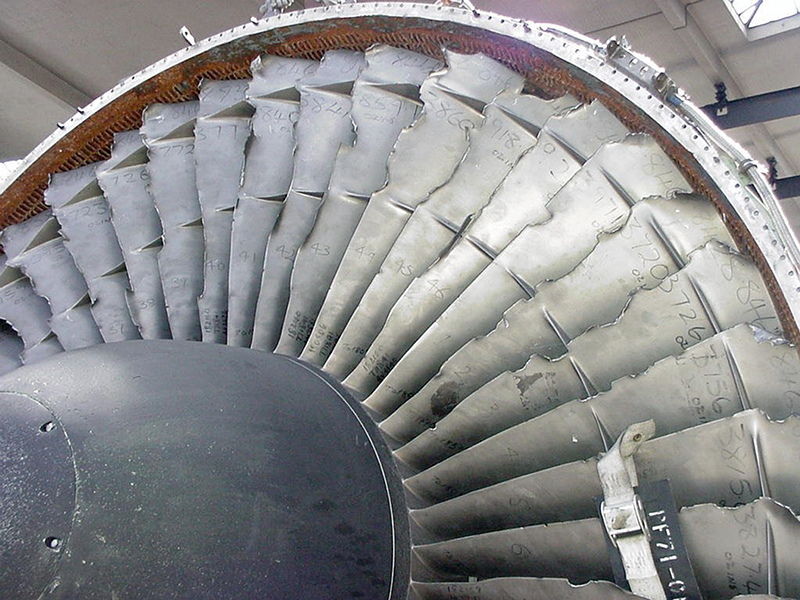
New Sensor Gaining Interest on Industry Radar Screen
While radar is typically used to track large objects that are relatively far away, an Atlanta, Georgia-based start-up company is using the technology in a counter-intuitive way to track very small changes in displacement at close proximity.
Radatec, Inc., a designer, manufacturer, and implementer of sensor systems for monitoring combustion-zone components in turbine engines, was formed in 2001 to commercialize the patented radio frequency vibrometer technology from the Georgia Institute of Technology (Georgia Tech). In readying the technology for the commercial market, Radatec received assistance from NASA's Dryden Flight Research Center in the form of Phase I and Phase II Small Business Innovation Research (SBIR) grants totaling over $650,000. The company's Phase II submission was ranked the number one SBIR proposal out of Dryden for 2002.
The SBIR contracts helped fund further development of Radatec's proprietary, noncontact microwave sensor technology for monitoring complex heavy machinery used on aircraft and in power plants, such as gas and steam turbines. The ensuing hardware/software system can warn of impending problems before they become dangerous. According to Scott Billington, co-founder of Radatec and former research faculty at Georgia Tech's Manufacturing Research Center, the sensor gives the operators of heavy machinery the capability to measure critical pieces of equipment in hostile environments where conventional sensor technology cannot operate. "Our radar-based system will enable operators to more effectively schedule costly maintenance and to run equipment longer. This will help reduce the cost of operating and maintaining these systems," Billington elaborated.
Since vibration measurements are the most important and informative indicator for accessing the health of rotating machinery, Radatec's sensor systems have found their widest application in protecting the investment of large, critical rotating equipment. According to the company, there are currently tens-of-thousands of turbines in use for military and commercial aircraft, representing billions of dollars of investment. Significant dollar amounts are spent maintaining the machinery, much of which is consumed in preventative maintenance, inspection, and replacing questionable parts. In power plants, more than 6,000 steam and gas turbines supply America's power grid alone. With downtime costs of $8,000 to $10,000 per hour and maintenance costs that take up 15 percent of the total operating budget, this sector represents an attractive opportunity for Radatec.
The invention has several key capabilities that provide an advantage over existing sensor technologies. It provides very precise data regarding component health while a turbine is in full-speed operation. Previously, operators were forced to remove a turbine from service, dismantle it, and inspect it to determine component health. Moreover, the new sensor measures component deformations with 5-micron resolution, withstands temperatures exceeding 2,500 ºF, is unaffected by interference that disrupts other sensors, and accurately assesses vibrations deep within an engine that were previously immeasurable.
In January 2003, Radatec proved just how advantageous its new sensor is. The company installed a sensor system at the Navy's Patuxent River Naval Propulsion Laboratory in Patuxent River, Maryland, as part of a 6-month, head-to-head test of systems to measure the health of a turbine disk that holds turbine blades in place. The competing systems, installed by the Defense Advanced Research Projects Agency (DARPA), consisted of capacitive, laser, and eddy current sensors. The turbine disk that was subjected to the test was pre-stressed with defects and in operation for over 800 hours at 1,200 ºF, and at speeds ranging from 1,500 rpm to 18,000 rpm.
Radatec's system performed favorably against the competing sensor systems in terms of data fidelity and probe survivability. Due to its high bandwidth capability, the Radatec system was able to profile the blades with over 2,000 data points per blade, even at the maximum speed of 18,000 rpm. These profiles enabled Radatec to accurately monitor disk failures, based on blade geometry changes over the course of the test.
From a reliability standpoint, Radatec was the only system to complete the test with original equipment. All competing systems required replacing components that failed due to exposure to the high temperature (one system required 14 sets of probes). Toward the end of the test, the disk began to fragment, impacting all of the sensors. Radatec's sensor absorbed the impact and continued to operate, while the other sensors were completely destroyed. Sustained functioning was due to the fundamental nature of Radatec's waveguide probe, which can be constructed of very durable materials and requires no sensitive components for operation. DARPA has since contracted Radatec to install its system for upcoming tests located at the Patuxent laboratory and another major turbine site.
A separate testing initiative demonstrated that the Radatec microwave sensor system would also benefit the automotive industry, when used as a radar technique for active suspension control. The purpose of a vehicle's suspension system is to isolate the shock and vibration caused by road and terrain irregularities from the main body of the vehicle, yet still provide the necessary ground contact to allow the vehicle to stay in control. Components in such suspension systems have traditionally been passive springs and dampers. Active suspension systems, on the other hand, are made up of components that can alter their properties or add energy to the suspension. They were developed to increase performance and handling of the vehicle and the durability of the components, improve rider comfort, and allow for faster speeds over irregular terrains.
Radatec's radar vibration sensing technology is also well-suited for noncontact measurement of road/terrain surfaces immediately ahead of a moving vehicle. This method of sensing is unaffected by dust, debris, rain, or other obscurants, and can be mounted on a vehicle behind a radio-transparent shield, out of harm's way.
In potential future military applications, the microwave sensor could improve the accuracy of fire-on-the-move when vehicles with moving weapons platforms are faced with rough terrain. When added to such a vehicle, like a tank, the sensor technology would provide information to predict the terrain about to be encountered and allow actions to be taken before the event, rather than after.
Radatec is a part of the Georgia Tech's VentureLab program, which assists faculty members in bringing university-based innovations to the commercial marketplace. VentureLab provided early assistance to Billington and Cofounder Jon Geisheimer, who was a faculty member at the Georgia Tech Research Institute when the company was established. During this time, the founders designed and built a laboratory prototype, which was the basis for their application to the NASA SBIR program. A successful Phase I project led to follow-on Phase II funding, and both founders agree that the NASA SBIR awards "provided a true heartbeat for Radatec as an operating company."
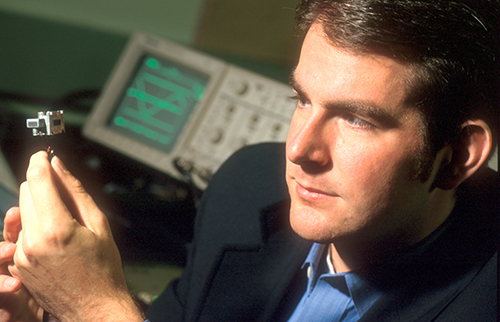
Radatec, Inc., Cofounder and President Scott Billington studies his company’s noncontact microwave sensor. The patented technology was commercialized by Radatec to monitor complex heavy machinery used on aircraft and in power plants.
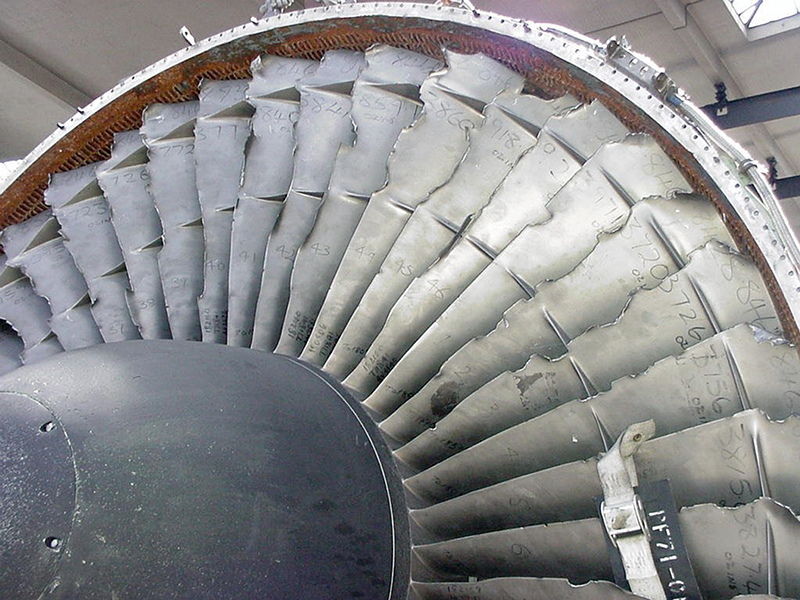
Radatec's sensor provides very precise data regarding component health while a turbine is in full-speed operation.