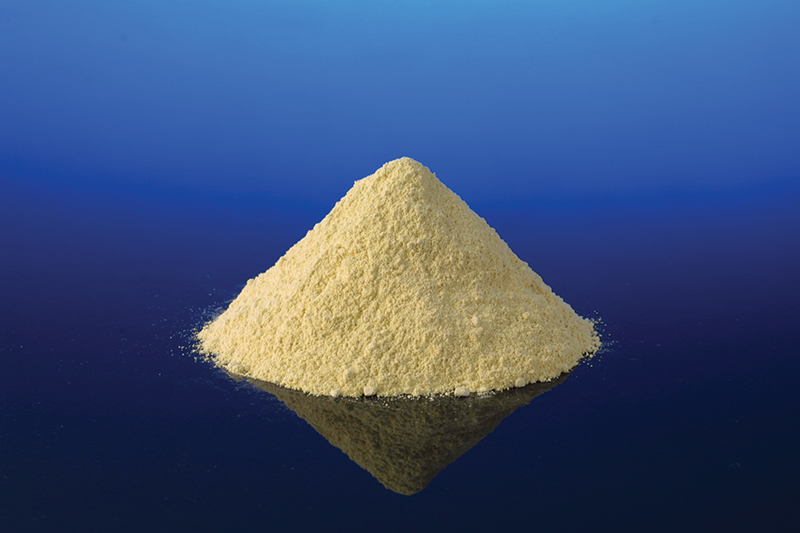
Nontoxic Resins Advance Aerospace Manufacturing
Originating Technology/NASA Contribution
In the late 1980s, scientists and engineers at Langley Research Center began to develop technology for future commercial supersonic air travel, which could reduce travel time across the Pacific or Atlantic Ocean to less than half the time possible with modern subsonic jets. Although British Airways and Air France offered high-speed travel across the Atlantic on the Aérospatiale-BAC Concorde aircraft at speeds of about 1,350 miles per hour (Mach 2.05, or 2.05 times the speed of sound, depending on altitude), NASA hoped to develop quieter, more fuel-efficient, faster supersonic jets that would travel at Mach 2.4 and carry up to 300 passengers, 3 times the number on Concorde. Supported by a team of U.S. aerospace companies, the Agency’s High-Speed Research (HSR) program began to explore the possibility of making these supersonic passenger jets a reality.
For the new jets, the HSR program needed a structural material with higher temperature capability than Concorde’s aluminum alloy, which would not tolerate the aerodynamic heating at higher altitudes at sustained speeds above Mach 2.2. Because wind friction can cause the outer surface of an aircraft to reach a temperature of 177 °C (350 °F) at Mach 2.4, the HSR team investigated new materials that retained their mechanical integrity at 177 °C for 60,000 hours—the anticipated service life of a commercial supersonic aircraft.
Partnership
Chemicals manufacturer Ube Industries Ltd., based in Ube City, Japan, has its North American headquarters, Ube America Inc., in New York. At the same time that Ube was seeking applications for a unique monomer (a small molecule that can be used as a building block for advanced high-performance polymers), Langley scientists Dr. John Connell, Paul Hergenrother (now retired), and Dr. Joseph G. Smith, Jr. were investigating these chemical building blocks that could impart specific physical, thermal, and mechanical properties into high-temperature polymers for the HSR program. Ultimately, NASA was seeking a partner in private industry that could provide materials and manufacturing capability for a high-temperature resin that met the property requirements for structural applications on supersonic aircraft. A colleague from the Japanese Aerospace Exploration Agency (JAXA), Dr. Rikio Yokota, introduced the two teams, and they formed an informal collaboration in which Ube provided a unique monomer to the Langley researchers for chemical evaluation. “We used Ube’s monomer to prepare over 50 resin formulations, measured properties, and honed in on the best performing material,” says Connell.
The monomer was a byproduct from the synthesis of another chemical used in the microelectronics industry. However, Connell explains, “This unique monomer was difficult and expensive to synthesize directly, so we collaborated with Ube to obtain the monomer and to investigate the effect of this monomer on polyimide matrix resins.” Although the HSR program was phased out in 1999, the Agency continued development with Connell’s team at Langley, who recognized that this material might fill a need in aerospace manufacturing for a high-temperature resin that could be easily processed.
Connell also credits Dr. Jim Criss, Jr., of M&P Technologies Inc., a small company in Marietta, Georgia, for refining the resin infusion (RI) and resin transfer molding (RTM) manufacturing processes for use with this high-temperature resin system. RTM is a standard process in aerospace manufacturing, traditionally for lower-temperature resin systems, such as epoxies. “As we were developing the resin system, he was developing the equipment and process for RTM, which at the time did not exist for high-temperature resins,” says Connell.
This polyimide matrix resin was named PETI-330, for its phenylethynyl-terminated imide and glass transition temperature of 330 °C. PETI-330 met the team’s requirements for a substance that performed well at high temperatures and had the unique capability to be processed into composites by RTM and RI processes.
Langley issued Ube America a non-exclusive license in 2004 for the manufacture of PETI-330, and according to Stewart Bain, product director of aerospace materials at Ube, the license was strategic for the company, which wanted to have a larger aerospace role for its specialty and chemicals division.
Based on the sales to date and the potential of PETI-330, NASA awarded the Langley team the “Commercial Invention of the Year” award for 2008. Connell believes the NASA award will help with the ongoing transfer to the commercial marketplace: “Ideally it will provide more visibility for the material and help further its progression into aerospace-related products.”
Product Outcome
The aerospace industry fabricates composites through non-autoclave techniques such as RTM, RI, vacuum-assisted RTM, and conventional autoclave processes using pre-impregnated material (prepreg). PETI-330 is the first resin created specifically for high-temperature composites formed with RTM and RI. Offering processability, toughness, and high-temperature performance, the resin has a low-melt viscosity and, when cured, a high glass transition temperature. These properties typically oppose each other, but are both highly desirable in manufacturing.
Bain explains that the composite manufacturing process is far simpler and faster using PETI-330 than competing materials because Ube’s resin only requires a one-step curing process. “The resin is heated to 288 °C and then de-gassed,” he explains. “Then it is injected into a mold, the temperature is increased to 371 °C, and left for an hour and subsequently cooled. You then have your part.” Curing cycles for other resins can have as many as 15 steps, Bain explains, and can take 24 hours. Because PETI-330 has low-melt viscosity, it is able to penetrate large area carbon fiber molds (preforms) without changing flow characteristics—an important characteristic for resins during this process. Connell says, “The low-melt viscosity gives us that advantage in the processing.” Machining of the composite is also possible after molding, thus enabling the precise manufacture of a variety of shapes and sizes.
Another advantage PETI-330 offers, Bain says, is strength with a lower weight than metal alloys, which enables the resin to replace them—particularly titanium alloys—in many components. Consequently, the resin can reduce the weight of high-temperature parts. Because of its strength and toughness, the cured resin (and composites) also resists microcracks that often result from frequent expansions and contractions with temperature fluctuations. Bain explains that when heat is combined with humidity in extended operation, a part tends to degrade much more quickly, but PETI-330 tends to maintain its strength even in these conditions. This can make PETI-330 especially useful for aerospace applications, where components must be both lightweight and resistant to cracks and damage from temperature swings.
One important feature of the PETI-330 that Connell and Bain are particularly proud of is its safety. Whereas traditional approaches use toxic monomers, the new resin is “completely nontoxic,” says Bain. Other high-temperature resin matrix composites, he says, contain unreacted aromatic diamines, such as 4,4’-diaminodiphenylmethane (called MDA), many of which are carcinogenic and require special handling and dedicated facilities to protect workers. He says, “PETI-330 is guaranteed not to contain unreacted aromatic diamines, which is an important feature when you consider the health of the workers who are handling the material.” The diamines used in PETI-330 are fully reacted into the resin, Connell says. Consequently, it is stable and has a long shelf life. Neither specialized protective equipment nor dedicated facilities are required for PETI-330, which can help reduce costs.
Because of the resin’s high-temperature performance and processability, Connell says, the NASA resin is well suited for use in and around jet engines (including inlet frames, insulation, nacelles, air ducts, and compressor vanes) where temperatures may reach 260–288 °C (500–550 °F) and remain at high temperatures for thousands of hours. Recently, Ube began collaborating with Boeing Aerospace for high-temperature applications on commercial aircraft. The resin is also under evaluation by a number of other aerospace companies for applications that may take advantage of PETI-330’s unique qualities.
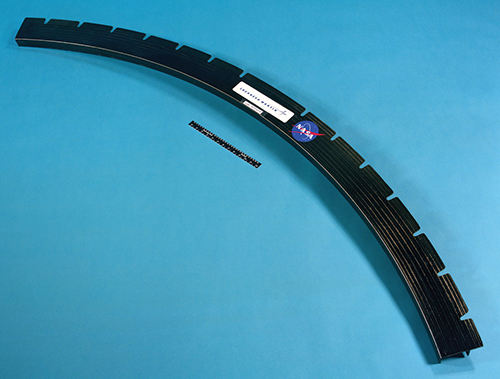
PETI-330 was used in resin transfer molding to fabricate this F-frame. Composite manufacturing is simpler and faster with PETI-330, because it needs only a one-step curing process.
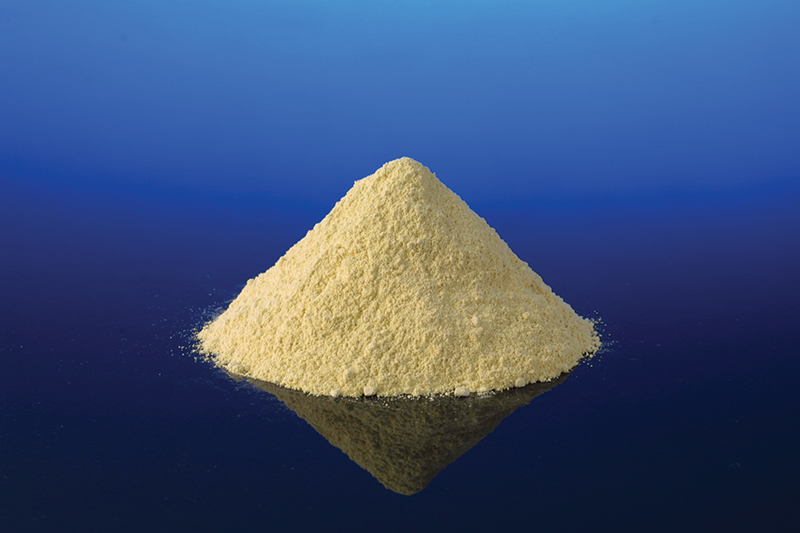
PETI-330 is the first resin created specifically for high-temperature composites formed with resin transfer molding and resin infusion. Offering processability, toughness, and high-temperature performance, the resin has a low-melt viscosity and, when cured, a high glass transition temperature.