Cool Software for Hot Materials
As part of NASA's efforts to build upon the philosophy of "cheaper, better, faster," one way to achieve that standard is through the increased efficiency of turbine engines. To help this goal along, NASA's Glenn Research Center awarded a Small Business Innovation Research (SBIR) contract to Deformation Control Technology, Inc. (DCT) of Cleveland, Ohio.
Under the contract, DCT has developed a computer model as an aid to designing ceramic coatings to extend the life of the coating and the coated component. NASA's interest in the research stemmed from a desire to develop quantifiable descriptors for the complex interactions experienced in thermal barrier coating systems (TBCs). Typical TBCs are composed of three "layers": the metallic component, an oxidization resistant "bond coat," and finally, the ceramic top coat.
This software allows for coating designers to measure the stresses being placed on coatings using computer simulation. Thermal barrier coatings have traditionally been evaluated using expensive "Burner Rig" tests. These tests involve a series of sequential heating and cooling cycles run on cylinders coated with the substance undergoing testing. The coated cylinders are run through varying configurations within a temperature range of 30-1200 degrees Celsius. DCT's new software will contribute toward reducing the need for extensive "Burner Rig" tests, since results can be predicted prior to actually producing the coating.
DCT's pioneering work involved the modeling of the thermal barrier coating system through finite element analysis and adding a statistical software package that measures the influence of material stress drivers on the internal stresses developed during thermal cycling.
The benefits of this research have meant a reduction in the cost of experimentation and the development of new design concepts. The results derived from the prediction models will support the development of coatings that can be applied to turbine engines. The turbine engines, with improved coatings, can operate at higher temperatures with improved efficiency.
The modeling aspect of the research provided one of the first descriptions of the role of bond coat oxidization in thermal barrier coating breakdown. In addition, other bond coat and top coat properties which may influence TBC fatigue have been identified.
Another innovation in the DCT model was accounting for the growing oxide layer between the bond coat and the ceramic layer. This oxide is formed at high temperatures when the porous properties of the ceramic enable oxygen to penetrate to the bond coat surface. By accounting for the oxide layer in its models, DCT was able to provide a sound description of the role of oxidization in TBC failure.
DCT's new method has been successfully used in the TBC design for electrical power generation turbine applications. Future applications for improved TBC systems include aerospace, land-based turbine, and diesel engines.
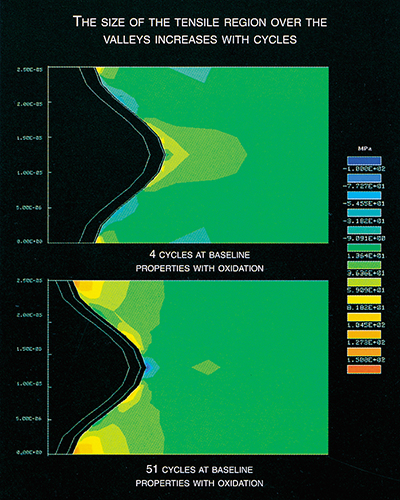
DCT's software can generate predictive computer models for coatings, saving time and money on coating design.