Cleanroom Contaminant Monitor
Helping to keep the work-setting free of airborne molecular contamination is a task of Femtometrics, Inc. of Irvine, California. The company's Real-Time Non-Volatile Residue (NVR) monitor was developed under a Small Business Innovation Research (SBIR) contract for John F. Kennedy Space Center (KSC) in Florida.
Femtometrics had responded to Kennedy Space Center's needs by proposing an advanced, highly sensitive surface acoustic wave (SAW) microsensor capable of detecting sub-monolayer deposition in cleanrooms where aerospace systems are assembled.
Initial criteria established by KSC called for a technology that could regulate the accumulation of nonvolatile residues in cleanroom environments. The smallest speck of material can harm sensitive payloads being prepared for launching. An ultra-clean work environment for assembly and final check-out of a spacecraft is a must.
As specialists in trace analysis and instrumentation, Femtometrics had responded years earlier to an SBIR solicitation by Langley Research Center. Langley's interests centered on size distribution and mass concentration of aerosols and chemical vapor in the stratosphere. NASA SBIR Phase I and Phase II contracts were awarded to Femtometrics resulting in a highly sensitive aerosol detector for environmental researchers.
Stimulated by the SBIR contract wins, the company set about developing proprietary SAW resonator technology. A new type of sensor evolved from the research.
The advanced sensor has the ability to measure a range of chemical vapors by applying chemical-specific coatings on the sensing surface. The SAW proved extremely sensitivet--two orders of magnitude greater than a competing, NASA-developed instrument built to conduct the same environmental monitoring function.
Femtometrics equipment can employ multi-SAW sensor array systems. These offer a range of absorption characteristics. When exposed to a chemical-vapor environment, the arrays produce a "fingerprint" of the specific chemical vapor or vapors present. Coupled with custom-programmed adaptive neural network software, the chemical compound fingerprint is analyzed and identified.
William Bowers, President of Femtometrics, explains that a prototype Real-Time NVR monitor was used as an engineering tool during the ground integration and launch processing of the Hubble Space Telescope replacement optics and science instruments during its first servicing mission in 1993. Hubble's second servicing visit by astronauts in 1997, Bowers adds, made use of three passive sensor elements provided by Femtometrics which successfully measured on-orbit contamination.
Commercial applications of the Real-Time NVR Monitor now include Class 1 cleanrooms at semiconductor and hard-disk manufacturing plants. Also, the monitoring system is a process tool to measure condensable contaminates in ultra-high purity operations that use gas and solvents.
Other federal organizations, such as the Department of Defense and the Department of Energy, have found need for the SAW chemical-vapor detection systems built by Femtometrics. Applications include scientific research and chemical warfare detection.
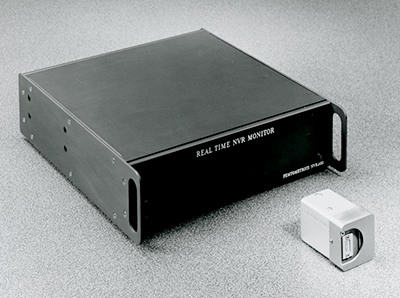
Real-Time Nonvolatile Residue Monitor developed by Femtometrics, Inc. is built to monitor for contaminants in cleanrooms for spacecraft check-out but has found a new home in factories of microelectronic chip makers.
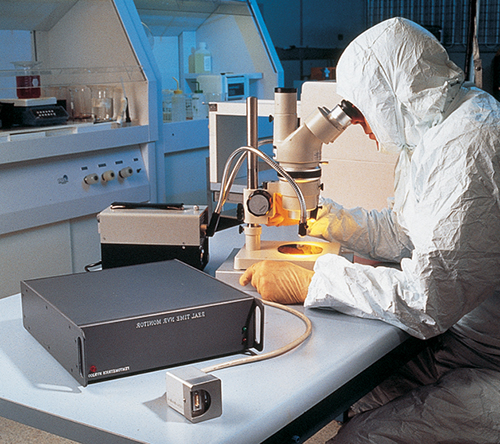
One use of Femtometrics, Inc.'s NVR-200 is in cleanrooms and in process control by semiconductor manufacturers.