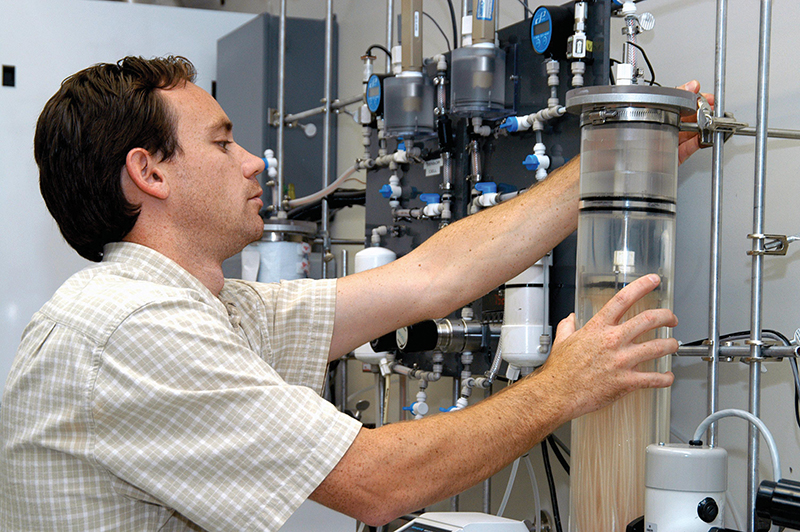
Oxygen Sensors Monitor Bioreactors and Ensure Health and Safety
NASA Technology
In the mid-1990s scientists at NASA Kennedy Space Center were experimenting with an unusual substance: cow digestive bacteria. Could it break down leftover dead plant matter in space into usable organic matter?
To find out, the scientists were cultivating the bacteria in bioreactors and had to constantly check and make sure that appropriate amounts of oxygen were being dispensed. Without enough oxygen, aerobic bacteria (like those of the vast majority of living organisms) would be incapable of their normal metabolism, or harnessing the biochemical energy that enables them to subsist and reproduce. But conversely, exposure to too much oxygen would be toxic and deadly, particularly for anaerobic bacteria.
Researchers at the time were using two sensors, but without satisfaction. The first, an electrochemical sensor, consumes molecular oxygen as part of its measurement. However, when immersed in thick, viscous biologicals (as was the case with the cow bacteria), biofilms develop on the sensor, which can slow the intake of oxygen, resulting in calibration drift, or inaccurate readings.
The second sensor, a fluorescent-quenching sensor, measures oxygen levels by analyzing the fluorescent intensity of an indicator substance while exposed to the testing sample. The calculations derived from the two events have an inversely proportional relationship: The more oxygen there is in a given sample, the less the fluorescent intensity, and vice versa. But this tool is also prone to calibration drift. For example, if during a measurement the light source became inadvertently brighter, then the readout would erroneously suggest a lower level of oxygen was actually present.
Technology Transfer
After learning about the Kennedy scientists’ sensor deficiencies, Needham Heights, Massachusetts-based Polestar Technologies Inc., a company that specializes in high-tech monitoring equipment, conceived an idea to develop a more reliable sensor: one that uses fluorescent quenching in a novel way to determine how much oxygen is present in a given medium.
In 1997 the company received SBIR funding to develop a new sensor. With additional financial backing from the National Institutes of Health the following year, and after a few years of research and development, Polestar had manufactured its own line of optical oxygen sensors.
What makes the company’s sensing technology unique is that the fluorescent lifetime of the indicator polymer, in this case a Ruthenium complex, is used to calculate oxygen levels. Like other fluorescent chemical compounds, the Ruthenium complex emits light when excited by external radiation. (For this purpose, Polestar employs an LED light.) The fluorescence lifetime—for which each compound has its own distinct rate, often in the order of microseconds—is the time after radiation exposure when the compound’s light intensity drops to a little over one-third of its initial emission.
But external factors can quench, or decrease, the fluorescent lifetime of a compound, and such is the case when the Ruthenium complex is exposed to oxygen. Oxygen will take the energy from the compound that would be given off as a photon of light and instead releases it as heat, so the more oxygen there is, the shorter the Ruthenium’s fluorescent lifetime.
Polestar’s optical sensor technology takes this phenomenon into account in order to determine the amount of oxygen that is present in a given sample. What makes this sensor more reliable than previous models is that the underlying math works independently of variables that can affect the accuracy of the readings.
“Our sensors are not prone to calibration drift due to light signal intensity or photo bleaching of the indicator molecule,” says James Kane, the company’s vice president of technology and product development. “It delivers precise measurements time and time again.”
And repetition is something these sensors are able to do on a grand scale. A typical sensor can record about 4 million readings before a red light on the instrument indicates it needs to be replaced. At that point, all the researcher or technician does is screw off the old sensor tip and replace it with a new one—a simpler process than is typical with many electrochemical sensors, which require skilled handling to replace the membrane, refill the electrolyte, and polish the electrode.
“Ours is a very user-friendly system that anyone can operate and maintain,” Kane says.
Benefits
Since entering the market in 2000, Polestar’s oxygen sensors have become very popular with pharmaceutical companies and medical research universities that work with cell culture, fermentation, and tissue regeneration. Drugs that need to be sealed in blister packages that are kept inert are tested with tiny sensors for quality control, and companies are using Polestar’s sensors for this task.
When gas companies started adding ethanol to petrol to create hybrid fuels, they found that their pipes had become more prone to erosion cracking because of the increase in oxygen. Many now use the fluorescent sensors as a safe, electrically inert way of testing in highly flammable environments.
But the company didn’t stop at oxygen detection. In the last several years, Polestar utilized the same optics and electronics technology they originally pursued with NASA SBIR funding to develop carbon dioxide and pH sensors. All three sensors can be plugged into the same instrument, which can house the necessary software for each tool. With other models on the market, one would have to buy a separate instrument for each sensor.
Polestar Technologies continues to grow, and at a prodigious rate: In 2013 alone the company estimates that its workforce increased by 50 percent. Its expertise has also resulted in a contract with the US Army to develop transcutaneous sensors for measuring arterial carbon dioxide in soldiers wounded with traumatic head injuries. Another contract that is underway with the US Navy involves developing a sensor for monitoring the same gas in tankless rebreather SCUBA gear.
It all began, says Kane, with that initial SBIR funding from the Space Agency. “The knowledge that we acquired in optics and electronics from the NASA grant set the foundation for this entire product line,” he says. “It has worked out really well for us.”
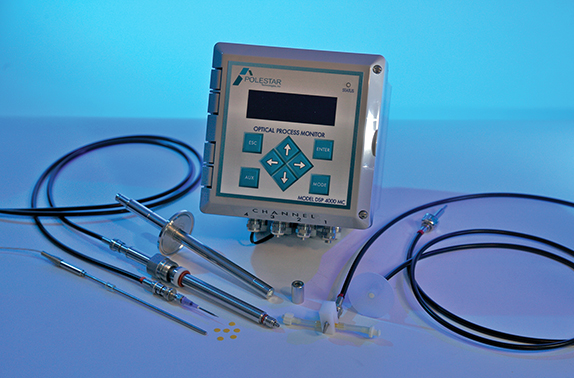
Polestar Technologies’ suite of sensors can monitor oxygen, carbon dioxide, and pH levels. All three sensors plug into a single hardware unit.
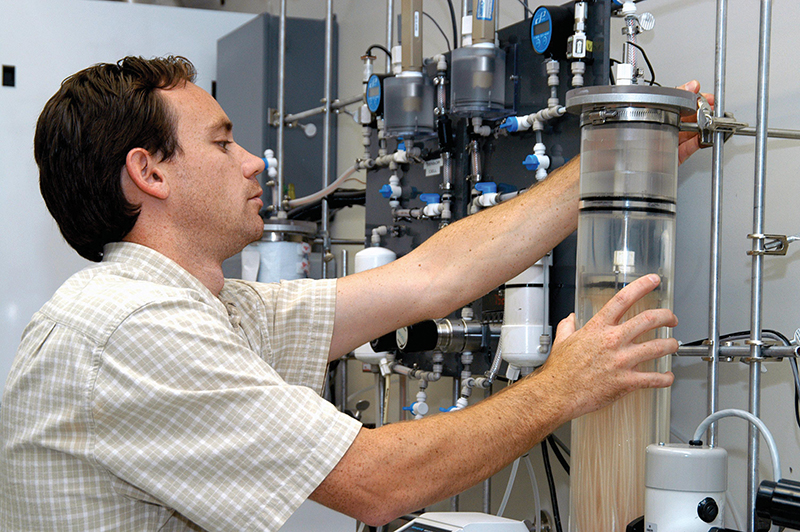
Bioprocess Engineer Tony Rector prepares one of the reactor vessels on the Aerobic Rotational Membrane System (ARMS) bioreactor for initial testing in the Space Life Sciences Lab. ARMS was designed to help treat wastewater onboard the ISS by using beneficial bacteria, which rely on a stable supply of gaseous oxygen to thrive.