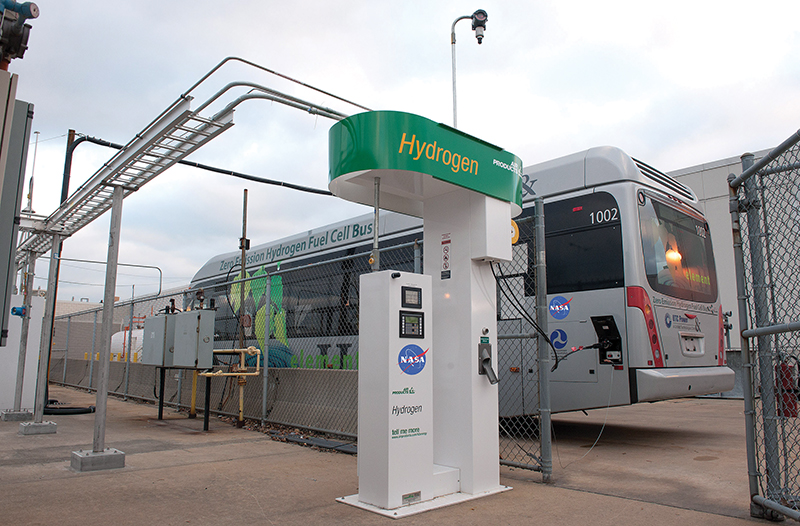
Compact Vapor Chamber Cools Critical Components
NASA Technology
Before the Apollo program sent the first men to the surface of the moon in 1969, in the early-to-mid-1960s NASA’s Project Gemini performed much of the fundamental research required to get there. Over the course of 12 missions—10 of them crewed—Gemini spacecraft launched into orbit to enable the agency to study everything from the health impacts of exposure to microgravity to rendezvous and docking logistics and the demonstration of extravehicular activities.
Another aspect of research involved experimenting with alternative technologies to power a spacecraft’s systems, as the agency believed batteries wouldn’t last long enough for a lunar mission. One technology tested on several missions was the Proton Exchange Membrane (PEM) fuel cell. Invented by General Electric, the device provides electricity by means of a catalyst that strips hydrogen gas atoms of their electrons, which travel through electrical circuits, providing power.
Due to reliability issues, PEM fuel cells were replaced by alkaline fuel cells, which are bulkier but more dependable. The Apollo and Space Shuttle programs went on to use alkaline varieties to power their spacecraft. But recent improvements in PEM technology brought about by NASA, the US Department of Energy, and the private sector have once again opened up the possibility of using the device for space exploration.
In the interest of improving supporting technologies for PEM fuel cells, in the early 2000s Kenneth Burke, an electrical engineer at Glenn Research Center, began looking into new ways of cooling these power-producing devices. Traditionally, NASA has used liquid coolant, which flows into the fuel cells and carries the heat to a heat sink for disposal, adding another level of complication to the system. “The fuel cell has to seal and pump another fluid within it and manage all its plumbing and electronics. It was a system with more working parts than was desirable,” Burke says.
As a workaround to this complexity, Burke turned to a kind of passive, closed-loop technology that would simplify the cooling process. What he had in mind were heat pipes: hermetically-sealed metal plates that use an internal phase-changing fluid to transfer heat. Basically, the heat pipe draws in heat from an adjacent source, which causes the liquid inside to evaporate. The vapor travels to a lower-pressure area of the device where the energy is transferred to a heat sink. Having lost energy, the vapor condenses back into liquid and is wicked by a porous metal structure back to the evaporator section, where the process starts over again.
But the particulars of PEM fuel cell design, to say nothing of the special demands placed on devices destined for space, made existing heat pipes unworkable. For one, instead of the classic tubular design, Burke needed thin, planar heat pipes. The planar heat pipes would be wedged between each pair of fuel cells, which would be stacked one on top of the other. Second, because the stacked fuel cells would exert considerable pressure, the working metal had to be exceptionally strong. At the same time, fuel cost and space limitations meant the device had to be lighter than what was available at the time.
As has happened many times throughout its history, NASA would collaborate with the private sector to make such a device a reality.
Technology Transfer
Founded in 1970, Thermacore Inc. specializes in passive thermal management technology. Burke had worked with the Lancaster, Pennsylvania-based firm in the past, calling them “the premier company” in that arena. “I listed the specs that I needed this heat pipe to have,” he says, “and they said, ‘Yes, of course we can do that.’”
The company first experimented with water paired with copper, a popular material for heat pipes because of its high thermal conductivity, but it was found to be too heavy. That meant they needed to find a lighter material and commit to more engineering research. As a result, in 2008 NASA granted Phase I Small Business Innovation Research (SBIR) funding to Thermacore, followed by Phase II funding later that year.
According to Thermacore’s senior research engineer, Sergey Semenov, what he and his colleagues came up with by 2008 is something that “no one else has in terms of its form factor,” he says, “and it fulfilled all of NASA’s requirements.”
Enter the water-based, titanium vapor chamber. Not only is titanium two times lighter than copper; it’s also considerably stronger. Its properties allow the overall thickness of the vapor chamber to measure a mere 1.3 millimeters while still being able to withstand 2,000 pounds per square inch of force, which means it has more than enough strength to handle the force imposed by several fuel cells clamping together.
What’s more, the company developed a proprietary technique for manufacturing the device that, by the end of its development, had reduced production costs by 90 percent. “It was a big achievement for us because we wanted to make it affordable for commercial applications,” Semenov says.
Benefits
In March 2013 Thermacore released the Thin Titanium-Vapor Chamber Therma-Base. The device provides passive thermal management to heat-generating electronics such as processors, video cards, radio-frequency amplifiers, power amplifiers, and other devices that require lightweight but strong thermal management systems, Semenov says. “The military in particular will find this technology useful because, similar to space missions, some operations also have to deal with space and weight constraints, and the same can also be said of some other commercial industries.”
As for dependability, titanium and water do not react chemically, which means they can’t produce gases that would eventually prevent the vapor chamber from working. With a nonreactive interior, if the device remains hermetically sealed, Semenov says, “it will work forever.”
The advent of this lightweight, thin yet exceptionally strong vapor chamber wouldn’t have happened without the agency, Semenov says. “Without NASA’s support, this product wouldn’t exist. We would still only be using copper-water combinations.”
Burke says the technology was worth the investment. “With these titanium vapor chambers, the agency can one day use PEM fuel cells for manned or unmanned missions to the moon or Mars or to an asteroid. There’s no shortage of possibilities.”
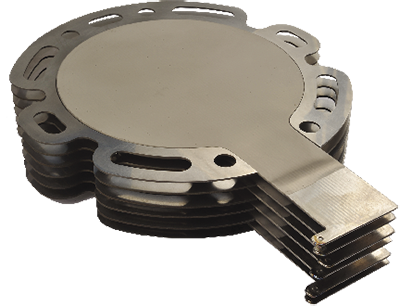
Thermacore worked with NASA to develop the Thin Titanium-Vapor Chamber, a thermal management device for PEM fuel cells, which are being considered for future NASA missions. It is now commercially available as Therma-Base.
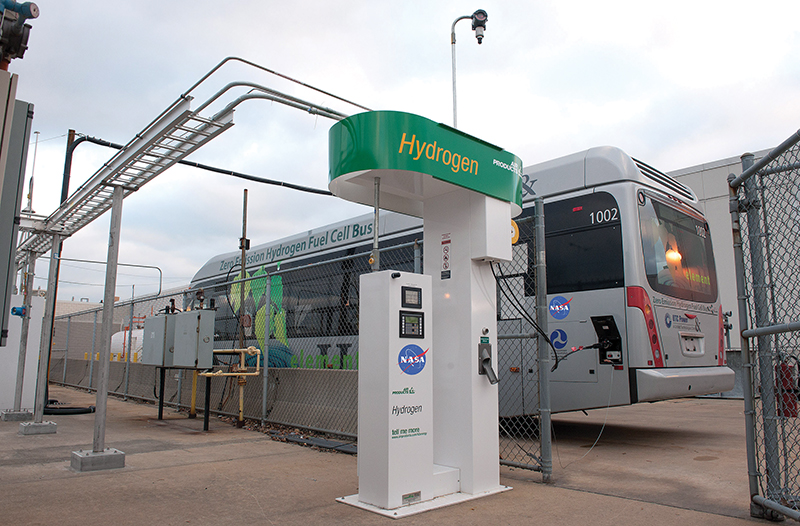
In 2012 Glenn Research Center partnered with the Greater Cleveland Regional Transit Authority (RTA) and other organizations to add a hydrogen-fueled demonstration bus to the RTA fleet. Here the bus is refueling at a station that uses an electrolyzer to convert water into hydrogen and oxygen. The vehicle’s Proton Exchange Membrane (PEM) fuel cells use the hydrogen to generate electrical energy. NASA is looking to use PEM fuel cell technology to power future spacecraft.