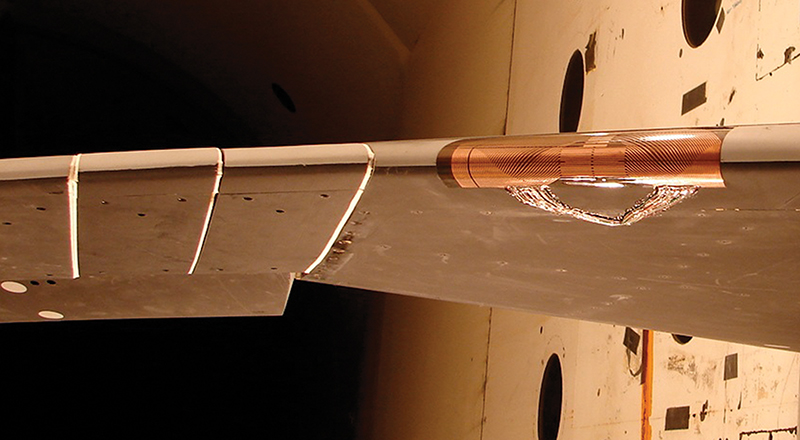
Sensor Systems Collect Critical Aerodynamics Data
Originating Technology/NASA Contribution
The next time you blow out a candle, watch how the smoke behaves. You will see that it rises first in an even stream. At a certain point, that stream begins to break up into swirls and eddies as the smoke disperses.
Air flowing over a wing demonstrates similar behavior. The smooth, even movement of air over a wing is called laminar flow and is what allows aircraft to fly efficiently. Airflow that separates from the wing’s surface and breaks up into unsteady vortices is called turbulence, which is responsible not only for those moments of bumpy discomfort during flights but also increased drag, which reduces efficiency and performance. Understanding and controlling the influence of these aerodynamic forces on a wing can lead to aircraft that fly more safely, use less fuel, and carry greater payloads.
In 1981, aerodynamics researcher Siva Mangalam joined NASA’s Langley Research Center to work with Werner Pfenninger, a renowned expert in the field of laminar flow control. Mangalam collaborated with Pfenninger on designing a series of unmanned aerial vehicle (UAV) airfoils, one of which has since been incorporated into the Global Hawk UAV, which this year began a series of NASA scientific missions. Through the course of his design work, Mangalam became interested in a basic deficiency in aerodynamics research: While there were extensive systems for wind tunnel testing, there were no quantifiable sensing systems for measuring aerodynamic forces and moments during actual flight.
Mangalam explains that, when an aircraft is in flight, there are three sets of forces in play apart from propulsion: aerodynamics, structural oscillations of the airframe, and forces created by actuators like flaps or tail surfaces. Currently, Mangalam says, the impact of aerodynamic forces on an aircraft is understood only after the fact; turbulence, for example, is only detected after the aircraft’s structure responds to it.
“Today we measure the impact of aerodynamic forces primarily through structural measurement devices such as accelerometers, gyroscopes, and strain gauges. We need sensing systems to measure aerodynamics independently of structures and actuation,” says Mangalam. An aircraft’s wings, for example, act like low-pass filters: They do not respond quickly enough to aerodynamic disturbances like turbulence to allow structural sensors to capture what the forces are doing in real time.
“Turbulence can be very fast acting, while the structure is slow acting,” Mangalam says. This means that not only do researchers not know the true aerodynamic conditions influencing an aircraft in flight, but neither do pilots. Without an exact knowledge of the unsteady forces in play, a pilot negotiating sudden turbulence might do the opposite of what is required, Mangalam says. The ability to detect changes in aerodynamic forces before the aircraft’s structure responds can lead to better control systems and safer, more efficient, and more comfortable flight.
Partnership
In 1994, Mangalam founded Tao of Systems Integration Inc. (Tao Systems), headquartered in Hampton, Virginia, to develop real-time systems to quantify aerodynamic and structural dynamics for monitoring and improving aircraft performance and safety. With the support of multiple Small Business Innovation Research (SBIR) contracts and flight testing opportunities with Dryden Flight Research Center, Tao Systems began crafting sensors and other components with the ultimate goal of developing a first-of-its-kind, closed-loop system to detect, measure, and control aerodynamic forces and moments in flight.
Tao Systems’ approach to gathering aerodynamic data is based on a “game-changing concept,” Mangalam says. Essential aerodynamic information such as lift and drag, he explains, can be estimated with measurements at two locations: where the airflow attaches to and detaches from the aircraft surface.
The system works based on a kind of reverse windchill factor. By maintaining a constant temperature on an airplane wing, Mangalam says, “we can determine how much heat loss is caused by the airflow. Depending on how much heat is taken, and its distribution, we can capture the critical points.”
This simple, inexpensive approach allows the real-time collection of aerodynamic data free of in-flight interferences like electromagnetic or radio frequency interference—a previous barrier to exposed sensors for accurate in-flight aerodynamic measurements.
Product Outcome
Today, Tao Systems has developed three of the four planned components for its closed-loop system. The final component, a controller, is scheduled for completion by 2012. In the meantime, the company’s completed components—its SenFlex hot-film sensors, hot-wire and hot-film constant voltage anemometers, and its proprietary signal processing techniques—are providing sensing solutions for a host of research and development applications.
Customers such as Boeing, Lockheed Martin, Northrop Grumman, General Electric, BMW, and Rolls Royce have employed SenFlex sensors for the nonintrusive measurement of airflow and temperature characteristics. Sandia National Laboratories are using the company’s technologies to explore ways of improving wind turbine operation.
“Whenever there is a tremendous amount of power available from high winds, these turbines have to shut down because they cannot handle the load,” says Mangalam. “If they could have some way of measuring and controlling the loads generated by the gusting winds, the turbines could generate more power and last longer.”
Tao Systems’ technologies are also employed for examining airflow in buildings to determine ways to save energy by optimizing air conditioning use.
“Wherever there is airflow, the opportunities are plenty,” says Mangalam. But he is quick to note the usefulness of his company’s technologies underwater as well, for developing and improving underwater turbines generating electricity from waves and tidal forces. Using its SBIR-developed components, Tao Systems is also working with the U.S. Navy to create a control system for an underwater propeller blade that can alter its shape to maintain high performance in a range of hydrodynamic conditions.
While Tao Systems’ customers continue to make use of its innovations, the company has its eye on the potential benefits its completed closed-loop flight control system will offer. Mangalam says that once the system is available, engineers will be able to use it to develop advanced adaptive control systems and flexible wing structures, allowing an aircraft to respond to—and even take advantage of—aerodynamic conditions as they happen, improving flight safety and comfort, increasing fuel efficiency and payload capacity, and extending aircraft lifespan by reducing structural strain and fatigue. Advancements like this would provide human aviation with capabilities closer to those of nature’s perfect aerodynamic creation.
“We could fly by feel,” he says, “like a bird.”
SenFlex® is a registered trademark of Tao of Systems Integration Inc.
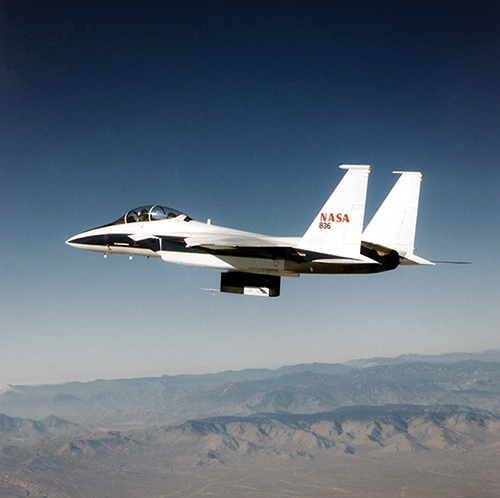
Dryden Flight Research Center’s F-15B test bed aircraft flew several flights to determine the location of sonic shockwave development as air passes over an airfoil.
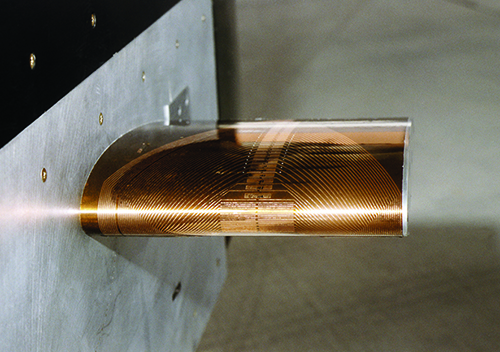
The shock location sensor developed by Tao of Systems Integration Inc., isolated the location of the shock wave to within a half-inch.
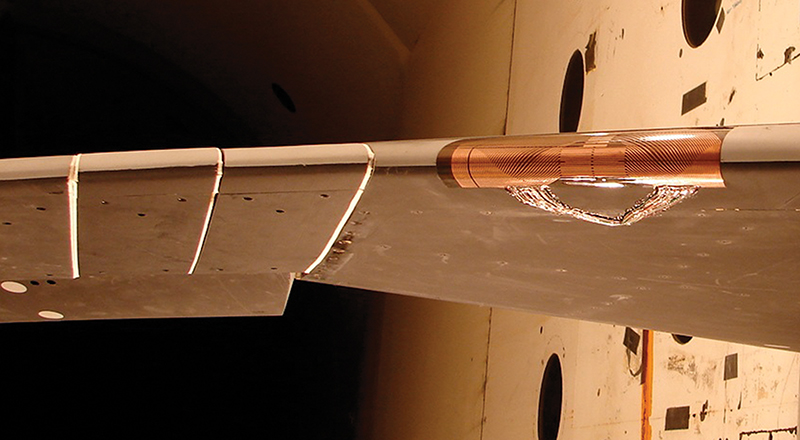
The Tao Systems sensor array, seen here on the leading edge of a Northrop Grumman SensorCraft flexible wing model, was used to successfully demonstrate gust load alleviation. Tao Systems’ sensors could one day enable flexible wing aircraft that respond in real time to aerodynamic conditions, resulting in bird-like flight.