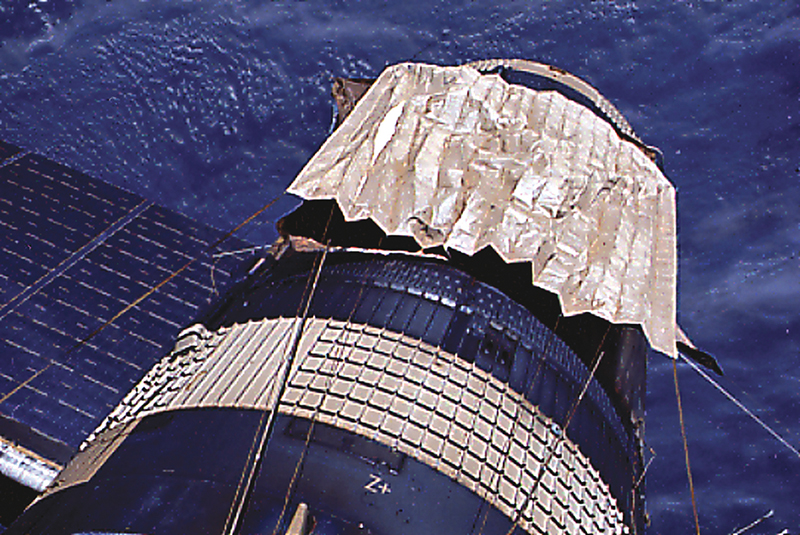
Reflecting on Space Benefits: A Shining Example
Originating Technology/NASA Contribution
NASA has long been known for having developed the thin, shiny reflective material used to insulate everything from the Hubble Space Telescope to hikers, from the Mars rovers to marathon runners, from computers to campers, from satellites to sun shields, and from rockets to residences. It is one of the simplest, yet most versatile spinoffs to come out of the Agency.
The insulating material, a strong, plastic, vacuum-metallized film with a highly-efficient, infrared-reflective, vapor-deposited coating of aluminum, was created to be very lightweight in order to minimize weight impact on vehicle payload while also protecting spacecraft, equipment, and personnel from the extreme temperature fluctuations of space.
It has been employed on virtually all manned and unmanned NASA missions. The shiny insulation which coated the base of the Apollo lunar landing vehicles is perhaps one of the most memorable early displays of this technology, and the bright, reflective honeycomb on the James Webb Space Telescope prototype is a testament to its lasting usefulness.
Partnership
The material is created by depositing vaporized aluminum onto thin plastic substrates. The result is a thin, flexible material that provides superior thermal-reflective properties. The highly pure aluminum coatings are carefully matched to their substrates to efficiently redirect infrared energy—infrared waves being the chief component of thermal energy in the near-vacuum conditions of outer space—to create either first- or second-surface reflecting. In some instances, the material is intended to deflect the infrared rays, and in other cases, it is meant to conserve them as a passive warming system.
Early in the Space Program, the National Metallizing Division of Standard Packaging Corporation, headquartered in Cranbury, New Jersey, was a supplier of this reflective material to NASA. In fact, it was one of the original subcontractors NASA turned to for design and supply of the material, and it was able to branch off from this work into the more general, terrestrial insulating applications, like building insulation.
It was National Metallizing that NASA turned to for assistance when, in May 1973, during the first few days that Skylab was in orbit, it was malfunctioning and overheating. A heat shield broke off during launch, and air temperature inside the orbiting station began approaching 130 °F. NASA was concerned about the condition of food, film, and other equipment inside, as well as plastic insulation and possible toxic gases if the temperature rose too high. The staff at National Metallizing was called upon by engineers at Marshall Space Flight Center to help create an emergency parasol-type sunshield that helped save millions of dollars worth of equipment, years of research, and allowed, for the first time, a habitat for astronauts to live and work in space.
Through a series of mergers, acquisitions, and transfers of ownership, National Metallizing’s factory doors eventually closed. A former employee, though, David Deigan, took advantage of the remarkable material the company had been manufacturing for NASA and founded a company to continue producing it, branding it as Heatsheets. The company, AFMInc, was originally founded as JSC Enterprises, a solely owned proprietorship, in Ridgewood, New Jersey. The “J” stood for Jennifer, “S” for Stephanie, and the “C” for Christopher, the names of Deigan’s three children.
He incorporated in 1982 as AFMInc (Advanced Flexible Materials), because the name JSC, Inc. was already taken, but the company’s story actually goes back a few decades further than this.
Product Outcome
In 1959, the Russians were the first to successfully launch a probe to the far side of the Moon—and return pictures—thus firing the starter pistol for the Space Race. Meanwhile, back in New York, a high schooler, David Deigan, heard a similar shot ring out, and on a lark with some friends, fell in step with a crowd running a marathon. With little prior training, he still managed to finish the event, and even though he paid for it with muscle aches and soreness, he had caught the marathon bug.
Granted, the illness remained dormant for 20 years, as it wasn’t until 1978 that Deigan attempted another marathon—this time with more training and preparation. It was a marathon in New York City that stretched its 26.2 miles throughout Manhattan’s five boroughs: Staten Island, Brooklyn, Queens, the Bronx, and Manhattan, where it finished in Central Park at the Tavern on the Green.
When the runners finished, one of the problems they ran into was keeping themselves warm. The race is held in the fall of each year, either in October or November, and weather in New York, like in many places around the country during these months, can be rather fickle. It might be balmy. It might snow. With masses of people crossing the finish line, it was taking each person an average of 20 minutes to get to their clothes. Hypothermia was settling in when the runners stopped running, and more people were making it to the first aid tent than were to their street clothes.
The Association of International Marathons and Road Races, a nonprofit group that organizes races, met to discuss this problem. They tested several products and settled on the original “Space Blanket” from Metallized Products, an early company that had taken advantage of the NASA technology. Although fine for many situations, and ideally suited for this use in many ways, the blankets were each folded and packaged, a seemingly small detail that had severe impact on their usefulness in this situation—with hundreds of runners crossing the line every few minutes, the blankets just took too long to dispense, unwrap, and unfold, but they were still, at that time, the most viable solution.
Still running, during the 1979 New York City Marathon, Deigan crested a hill in Central Park and crossed the finish line. What stood out to him was not that he had made it 26.2 miles; rather, he was marveling at the silver caterpillar of people wiggling away from the finish line. As he recalls “I crossed the finish line and followed the runners in front of me as we were wrapped in metallized polyester sheets and guided onto and over a hilly path to the reunion area.” He recalls that it looked like a dragon from a Chinese New Year’s celebration. He had the idea at that point that the New York Road Runners Club, Inc., the group that organizes the New York City Marathon, could transform the expense of the silver blankets into racing revenue through branding.
Deigan, the former employee of National Metallizing, also thought of a solution to the problem of having to unwrap and unfold the blankets. The insulating material could be shipped flat and unwrapped on a pallet, thus eliminating the time-consumption problem.
During the first few years, the blankets were branded with the Road Runners logo, a bright red apple; but in 1982, industry had taken notice of the advertising opportunity and major corporations branded the marathon as well as 10 smaller races, and the idea really took hold. That following year, the Chicago and Boston Marathons took interest in the new product and found sponsors to brand their races as well.
Now, most major marathons in the United States, many in other parts of the world, and a number of smaller races employ the blankets, mostly for the purposes of preventing hypothermia, but also because runners have come to expect them. They have become synonymous with finishing a race.
The blanket printing process has, over the last few years, gotten increasingly sophisticated. This past year, for the Marine Corps Marathon, in Arlington, Virginia, AFMInc shipped 24,000 camouflaged finish line Heatsheets to cover the runners as they finished the race. The product has also advanced over time and is now manufactured in a variety of ways, including on rolls and perforated at 6-foot intervals for quick dispensing. Most notably, though, the sport has really progressed. It has taken on mass appeal as a sport where amateurs line up with Olympians. In fact, it is estimated that 700,000 marathoners cross the finish line in the United States alone each year, in the dozens of races taking place around the country.
In 1996, Runner’s World, a monthly publication devoted to news of interest to joggers, ran an article on Deigan and AFMInc’s endurance in the marathon safety culture. Deigan received a call from a plant manager at Encompass Group, of Addison, Texas, who had just started running marathons and had read the article. The plant manager, Lloyd Burnett, told Deigan about Thermo-Lite, an advanced variation of the infrared-reflective aluminized material that his company was manufacturing.
At the time, Thermo-Lite was being used as bed sheets in hospital settings as passive hypothermia prevention for pre- and post-operational patients, for staff in scrubs who work in chilled environments, and as surgical drapes, often including a cut-out access area, giving surgeons access to specific areas of the body while covering the rest. The sheets were softer and quieter than most reflective insulating materials, as they did not have the crinkle and rustle of metallized plastics.
Burnett and Deigan saw potential for the Thermo-Lite and Heatsheets in a line of adventure and extreme weather gear, which AFMInc then sold through Adventure Medical Kits, of Oakland, California. The products, emergency bivvies and rescue blankets, made their way to Alaska where they were purchased by Becky and Doug Bowers.
The Bowers live at the Tolovana Roadhouse in the outreaches of Alaska, 50 miles from the nearest road and the small town of Nenana. They grow their own vegetables, hunt, fish, and trap. Since public utilities do not run to their remote outpost, their power is generated by wind mills and solar collectors. They use this power, in part, to run a small business, Midnight Mushing Outdoor Gear, making the types of rugged, cold-tolerant outdoor gear needed for their climate, where, on a nice day, temperatures run well into the negative digits.
Most of the year, they are confined to their home, where Doug conducts the marketing and business side of their enterprise, while also making the buttons and pulls for their line of parkas and anoraks out of caribou bone and antlers, and Becky designs the garments. Each item, including the vests, mittens, parkas, walking bags (a type of mobile sleeping bag), and pullovers, is made by hand, with added details that make each one unique, but still representative of traditional Alaskan designs.
In addition to their aesthetics, though, the garments are tested thoroughly for high performance. Becky and Doug use everything for a full season before offering them for sale. As might be imagined, one of the key factors they test is an item’s insulating ability. Many contemporary insulating fabrics are wicking, which draws the perspiration away from the body; but after it has been wicked, the insulating barrier is then wet. The ideal solution is to combine the insulating material with a vapor barrier. Unfortunately, many of the different materials traditionally used as vapor barriers are bulky or noisy. This is where Thermo-Lite enters the picture.
On one of their trips into Nenana, Becky purchased one of the Thermo-Lite blankets. She cut it into pieces and sewed it into the linings of several pairs of mittens.
The mittens were put to the test in the winter of 1999, shortly after Christmas, when Becky and Doug left Nenana to trek the 50 miles back to theirafter conducting some routine business. Doug was leading the way on the snowmobile with a load of gear, and Becky was following with a team of sled dogs. The two were enjoying the unseasonably warm weather, and the trip was uneventful.
Two days later, the temperature started to drop, reaching -55 °F by the time night fell and continued dropping through the night. The thermometer in their woodshed the next morning read -65 °F. The weather was expected to hold at this temperature for at least a week, and the Bowers had only enough food for their 25 sled dogs to last another 4 days.
They determined to make the trek back, through the bitter cold, into Nenana, so they made makeshift dog coats out of squirrel-damaged blankets, fired up the snowmobile, and left. The trip took 7½ hours, with temperatures nearing -72 °F, 144 degrees below room temperature!
During that time, the starter pull rewind failed on the snowmobile, which meant Doug had to run the engine idle high to avoid stalling and then drive extra slowly so as not to overheat the engine. Meanwhile, Becky’s chemical hand warmer failed near the halfway point. She wore her new, experimental Heat Barrier Mitts the rest of the way, and to her surprise, and great relief, her hands stayed warm. Ahead on the snowmobile, which is not equipped with heated grips, Doug wore a pair of work gloves under a pair of the mitts, and his hands, too, stayed warm.
After this event, Becky and Doug decided to add the Thermo-Lite mittens to their Midnight Mushings product line. Becky eventually worked her way through a line of phone calls and got through to Deigan, then asked if she could buy seconds of the material. After hearing her story, not only did Deigan agree to supply Becky with factory seconds, he took a plane up the West Coast to see the Tolovana Roadhouse where the Bowers live.
Midnight Mushing’s resulting Heat Barrier Mitts employ a 330-denier Supplex Cordura outer shell, a material that owes its origin to work done by DuPont in the 1920s to make super-strong tires for Army vehicles. It has been refined to the point now, where it is as supple as cotton. The mittens also have Tuff-Grip palms, which stay flexible even in extreme cold, and, of course, the Thermo-Lite insulation. They are very popular with the trappers who turn the mittens inside out when perspiration builds inside, wait a few seconds for the moisture to freeze, give the mittens a whack to crack off the ice, and then put them back on.
Becky has been wearing the mittens for several seasons now, and with the money she has saved from not having to purchase a case of chemical warmers each season, the mittens paid for themselves within the first year. She had had considerable tissue damage to her hands from repeated frostbite, and wearing these mittens for the past few years, her hands have had a chance to start healing—a considerable boon considering that she is a seamstress by trade.
Midnight Mushing also incorporates the space-age Thermo-Lite into a line of vests, which is handy not only for activities like running the dogs in extreme cold, but for sedentary activities, like sewing, where the body has the tendency to lose heat.
The Bowers are not the only people who have bought this space-age material from AFMInc; many have realized its potential and then wanted it for their own unique use. What is remarkable, though, is the extent to which this space technology can be applied and that it has worked its way into such remote locations.
In October 2005, an earthquake registering 7.6 on the Richter scale caused widespread destruction in northern Pakistan, as well as in Afghanistan and northern India. The following day, the area felt 147 aftershocks, the strongest of which registered 6.2. During the first 4 days after the initial quake, 28 aftershocks occurred with a magnitude greater than 5. Even 11 days later, there were still major quakes.
It is estimated that over 79,000 people died, 135,000 people were injured, and 400,000 houses were destroyed—a true natural disaster. The area was devastated, and the aid started pouring in to assist in relief efforts.
Stateside, Richard Berger, an avid hiker, was so moved by the plight of the people in the remote villages of Pakistan that he literally got into his car and started a search for products that might help relieve their suffering. He found his way to a large REI (Recreational Equipment, Inc.) retail store in his hometown of Seattle. REI is a supplier of specialty outdoor gear and equipment. There, Berger sorted through as many products as he could and settled on the Heatsheets rescue blanket AFMInc and Adventure Medical Kits had created. It is a larger version of the finish line blanket. At finish lines, where tripping hazards are a problem, the blankets measure 48 by 72 inches. These emergency blankets, though, are big enough for two people to wrap up and share body heat. They measure 60 by 96 inches, and the retail version is printed with a complete set of illustrated survival instructions in two languages.
Berger, like the Bowers, worked his way from the supplier to the distributor, to the manufacturer, and eventually to Deigan, asking what AFMInc could do to help. With the cooperation of a network of small companies, and a remarkable Internet fundraising effort through friends and acquaintances, Berger began to generate a buzz. The efforts were successful, and the newly formed collective received e-mails and letters from nurseries and day schools, from various nonprofit organizations, and from individuals willing to assist the refugees of the Pakistani earthquake.
Through this fundraising campaign, they produced approximately 150,000 60- by 90-inch Heatsheets out of a special performance resin polyethylene with the standard infrared-reflective coating. All of the work was done at cost, with no profit, and they went through two production runs to produce enough Heatsheets to reach as many people as possible.
Once the campaign had grown quite sizeable, Berger contacted Mercy Corps, of Portland, Oregon, to assist in the final, but most critical, stage—distributing the materials. Mercy Corps has a 25-year history of disaster relief response around the world and had already been conducting aid work in Pakistan for over 20 years. It was integral to the earthquake response and the ideal group to manage the next stages of the effort.
The group supplied both folded Heatsheets and Heatsheets-on-a-Roll for this effort, and suggested ways to employ Heatsheets as structural insulation and as emergency blankets. AFMInc also donated thousands of smaller Thermo-Lite blankets that were tremendously helpful, especially for smaller children and the elderly. These doubled as ground covers during the day and much-needed blankets at night.
Dan McHugh, a senior vice president at DHL International, Ltd., assisted the group by arranging for the large shipping firm to provide air shipments of the relief supplies at no charge, on three separate occasions. This generosity made it possible to nearly double the amount of Heatsheets supplied and provided some relief to people halfway around the world.
Both the Heatsheets and Thermo-Lite have been named Certified Space Technologies by the Space Foundation. The Space Foundation, in cooperation with NASA, created the Space Certification Program to promote the extraordinary products and services that bring the benefits of space technologyto Earth and enhance public interest and awareness in space.
Heatsheets® is a registered trademark of AFMInc.
DuPont® is a registered trademark of E. I. du Pont de Nemours and Company.
Supplex® and Cordura® are registered trademarks of INVISTA, Inc.
Thermo-Lite® is a registered trademark of Encompass Group, LLC.

Runners winding down after the 2005 Boston Marathon. When they stop running, body temperatures drop rapidly. The reflective blankets, which have become standard at marathons worldwide, help stabilize body temperatures.

AFMInc supplied the Marine Corps Marathon with 24,000 camouflage printed Heatsheets for the 2005 run

At the Tolovana Roadhouse in Alaska, 50 miles from the nearest road, Doug and Becky Bowers live with their 25 sled dogs and operate their small company, Midnight Mushing Outdoor Gear, via solar electricity.

All of the items in the Midnight Mushing catalog are handmade, and several contain an advanced variation of the infrared-reflective material used by NASA to control temperatures on spacecraft and equipment.
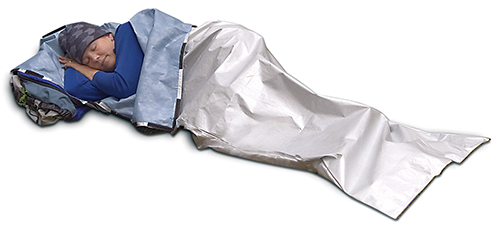
The Emergency Sleeping Bag by Adventure Medical Kits weighs only 2.5 ounces and reflects up to 90 percent of a person’s body heat, making it ideal for survival situations.

Mercy Corps coordinated with individuals and institutions, large and small, to deploy tens of thousands of the reflective emergency blankets to Pakistan in fall of 2005, after earthquakes devastated the region.
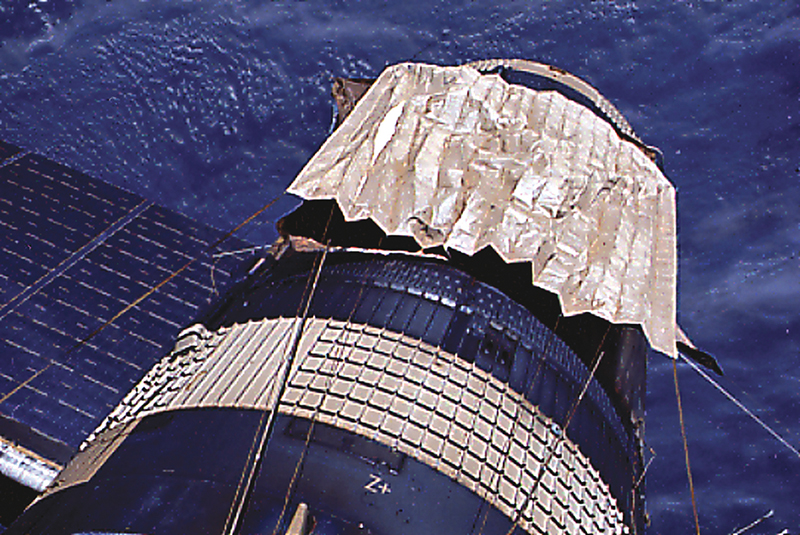
During the first days Skylab was in space, the station was besieged by problems caused when the meteoroid shield that was designed to protect it from micro-meteorites and the Sun’s intense heat tore off during launch. Scientists, engineers, astronauts, and management personnel at Marshall Space Flight Center and elsewhere worked to devise the means for its rescue. Their solution was to deploy a reflective parasol-like sunshield. Concern over the possibility that the parasol would deteriorate with prolonged exposure to the Sun’s rays prompted the installation of a second sunshield (pictured here) during the Skylab-3 mission.