantages of a piezofiber composite actuator are higher performance, flexibility, and durability, compared to a traditional piezoceramic actuator.
MFCs consist of rectangular piezoceramic rods sandwiched between layers of adhesive film containing tiny electrodes that transfer a voltage directly to and from ribbon-shaped rods that are no thicker than a few tenths of a millimeter. These miniscule actuators are roughly equivalent to human muscles—flexing, stretching, and returning to their original position when electricity is applied.
Because any external mechanical deformation of an MFC package produces a charge on the electrodes proportional to the deflection, its compression or stretching also enables the MFC to be used as a self-powered sensor. Defects within structures can therefore be detected, or small amounts of energy can be collected and stored for later use.
The MFC’s combination of small size, durability, flexibility, and versatility allows it to be integrated—along with highly efficient electronic control systems—into a wide range of products. Potential applications include sonar; range-measuring and fish-finding equipment; directional-force and fingerprint sensors; flow meters; and vibration/noise control in aircraft and automobiles. Since its original development in 1999, the MFC has been used in government and industrial applications ranging from vibration reduction to structural health monitoring.
NASA has used MFC piezocomposites for alleviating tail buffeting in aircraft, controlling unsteady aerodynamics and noise on helicopter rotor blades, and actively reducing vibrations in large deployable spacecraft structures. The MFC has been used as a sensor for impedance-based health monitoring of launch tower structures at NASA’s Kennedy Space Center, for strain feedback sensing and control in industrial arc welding equipment, in an STS-123 experiment, in solar sail technology, and in ultra-lightweight inflatable structures.
The MFC has been internationally recognized for its innovative design, receiving two prestigious “R&D 100” awards in 2000, including the “R&D Editor’s Choice” award as one of the 100 most significant technical products of the year. The MFC was also the recipient of the International Forum’s prestigious “iF Gold” award, in Germany, for design excellence in 2004. In March 2007, the MFC was awarded the title of “NASA Invention of the Year.”
Partnership
Smart Material Corporation, of Sarasota, Florida, specializes in the development of piezocomposite components. The company licensed the MFC technology from Langley in 2002, and then added it to their line of commercially produced actuators.
It now combines the Langley MFC’s piezoelectric properties with the robustness and conformability of plastics to radically extend the spectrum of commercial applications.
A NASA partnership gives a small company access to research and technologies that allow it to compete with larger corporations. According to Thomas Daue, with Smart Material Corporation, “For a small business, it is almost not possible anymore to spend the money for basic research in high tech products. Licensing technology from the leading research facilities in this country is a very cost effective way to become a player in a new technology field. Many developments ready for licensing at government-owned facilities have already reached the proof of concept status, which would often cost a small business or start-up millions of dollars.”
Smart Material Corporation is now marketing MFCs internationally, with the majority of applications in the United States directed at Federal government research projects or defense-related government contracts. For example, Smart Material Corporation currently sells the materials to Langley, NASA’s Jet Propulsion Laboratory, and Marshall Space Flight Center, where they are used as strain gauge sensors, as well as to the U.S. Air Force and the U.S. Army.
Product Outcome
To date, Smart Material Corporation has sold MFCs to over 120 customers, including such industry giants as Volkswagen, Toyota, Honda, BMW, General Electric, and the tennis company, HEAD. The company also estimates that its customers have filed at least 100 patents for their unique uses of the technology.
Smart Material Corporation’s main manufacturing facilities are located in Dresden, Germany, in the vicinity of the Fraunhofer Institute for Ceramic Technologies and Sintered Materials, one of the world’s leading research institutes in the field of advanced ceramics. Dresden is also the center of the German semiconductor industry, and so provides crucial interdisciplinary resources for further MFC refinement. In addition to its Sarasota facility, the company also has sales offices in Dresden and in Tokyo, Japan.
The company’s product portfolio has grown to include piezoceramic fibers and fiber composites, piezoceramic actuators and sensors, and test equipment for these products. It also offers a compact, lightweight power system for MFC testing and validation.
Smart Material Corporation believes that solid-state actuator systems, including piezoceramics, will have healthy commercial growth in the coming years, with increasing penetration in industrial, medical, automotive, defense, and consumer markets. Consumer applications already on the market include piezoelectric systems as part of audio speakers, phonograph cartridges and microphones, and recreational products requiring vibration control, such as skis, snowboards, baseball bats, hockey sticks, and tennis racquets.
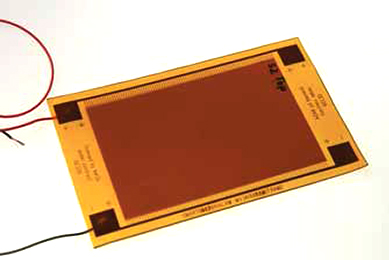
The Macro-Fiber Composite’s flat profile and use as a sensor and an actuator allows for use in critical or tight areas where other technologies with larger volumetric profiles cannot be used.
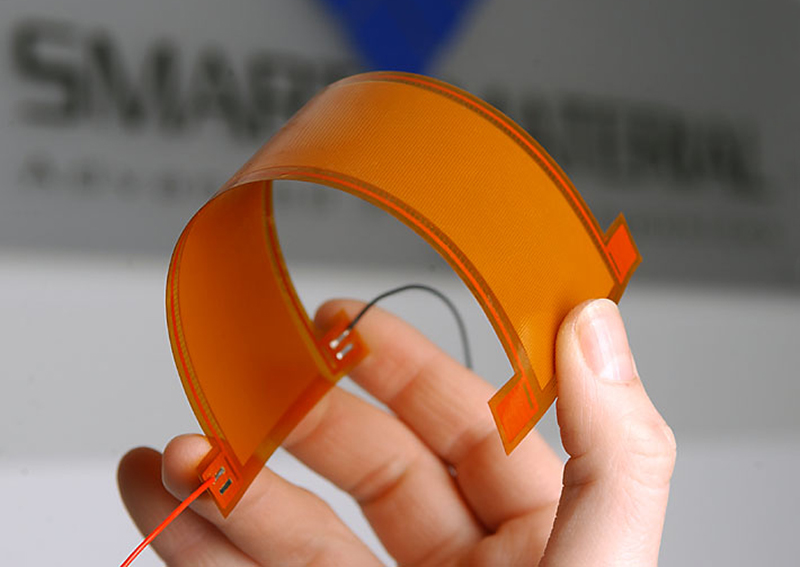
When compared to standard piezoelectric systems, the MFC is much more durable and provides increased unidirectional control. Furthermore, the MFC is designed to be readily integrated into a system as an add-on component or integrated during manufacture.