Secure Future
In the business of space construction, the phrase, "some assembly required" is commonly heard, just as it is here on Earth. But there is a big difference. Suited up in heavy pressurized space suits and outfitted with bulky gloves, astronauts have a tougher job in completing work tasks.
Specifically built to Johnson Space Center requirements, Thread Technology, Inc. of Sterling, Virginia, developed the ZipNut®, replete with Push-on Threads®. As the name suggests, this fastener can be pushed on, rather than turned. Originally developed for the Space Shuttle and space station programs, the product is now in use by firefighters, nuclear powerplant repair technicians, and others involved in difficult assembly duties. These quick-connect fasteners enjoy the flexibility and strength of threads while eliminating their heretofore inherent weaknesses of slowness and cross-threading.
NASA has adopted the ZipNut fastener for space walking and robotic in-space assembly. A tool to apply the fastener was first developed for flight aboard a Space Shuttle in 1989. It was also adopted for the Space Station in 1992. The attachment technology has been a part of two Hubble Space Telescope repair and servicing missions, in 1994 and 1997. Zipping on and zipping off attachment handrails to move delicate Hubble instruments about the Shuttle's cargo bay were made possible by using the exceptional fasteners.
Once segments of the International Space Station are orbited, astronaut "hard hats" will be faced with piecing together the various elements. Thread Technology is supplying ZipNuts to help assure fast and easy connection of Space Station hardware. Installation time can be improved since bolts can be pushed into place rather than having to be turned like conventional nut/bolt combinations.
There are several benefits and features of Thread Technology fasteners, also making them ideal for more down-to-Earth applications. Coupling to an existing threaded part can be done with only a push and twist of up to one full turn. Wrench tightening is obsolete. Rapid assembly is possible without the need of starting the thread lead or rotating the male and female parts multiple times.
A patented optional feature of the ZipNut allows quick removal of fasteners and connections. A locking system prevents accidental disconnection under load. For many markets, such as industrial gas filling, this feature reduces repetitive hand motion problems and virtually doubles the product benefit without doubling the cost.
The Push-on Thread fastener also resists movement under vibration. Adverse environmental conditions do not degrade product performance, whether exposed to outer space, contamination, or extreme weather. Lastly, the product can be fabricated from most materials, such as stainless steel, aluminum, titanium, brass, and even plastic. There is no material limitation so long as the material has sufficient strength to bear the specified loads. A fastener can be designed in a wide range of sizes, such as the one-quarter-inch nut developed for NASA or a six-inch high pressure water coupling.
ZipNuts can be found in numbers of settings: Industrial and medical compressed gas connections; hydrant and water hose fittings; for extracting a person from a crashed auto, building collapse, cave-in or construction accident; and in radioactive areas where speed of attachment and removal of threaded items are a must. Other potential product markets include automotive assembly and operation such as lugnuts, coaxial and pin connections for electronic equipment, injection-molded plastic parts for mass assembly, and in high pressure fluids for fire or dealing with hazardous materials.
Thread Technology envisions ever wider use of the ZipNut in future years, not only in space but for Earthbound, in-the-home chores, too. It will be a "fasten"-ating future, no doubt!
®ZipNut is a registered trademark of Thread Technology, Inc..
®Push-on Threads is a registered trademark of Thread Technology, Inc..
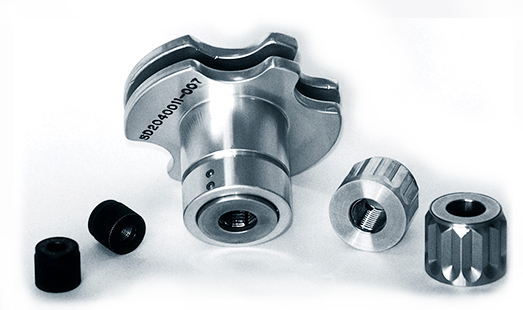
ZipNut® fasteners are unique in that they push on rather than turn. NASA has adopted this technology for space walking and robotic in-space assembly.