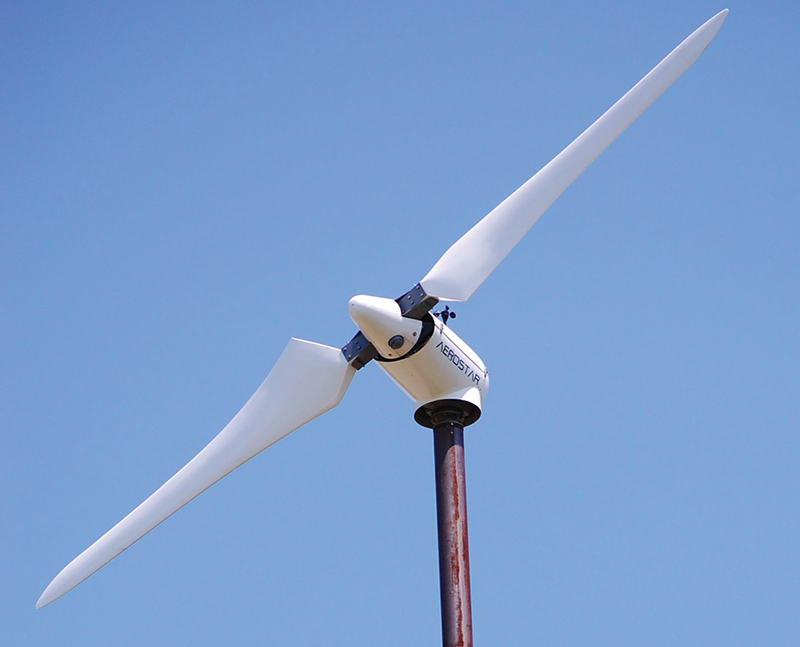
Modeling Innovations Advance Wind Energy Industry
Originating Technology/NASA Contribution
One morning in 1990, a group of Glenn Research Center (then Lewis Research Center) employees arrived to find their workspace upended by an apparent hurricane. Papers were scattered, lights blown out. All eyes turned to the door connecting the office to its neighbor: a 20-foot wind tunnel.
The employees did not know it, but they had Dr. Larry Viterna to thank for the state of their workspace. An innovation by the NASA researcher may have led to the accidental trashing of their office, but it would go on to benefit the entire field of wind energy.
Viterna joined NASA in 1977, during a time when the country was in an energy crisis. Growing anxiety over fuel costs and environmental impacts led the U.S. Government to explore alternative and renewable energy sources. In a time prior to the formation of the Department of Energy (DOE), the government turned to other agencies like NASA to develop solutions. Glenn had a history of energy research stemming from its work in fuel-efficient aeronautics during World War II and in alternative fuels and related aerospace engines at the start of the Space Age in the 1950s. When Viterna joined the Center, it had already assumed the lead role in the Nation’s wind energy program. NASA’s goal was to develop technology for harnessing the wind’s power and transfer it to private industry.
“Our center had an expertise in propellers, propulsion, rotating equipment, and power systems,” making Glenn a natural choice for the job, explains Viterna. The Center’s efforts, he says, ultimately laid the foundations for much of the wind technologies and industry that exist today.
Glenn constructed its initial experimental 100-kilowatt (kW) wind turbine at the Center’s Plum Brook Station facility in Sandusky, Ohio in 1975. The Mod-0 turbine was a two-bladed, horizontal turbine. By 1978, the 2-megawatt (MW) Mod-1, the world’s first multimegawatt wind turbine, was developed—capable of providing electricity to thousands of homes. Successive experimental models (13 in all) were built throughout the country. Viterna notes that these were also record setting in size and output; the 4-MW capability of the WTS-4 turbine, built in 1982 in Medicine Bow, Wyoming, was not surpassed for about 25 years.
“That’s how far ahead the program was in terms of developing this technology,” Viterna says.
NASA’s efforts also led to other industry innovations that are standard today. As Glenn researchers explored ways of reducing the weight and cost of turbine structures, they developed steel tube towers that replaced the rigid truss towers traditionally used. “Today, virtually every large wind turbine uses a steel, tubular tower, which was novel technology at the time,” says Viterna.
Despite the advances made by the NASA-led program, there were still significant challenges. “One of the key things then and now is to accurately predict the forces exerted on a wind turbine,” Viterna says. On a basic level, wind turbines function by the same forces that allow airplanes and helicopters to fly. Wind blowing over the turbine’s blades, or airfoils, creates lift that turns the blades, spinning a shaft that connects to an electricity-producing generator. When engineers first began to model the impact of these forces on wind turbine airfoils in high-wind conditions, they would produce results that were off by at least 50—and sometimes as much as 100—percent.
The problem was that wind turbines, unlike most other airfoil-based systems, operate at a high angle of attack—the angle formed between the chord of an airfoil and the direction of the airflow. (A chord is an imaginary line through an airfoil’s cross-section, joining the tip of the trailing edge to the center of the leading edge.) In airplanes, when the angle gets too large, the laminar air flow that typically hugs the wing begins to detach and become turbulent, reducing lift and increasing drag; at a certain point, the plane stalls and drops out of the sky. (This could theoretically happen with helicopter blades as well, but these vehicles do not operate near stall conditions.) Wind turbines, especially in high-wind conditions, can routinely stall, limiting the ability of the turbine to produce electricity. The inability to properly predict stall behavior, actual aerodynamic loads, and the relationship between wind speed and power in wind turbines led to inefficient designs and costly turbine failures. At the time, there was a significant lack of research and data in this area, Viterna explains, as well as “three-dimensional effects going on that we had no way of calculating or even measuring.”
In 1981, using data previously collected from an old Danish turbine, coupled with test data gathered by fellow NASA researcher Robert Corrigan from the Plum Brook turbine, Viterna developed a model that took into account three-dimensional effects and predicted stall behavior with far greater accuracy than previous methods.
The model was not well accepted by colleagues in the wind energy field, Viterna remembers. “I almost got laughed off the stage when I presented it,” he says, explaining that the model violated existing theories that used two-dimensional airfoil data. Viterna, however, continued to employ the model for NASA’s purposes, even using it in 1991 to improve Glenn’s Icing Research Tunnel, designed to study the effects of ice buildup on aircraft. Based on the model’s results, Viterna suggested that slightly shaving down the wood fan blades could boost the tunnel’s 299-miles-per-hour (mph) capability. During a nighttime test, the wind tunnel’s pressure release door flew open, sending 400-mph winds ripping through the adjoining work area. (The tunnel’s new upper limit after implementing Viterna’s model: 430 mph.) The surprise Viterna’s coworkers encountered the following morning was on par with what Viterna experienced during a random Internet search nearly 25 years after inventing his model.
Partnership
In 2005, long after the easing of the energy crisis and shift of the wind energy program to the DOE, Viterna, now in Glenn’s Office of Strategic Management, was searching the Internet when he began to come across multiple references to the “Viterna method” by experts in the wind energy field. He discovered his initially criticized model had, within a decade of its creation, quietly become the established method of modeling the performance of wind turbine airfoils under high angles of attack—stall conditions.
“It had become, and still is, the most widely used stall model in the United States,” says Viterna, who along with Corrigan recently received a “Space Act Award” from NASA’s Inventions and Contributions Board, as well as the Agency’s inaugural “Blue Marble Award” at its Environmental and Energy Conference.
Among the many who use the Viterna method is the DOE’s National Renewable Energy Laboratory’s National Wind Technology Center (NWTC), located in Boulder, Colorado. In 2005, the center added the Viterna model to its design-code software suite for horizontal-axis wind turbines, the most popular variety of turbines in use today.
“Viterna’s model does a very effective job of estimating stall behavior on inboard sections of the blade and how it varies along the blade’s span,” says Dr. Sandy Butterfield, wind program chief engineer at the NWTC. “Even though it was invented in the 1980s, it remains a model used by engineers predicting performance and loads for wind turbines.”
The NWTC suite—which offers design and analysis software tools for use in achieving worldwide certification of wind turbines—incorporates Viterna’s model in its FoilCheck preprocessor. FoilCheck allows users to generate airfoil tables and compute dynamic stall parameters for use in NWTC’s AeroDyn software library, which enhances the center’s YawDyn, FAST, and ADAMS turbine simulators. The entire suite is available to private industry for free, which has enabled wind turbine manufacturers like Westport, Massachusetts-based Aerostar Inc. to use Viterna’s method to help craft their products.
Product Outcome
Aerostar produces a 6-meter, 10-kW wind turbine, the design for which was developed in the 1980s by company president Paul Gay, as well as a recently added 11-meter, 30-kW model. Aerostar wind turbines are designed to provide electricity to individual homes, farms, and remote locations with limited or no connection to the power grid. As opposed to a rigidly mounted, three-blade design—the three blades commonly seen on wind turbines today are a feature imported from Denmark and Germany, which became the main technology drivers in wind energy following NASA’s major involvement—Aerostar’s turbines feature teetering, two-bladed rotors like NASA’s early models. This design helps lower the weight and cost of the structure by reducing the large, gyroscopic loads typically inflicted on the turbine and its tower.
The company’s turbines belong to a class called fixed pitch turbines. The rotors of fixed pitch turbines turn at a relatively constant speed regardless of the current wind speed. This is in contrast to variable speed turbines (a NASA-developed technology), in which the rotor speed varies with the wind speed. While variable speed turbines have the advantage of producing more power as wind speeds increase, the frequency, voltage, and current of their output also varies, requiring a line commutated inverter to make the output compatible with the power grid. Fixed pitch turbines like Aerostar’s, however, use induction motors to produce electricity. The same kind of motor used in common technologies like water pumps and air conditioners, an induction motor transforms into a generator when its shaft rotates at speeds faster than it turns as a motor. The induction generator is already in phase with the electrical current supplied by the power grid, so the cost and inefficiency of an additional inverter is unnecessary.
Because Aerostar’s turbines are of this variety, the Viterna model plays a major role in the manufacture of its products. The company employs the NWTC suite, including FoilCheck, when designing its wind turbines. Utilizing the Viterna method through this software has enabled Aerostar to create efficient, effective turbine designs, says Gay.
“The model makes it possible for manufacturers like us to predict and characterize the performance of airfoils
for these turbines,” he says. Viterna’s model is highly important to Aerostar’s turbines because, like many fixed pitch turbines, they are actually regulated by stall, the conditions Viterna’s model was the first to accurately predict for wind turbine airfoils.
A constant-speed rotor will only operate effectively in a narrow range of wind speed, Gay explains. Above that range, the airfoils go into stall, and power production tapers off. Aerostar’s turbines and many others utilize stall regulation as an automatic, passive way of managing the turbine at high wind speeds—like a built-in power governor. This eliminates the need for moving parts, which are required for blade pitching, furling, and other active power-limiting devices.
“If you can’t calculate how the rotor performs at these higher wind speeds, you might find it producing way too much power, burning out the generator,” Gay says. Being able to accurately predict stall behavior allowed for this kind of control, says Viterna.
“We were trying to simplify the design of wind turbines early on to get the market going,” Viterna says. “It was very important to get the entire industry off and running with a design capable of operating reliably in a passive control mode.” (The effort worked: Fixed pitch turbines comprised 60 percent of turbines worldwide by 1991.)
The Viterna method is finding applications beyond horizontal wind turbines; Viterna has discovered his once-mocked model is now employed for vertical wind turbines, wind tunnels, and even underwater turbines that make use of tidal energy to produce power. In the meantime, NASA continues to be involved in the advancement of wind energy; Glenn, for example, is supporting the plans of Cuyahoga County, Ohio, to establish on Lake Erie the world’s first freshwater, offshore wind turbine site.
The Agency can also expect to see its early work experience a resurgence, predicts Dr. Butterfield of the NWTC. “As the industry moves forward and becomes more competitive and broad, you will see efforts to explore lower cost, more structurally efficient machines, and that’s when people will begin to capitalize again on that good work NASA did in the early 1970s and 1980s,” he says. It seems likely that Viterna’s and NASA’s pioneering work will continue to play a significant role given the Nation’s ambitious energy goals: The DOE has outlined a plan for generating as much as 20 percent of the country’s energy from wind power by 2030.
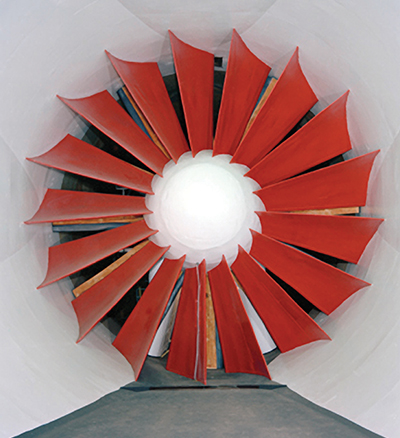
By shaving the IRT’s wooden fan blades in accordance with the results of Dr. Larry Viterna’s model, Glenn engineers boosted the tunnel’s top wind speed by over 130 miles per hour.
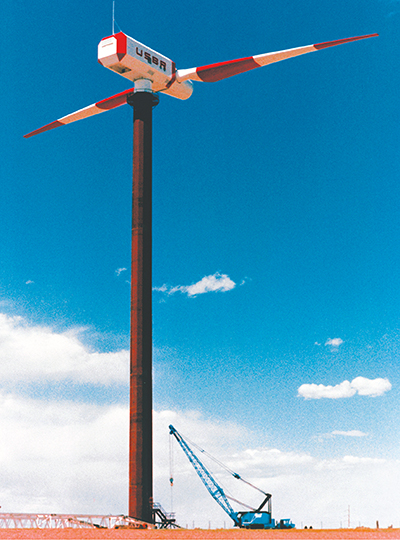
For over 20 years, NASA’s 4-megawatt WTS-4 wind turbine held the world record for maximum power output.
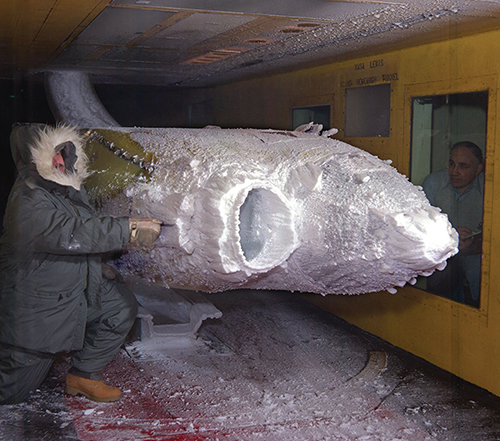
Glenn Research Center’s Icing Research Tunnel (IRT), built at the end of World War II to study aircraft icing, is one of the world’s largest refrigerated wind tunnels and currently the Center’s busiest facility.
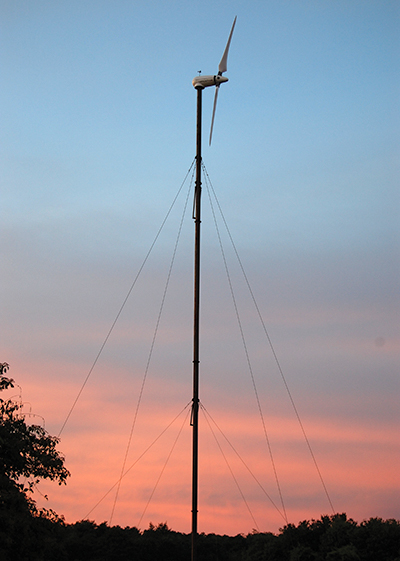
Aerostar’s wind turbines are stall regulated, a feature enabled by the Viterna model.
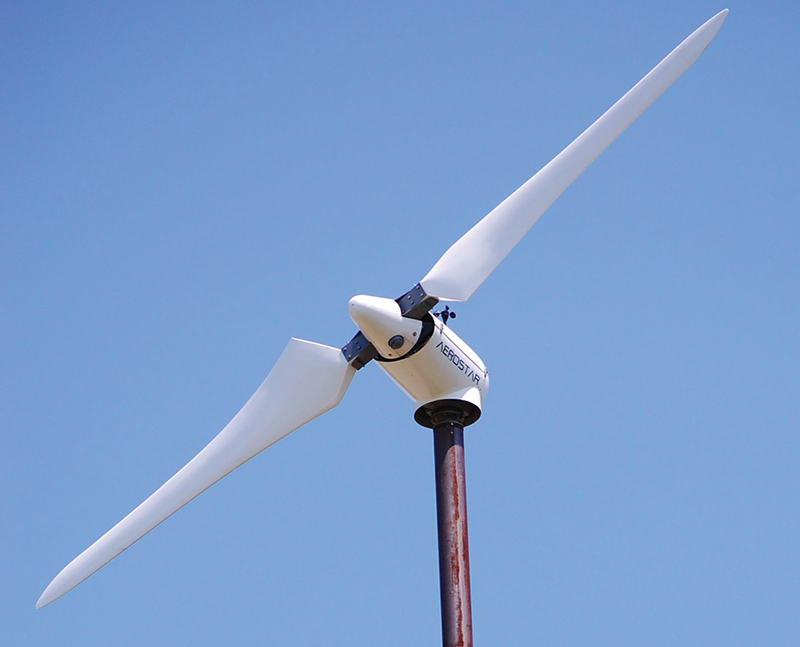
The teetering, two-bladed rotor of Aerostar’s wind turbines is similar to that of NASA’s early designs.