
Software Performs Complex Design Analysis
Originating Technology/NASA Contribution
Designers use computational fluid dynamics (CFD) to gain greater understanding of the fluid flow phenomena involved in components being designed. They also use finite element analysis (FEA) as a tool to help gain greater understanding of the structural response of components to loads, stresses and strains, and the prediction of failure modes.
Automated CFD and FEA engineering design has centered on shape optimization, which has been hindered by two major problems: 1) inadequate shape parameterization algorithms, and 2) inadequate algorithms for CFD and FEA grid modification.
Working with software engineers at Stennis Space Center, a NASA commercial partner, Optimal Solutions Software LLC, was able to utilize its revolutionary, one-of-a-kind arbitrary shape deformation (ASD) capability—a major advancement in solving these two aforementioned problems—to optimize the shapes of complex pipe components that transport highly sensitive fluids.
The ASD technology solves the problem of inadequate shape parameterization algorithms by allowing the CFD designers to freely create their own shape parameters, therefore eliminating the restriction of only being able to use the computer-aided design (CAD) parameters.
The problem of inadequate algorithms for CFD grid modification is solved by the fact that the new software performs a smooth volumetric deformation. This eliminates the extremely costly process of having to remesh the grid for every shape change desired. The program can perform a design change in a markedly reduced amount of time, a process that would traditionally involve the designer returning to the CAD model to reshape and then remesh the shapes, something that has been known to take hours, days—even weeks or months—depending upon the size of the model.
Partnership
Optimal Solutions Software (OSS) LLC, of Provo, Utah, and Idaho Falls, Idaho, creates highly innovative engineering design improvement products to enable engineers to more reliably, creatively, and economically design new products in high-value markets.
The company entered into a Small Business Innovation Research (SBIR) contract with Stennis, under which it extensively used its ASD software to improve pressure loss, velocity, and flow quality in the pipes utilized by NASA. The product is available under the trade name Sculptor.
Because of the funding from the SBIR program and the technical contributions from its NASA counterparts, OSS was able to take the technological know-how and commercial successes gained from this project and effectively commence the next-phase step into the marketplace.
According to Mark Landon, OSS’s president, “We thoroughly enjoyed working with the engineers and scientists at Stennis—they were technically very sound and extremely helpful in every aspect of the success of the project. Additionally, with the technical and funding assistance from this program, OSS was able to create new jobs, our revenue figures and sales have increased, and private investors are looking at us at this time to take us to the next stage on our road to commercialization.”
Implementing Sculptor’s ASD technology and optimizer during the Stennis SBIR Phase II test case, OSS demonstrated a steady-state optimized resistance temperature device (RTD), which produced a smaller and more symmetrical wake, resulting in a lower drag coefficient, thus a lower moment at the base of the RTD. Remarkably, because of the aerodynamic drag reduction from the shape optimization, there was a 60 percent reduction in moment at the base of the RTD probe.
NASA applications for Sculptor include the design of spacecraft shapes; aircraft shapes; propulsion devices (nozzles, combustion chambers, etc.); pumps; valves; fittings; and other components.
With the assistance from programs such as the SBIR program, the company continues to expand its product family and add features so that its customers can create breakthrough designs and realize increased efficiency gains.
Product Outcome
Sculptor can be applied to almost any fluid dynamics problem, structural analysis problem, acoustics design, electromagnetic design, or any area where the designer needs to be able to address complex design analysis. The program performs smooth volumetric deformation and can institute design changes in seconds.
OSS has sold a license for Sculptor to Eglin Air Force Base for the design of unmanned aircraft drones and miniature aircraft. The company has also sold a license for the software to the U.S. Navy for use with Combustion Research and Flow Technology Inc., the author of the CRUNCH CFD code, a multi-element, unstructured flow solver for viscous, real gas systems, currently in use for cavitation modeling, turbo machinery applications, and large eddy simulation.
OSS has also teamed with Engineous Software Inc., the author of the iSIGHT optimization software, to subcontract on a Phase I SBIR with Wright-Patterson Air Force Base to use Sculptor to provide the shape deformation and shape matching for fluid structure interaction solutions. Wright-Patterson has also purchased a Sculptor license for application to aircraft shape design.
Since Sculptor can be utilized in any instance where there is fluid (gas or liquid) flowing in, around, or through an object, the applications are nearly countless.
Automotive shapes and parts such as aerodynamics of the body itself, mirrors, internal flow components such as intake manifolds, radiators, exhaust manifolds, cylinders, and air conditioning ducts all benefit from this program.
The motor sports industry is currently a big customer, with many racing teams finding a competitive edge by using Sculptor to reduce drag, improve down forces, improve engine design, and perform other design analyses, such as for brake cooling, basic flow handling, and internal combustion components.
Other sports are showing a deep interest in the Sculptor technology for such activities as golf club design, swimming and boating aerodynamics—even model airplane flight efficiencies.
Also showing great promise for using these tools are other industries such as biomedicine, which can utilize its ability to more quickly predict the effect of shape (anatomical) changes in the body’s vascular and other bodily systems.
To expand its domestic and worldwide presence, OSS has established a powerful distribution network, which covers North America, all of the European Union, Japan, South Korea, and China.
Sculptor™ is a trademark of Optimal Solutions Software LLC.
Crunch CFD® is a registered trademark of Combustion Research and Flow Technology Inc.
iSIGHT™ is a trademark of Engineous Software Inc.
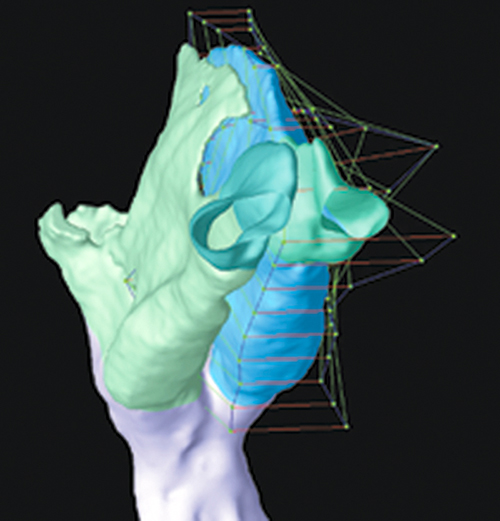
With traditional design software, reshaping an object can be a very tedious job, requiring point-by-point adjustment of hundreds or thousands of grid points. Sculptor makes this process simple and intuitive.

CFD shows pressure and streamlines along the body of this Aston Martin DBR9 GT series racecar.

Computational fluid dynamics (CFD) is proving an effective method for testing racecars—replacing, in some instances, the traditional track and wind tunnel tests.