Grace Under Pressure
Developed in response to a NASA requirement to remotely measure tension in critical bolts on the International Space Station, American Remote Vision Company's (ARVC) SureBolt™ Correlation Bolt Gage is the first ultrasonic system to capture an entire "echo" pulse for determining the change in time of flight of an ultrasonic signal traversing a fastener for tension measurement. An ultrasonic bolt gage can characteristically be thought of as a "super accurate ruler" that measures how much a bolt stretches under tension pressure. To determine the amount of stretch, the bolt gage sends a sound pulse into one end of a bolt, and then measures the time for the echo to return.
Prior to the invention of SureBolt, ultrasonic bolt gages proved limited in reliability and resolution because they only tracked one point, or one zero crossing, in the echo time-of-flight assessment. The main problem encountered when using these one-point gages is known as the "peak-jumping" phenomenon. Peak-jumping is a result of the echo waveform distortion that often occurs when tension is applied to a bolt. This waveform distortion causes the bolt gage's zero-crossing detector to jump to another part of the echo waveform without any indication that this peak jump has occurred. Because SureBolt takes measurements using all of the sampled points of an echo waveform, and not just one zero-crossing point, the correlation technology provides far more accurate and reliable readings than its one-point predecessors, thus reducing the errors, inefficiencies, and frustrations generally associated with the use of bolt gage systems.
Furthermore, if any waveform distortions occur while using SureBolt, the system, which is built into an industrial-grade laptop computer, overlays and displays entire waveforms so the user can visually determine and analyze any effect on the data. The standard SureBolt system hardware has the capability of recording over 1 million bolt tension readings—with their complete waveforms—in Microsoft Excel-compatible format. The user-friendly Tension-Not-Torque© software interface offers tension change graphing in real time, and a place to store field notes, special parameters, tension calibration constants, and temperature changes for each measurement. SureBolt is also Web-ready, so users such as engineers and managers worldwide can access measurements in real time.
SureBolt correlation technology was developed over the span of 15 years by Stuart Gleman and Geoffrey Rowe while working for various contractors at NASA's Kennedy Space Center. A prototype of the SureBolt Correlation Bolt Gage was used at NASA's Marshall Space Flight Center on Space Station Common Berthing Mechanism Attach Ring flange bolts during preflight pressurization tests of the Structural Test Article Node, and at Boeing's facility in Huntington Beach, California, for tests on the Pressurized Mating Adapter and its Attach Ring. Data obtained from the Marshall tests demonstrated that, when tested side-by-side with single-point gages, the SureBolt correlation technology achieved superior accuracy and performance. A later prototype was used on the X-33 hold-down bolts.
Gleman's company, ARVC, which is based in Titusville, Florida, participated in a Phase I Small Business Innovation Research (SBIR) contract with Kennedy in 1998 for advanced development of correlation bolt gage technology. Later that same year, Kennedy patented the correlation bolt gage, and then licensed it to ARVC 3 years later in 2001.
The technology has been used on fasteners as small as fine-threaded, 1-inch bolts, and as large as 18-inch-diameter by 30-foot-long tie rods. SureBolt is finding increased application within NASA and the aerospace industry, as well as in the automotive and nuclear industries.
SureBolt™ is a trademark of American Remote Vision Company.
Tension-Not-Torque© is a copyright of American Remote Vision Company.
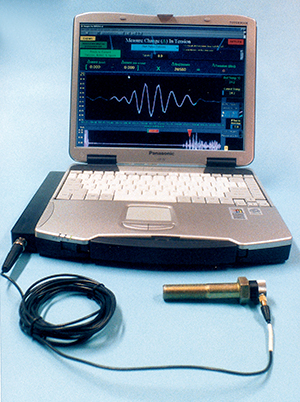
Built into an industrial-grade laptop computer, the SureBolt™ Correlation Bolt Gage captures an entire "echo" pulse for determining the change in time of flight of an ultrasonic signal traversing a fastener for tension measurement.