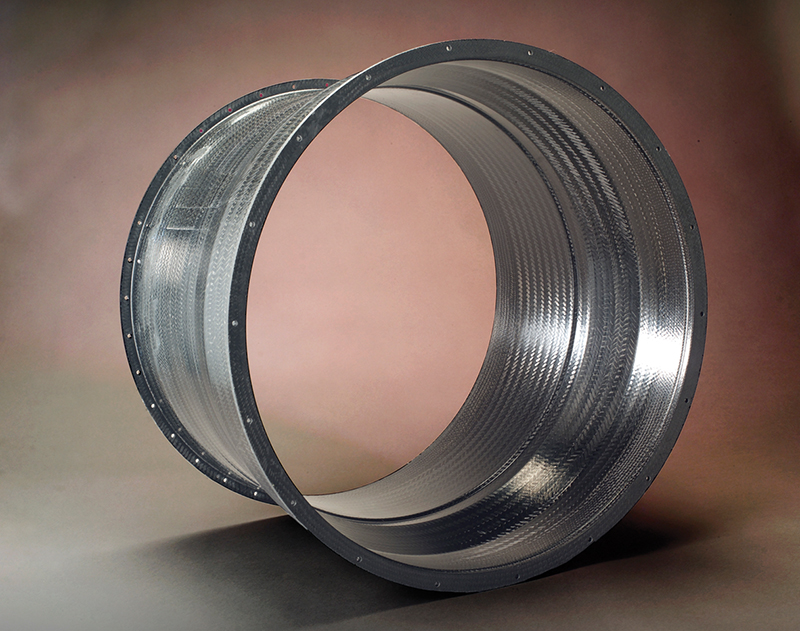
Damage-Tolerant Fan Casings for Jet Engines
Originating Technology/NASA Contribution
All turbofan engines work on the same principle. A large fan at the front of the engine draws air in. A portion of the air enters the compressor, but a greater portion passes on the outside of the engine—this is called bypass air. The air that enters the compressor then passes through several stages of rotating fan blades that compress the air more, and then it passes into the combustor. In the combustor, fuel is injected into the airstream, and the fuel-air mixture is ignited. The hot gasses produced expand rapidly to the rear, and the engine reacts by moving forward.
If there is a flaw in the system, such as an unexpected obstruction, the fan blade can break, spin off, and harm other engine components. Fan casings, therefore, need to be strong enough to contain errant blades and damage-tolerant to withstand the punishment of a loose blade-turned-projectile.
NASA has spearheaded research into improving jet engine fan casings, ultimately discovering a cost-effective approach to manufacturing damage-tolerant fan cases that also boast significant weight reduction. In an aircraft, weight reduction translates directly into fuel burn savings, increased payload, and greater aircraft range.
This technology increases safety and structural integrity; is an attractive, viable option for engine manufacturers, because of the low-cost manufacturing; and it is a practical alternative for customers, as it has the added cost saving benefits of the weight reduction.
Partnership
A&P Technology, Inc., of Cincinnati, a leading manufacturer of braided fabrics for composite reinforcement and advanced technology applications, received a Small Business Innovation Research (SBIR) grant through Glenn Research Center to develop damage-tolerant fan casings for jet engines. Additional collaborators on this project included the Federal Aviation Administration, Ohio State University, and the University of Akron, Ohio. This group effort enabled the rapid development and fabrication of the prototype composite fan cases for direct comparison to the metal fan cases currently used in aircraft engines.
The prototypes proved feasible. A&P, a seventh-generation, family-owned company is partnered with two major manufacturers of jet aircraft engines—Williams International and Honeywell International Inc.—and is sponsored by General Electric Corporation’s Aviation division, GE Aviation, in the development and production of these braided composite fan cases.
For the successful work on this SBIR, A&P received the “Emerging Technology Award” from the Ohio Department of Development. The work also contributed to Glenn’s Jet Engine Containment Concepts and Blade-Out Simulation Team receiving the NASA “Turning Goals into Reality” award.
Product Outcome
A&P uses triaxial carbon braid as an alternative to aluminum or other solid metal in the manufacture of braided fan containment cases for jet engines. The braided fan case has a toughness superior to aluminum and enables significant reductions in weight and fuel consumption.
The use of braided reinforcements also allows for a low-cost, repeatable manufacturing process. A&P produces a braided sleeve with a custom shape that exactly fits the geometry of the fan case. Instead of having to cut complicated shapes to match the geometry of the fan case, the manufacturer can simply wrap A&P’s tailored braid circumferentially in a continuous lay-up to create the needed structural reinforcement. This cuts down significantly on manufacturing time and costs.
Not only can the efficiency of the manufacturing process increase noticeably with the braid, but the performance of the braided case exceeds the performance of conventional fan cases. Impact testing has shown that braided laminates perform better, because the failure mode is much more controlled. In impact tests, the braided laminate experiences fracturing only near the point of impact while the rest of the laminate remains intact. In contrast, a conventional laminate that fractures from an impact spreads rapidly to regions remote to the initial impact location, like the “spider web” cracking of a windshield. This extensive failure results in a fan case structure that is less able to withstand secondary loads as the fan decelerates.
A braid’s resistance to crack propagation is a result of two key features: the interwoven fibers within each layer of braid, which distribute load evenly, and the isotropic architecture offered within each individual ply. Since each ply is isotropic within itself and identical to each neighboring ply, the interlaminar stresses are minimized during response to an impact event. Upon impact, crack propagation is contained to an area substantially smaller than those found upon impact of aluminum or laminate cases.
Although braiding has been a mechanized process for over 300 years, creating everyday products like clotheslines and candlewicks, A&P has advanced the manufacturing technology to incorporate cutting-edge materials such as carbon fiber into structures of previously unthinkable scale. For instance, one fan case design it built is approximately 10 feet in diameter and 5 feet long. The braided reinforcements for this composite fan case were produced on one of A&P’s Megabraiders—an 800 carrier braiding machine—the largest braiding machine in the world.
In the case of the GEnx engine, the composite fan case A&P is making for GE Aviation, braid will reduce engine weight by 350 pounds, or 700 pounds in a two-engine aircraft. The overall weight reduction is more than 800 pounds for the aircraft, because composite materials also allow for weight avoidance in the engine installation. The weight reduction translates directly into fuel savings, increased payload and/or greater aircraft range, and those are really just secondary benefits of this technology, with the primary benefit being the added safety of a stronger fan casing.
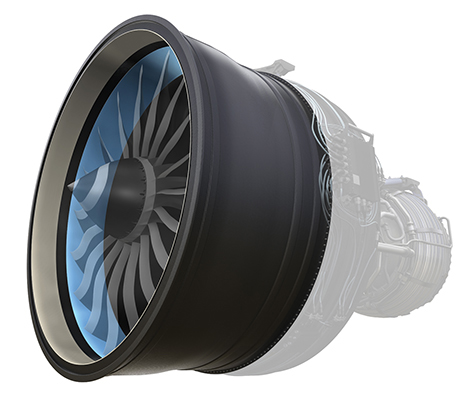
The braided composite creates a lighter, more fuel-efficient engine casing that is stronger and safer than those made with aluminum or other traditional materials.
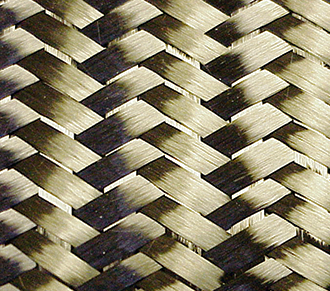
The efficient distribution of loads makes braided structures highly impact resistant. Since all of the fibers in the structure are involved in a loading event, a braid absorbs a great deal of energy as it fails, making it very effective for use in fan blade containment for commercial jet aircraft.
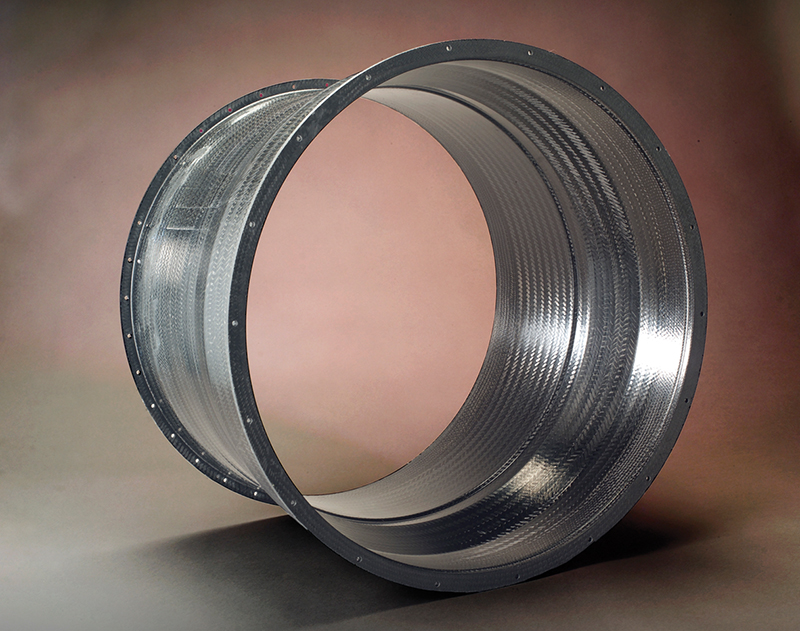
The braided fan case has a toughness superior to aluminum and enables significant reductions in weight and fuel consumption.