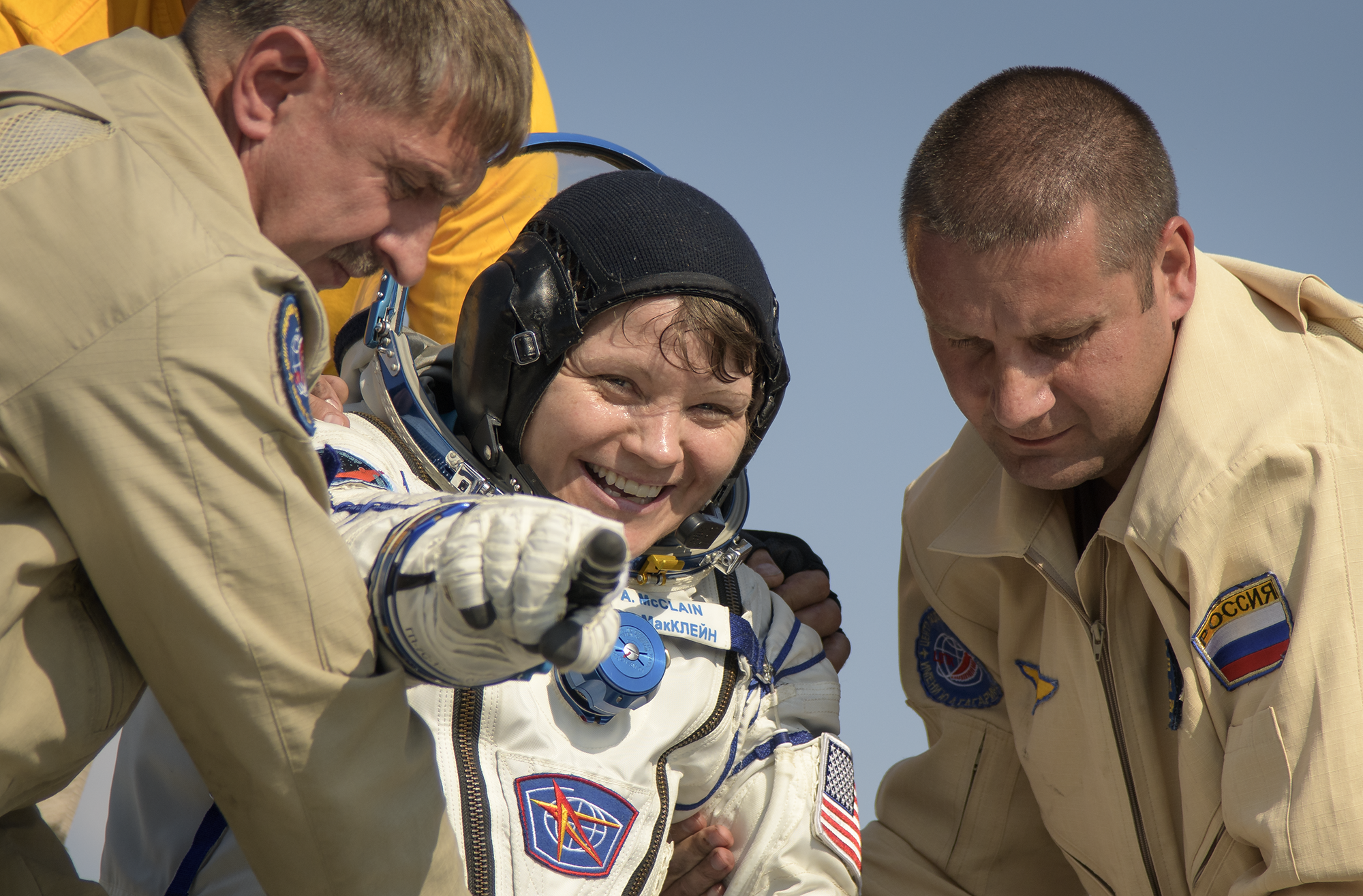
Better Data for Bodies in Motion
Subheadline
A wearable device to monitor astronauts’ tumultuous return to Earth is helping industry
The return to Earth is a rough ride for astronauts, from the violent turbulence of atmospheric entry to a jarring landing. Hitting the ground in a Soyuz capsule is the equivalent of driving a car backward into a brick wall at 20 mph, and it’s resulting in more head and neck injuries than NASA computer models predicted. To collect more data, NASA’s Johnson Space Center in Houston commissioned a Small Business Innovation Research (SBIR) project to develop a wearable data recorder for astronaut spacesuits. One result, created by Diversified Technical Systems Inc. (DTS), is a miniature commercial device that now collects and transmits data for any application from airplane test flights to tracking high-value shipments.
Common data recorders, such as those used for laboratory testing and automotive crash testing, can be bulky and require external power sources. But even smaller versions of that technology weren’t going to work for astronauts, according to Nate Newby, occupant safety analyst at Johnson. The occupant protection tools NASA uses to predict the likelihood of injury under the unique conditions of capsule landings require kinematic measurements defining the motion of a body through space.
“Our predictive tools were adapted from the automotive world and from the military,” he said. “But our environment is a little bit different.” The head and neck are subjected to high rates of acceleration in every direction. The kind of injuries astronauts are prone to don’t occur under other conditions, so NASA had to fill that data gap to improve the predictive model.
DTS already had extensive experience in miniaturizing data recorders, including one data logger that’s embedded in the mouthguard worn by NFL players. NASA engineers worked with the company to adapt that technology and refine it during Phase I and II SBIR projects.
Astronaut Safety
DTS’s work to create a self-contained wearable device that didn’t rely on a wired data connection and was powered by an integrated battery benefited from the agency’s experience with space travel — including proven materials, knowledge of conditions that affect battery longevity, and more. The housing had to contain the hardware and software necessary to take and store motion measurements, with enough room for the power source and wireless communications technology. The project envisioned a small data recorder that could attach to an astronaut’s communications cap and automatically begin recording data when it reached a predetermined velocity.
“The astronauts are in the spacecraft for a while, and you don’t want it to record that whole time, to minimize power and storage,” said Newby. To meet NASA’s specifications, the company needed to gather data about the kind of acceleration astronauts experience and use that information to create a mechanism that could automatically record both launch and re-entry forces.
DTS started with its core technology, designed to capture data for “dynamic testing,” primarily crash, blast, and injury biomechanics testing, according to Mike Beckage, the company’s CTO. The existing hardware and software provided reliable shock and vibration data, which NASA, a DTS customer, already relied on for a variety of aeronautics and aerospace testing.
The agency used this off-the-shelf technology to verify the structural integrity and occupant safety of the Orion crew capsule. Newby also uses a DTS device to collect data from hard landing crash tests performed using test dummies. This work and more helped the Seal Beach, California-based DTS, a brand of Vishay Precision Group Inc., build a good working relationship with NASA for over 20 years.
“A development project like this is a very interactive process, so we had regular meetings to discuss our progress. We identified technology and capabilities that we could build into the product,” said Beckage. Tapping NASA’s expertise was challenging as the COVID-19 pandemic disrupted much of the project, but the company still met the final deadline.
Parachute Drops and Car Crashes
The prototype design, named DXR, met every specification except for size — it’s still a little too big for NASA’s applications. But Beckage said the company based its new TSR AIR data logger on the DXR design. NASA input on everything from new features to the final design made the 2.75-square-inch device ideal for numerous commercial applications.
Adding the TSR AIR to a tailfin or other places on an airplane makes it possible to collect in-flight data. It can also be attached to a trailer transporting high-priority cargo, not only tracking its location in real time but recording the conditions of that trip. The device has wireless charging and wireless communications capability, making it easy to keep powered and to continuously share data.
Safety testing that includes drones, parachute drops, and automobile crashes can also use the device. It can be used to track batches of pharmaceuticals as they go through production lines and the shipping process to provide information about exposure to environments that can degrade medicines as they’re moved around.
In addition to providing an array of hardware, DTS provides the services necessary to help companies get their applications up and running. Beckage said he hopes to continue integrating what the company learns from NASA technologists, serving as a conduit for sharing that store of knowledge.
“We’re thankful to have those opportunities to work on really cool applications for NASA and redefine what’s possible when it comes to testing,” said Beckage.
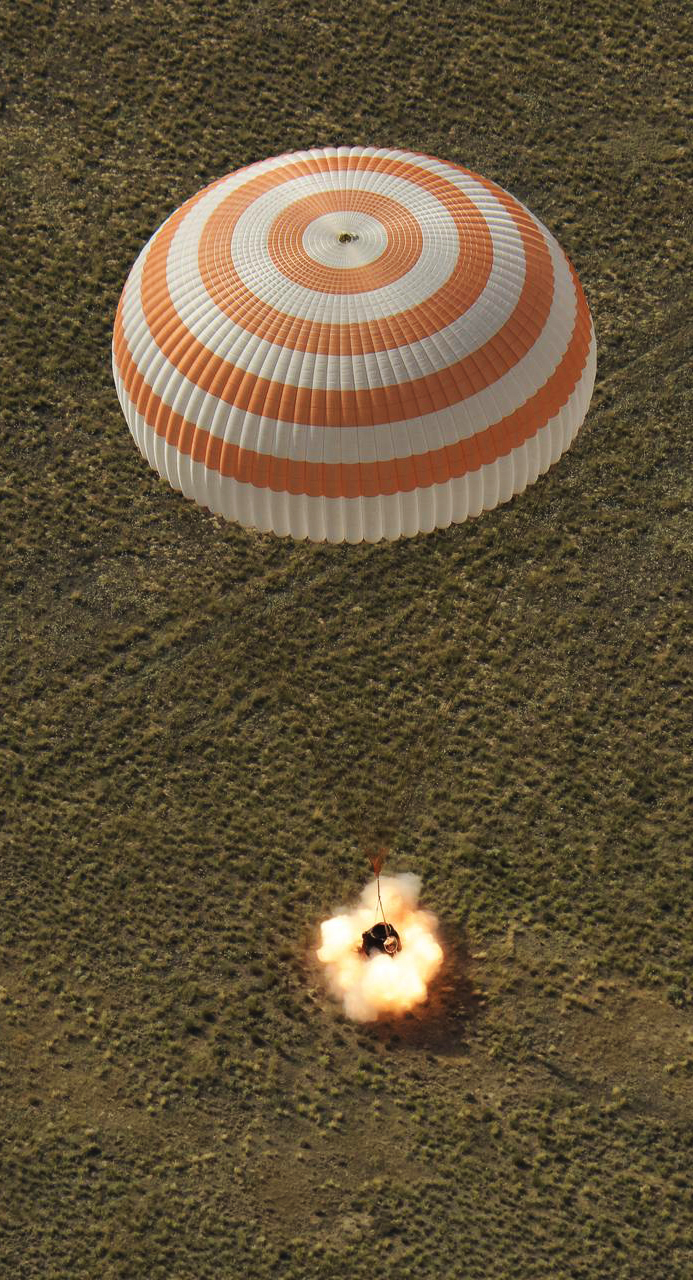
A “soft” landing in a Soyuz capsule is like driving a car in reverse into a brick wall. To help NASA gather information about the cause of head and neck injuries experienced by astronauts, DTS developed a wearable miniature data recorder. Credit: NASA
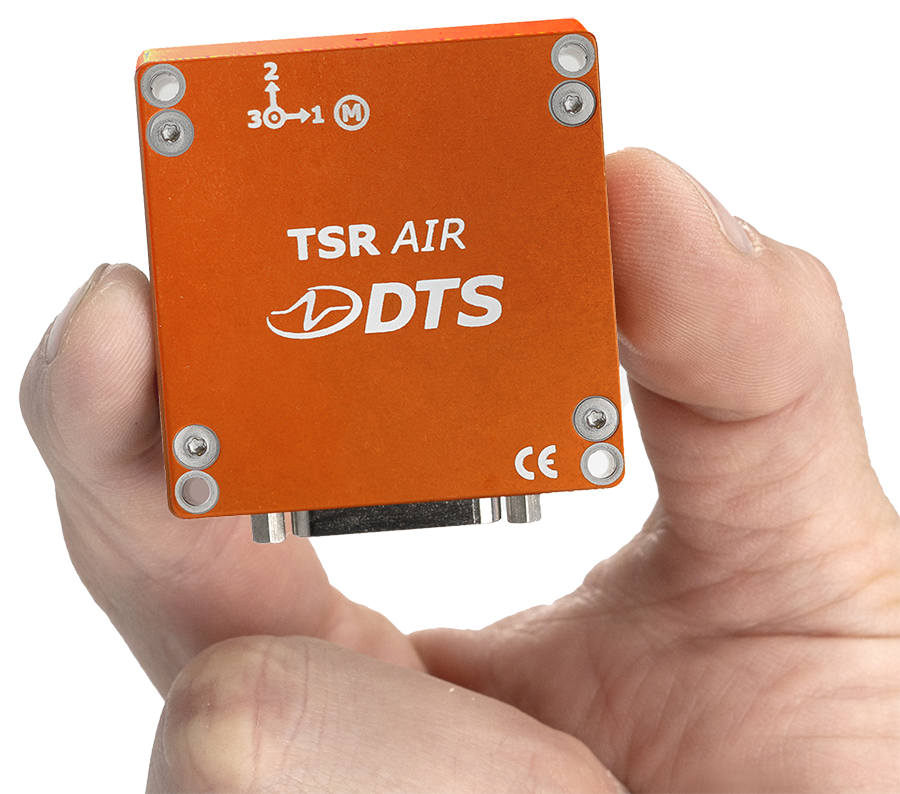
The TSR AIR data recorder measures the velocity and motion of an object. DTS created a wearable version for NASA, but now industry uses the device for safety test flights, tracking the location of high-values assets, and more. Credit: Diversified Technical Systems Inc.
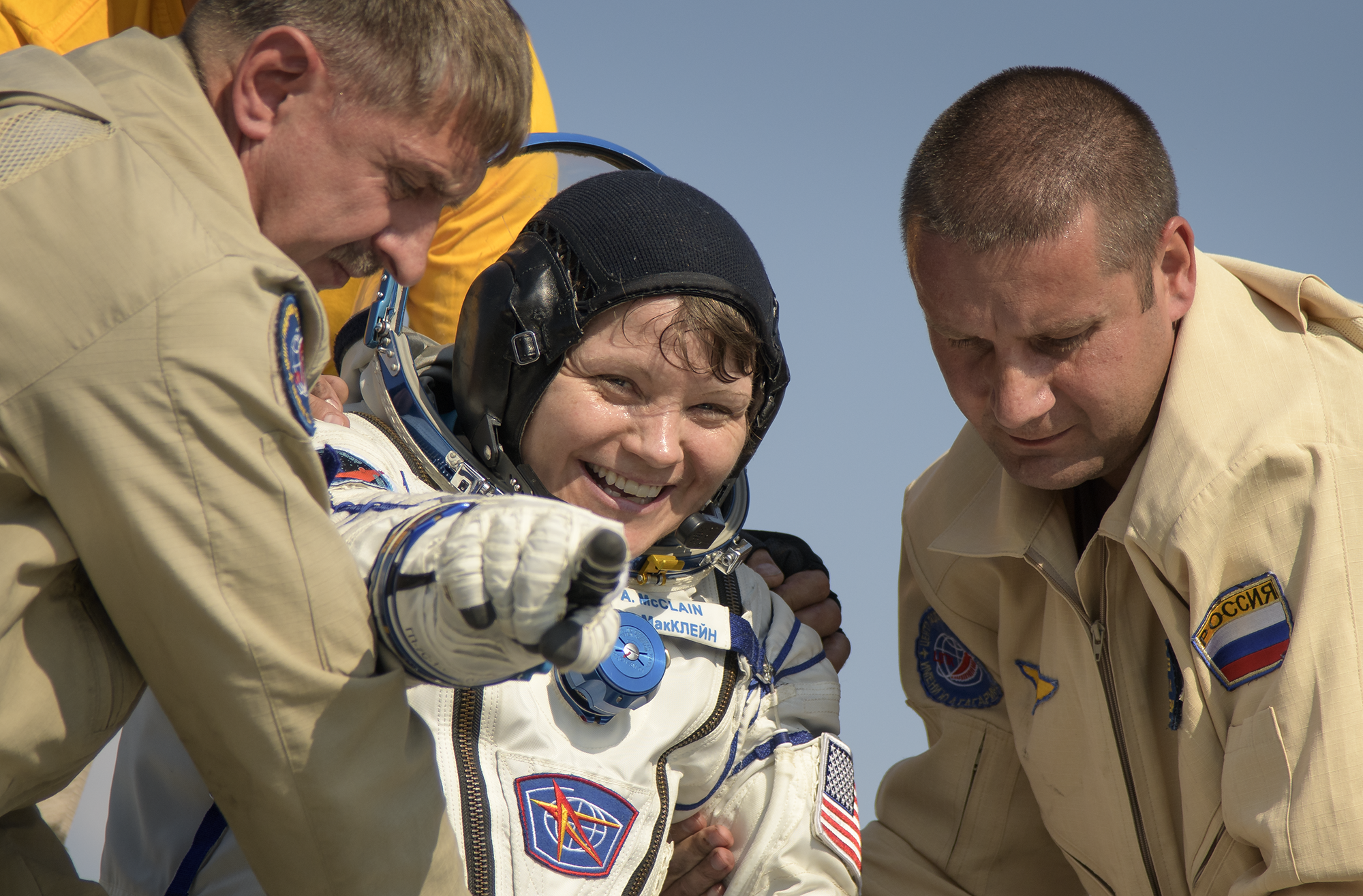
Astronaut Anne McClain returns to Earth after 204 days in space, a duration that weakens bones and muscles. To better understand how the velocity of descent and landing can cause head and neck injuries, Diversified Technical Systems (DTS) created a wearable data recorder. Credit: NASA