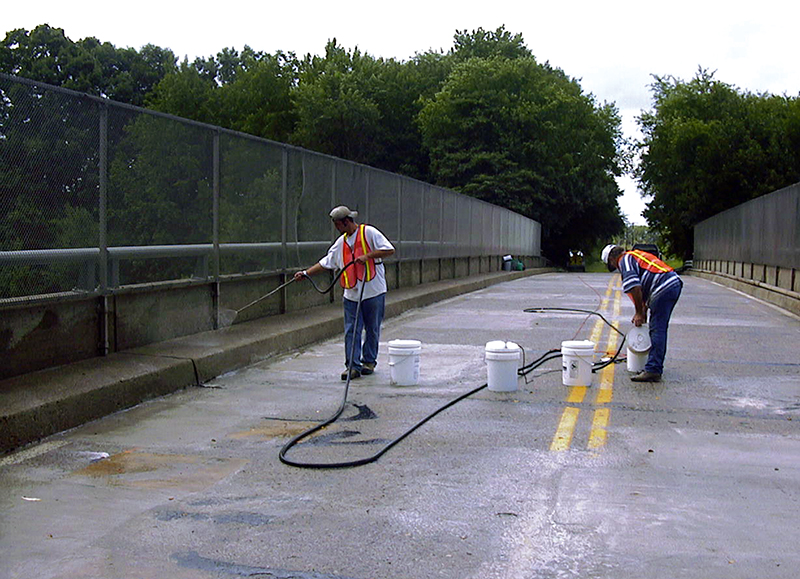
Treatment Prevents Corrosion in Steel and Concrete Structures
Originating Technology/NASA Contribution
NASA’s Kennedy Space Center is located on prime beachfront property along the Atlantic coast of Florida on Cape Canaveral. While beautiful, this region presents several challenges, like temperamental coastal weather, lightning storms, and salty, corrosive, sea breezes assaulting equipment and the Center’s launch pads. The constant barrage of salty water subjects facility structures to a type of weathering called spalling, a common form of corrosion seen in porous building materials such as brick, natural stone, tiles, and concrete. In spalling, water carries dissolved salt through the building material, where it then crystallizes near the surface as the water evaporates. As the salt crystals expand, this creates stresses which break away chips, or spall, from the surface, causing unsightly and structural damage.
The potential for corrosion heightens as concrete structures age, because over time concrete loses its acidity, or pH. When it starts out, poured concrete has a high pH value, between 11 and 13, which helps to inhibit corrosion. Over time, though, this value drops, and when the pH value dips into the 8 to 9 range, there is potential for corrosion of the steel reinforcing bars, or rebar, causing further structural concerns.
In the mid-1990s, to protect the rebar, NASA developed an electromigration technique that sends corrosion-inhibiting ions into rebar to prevent rust, corrosion, and separation from the surrounding concrete. An ounce of prevention is worth a pound of cure, and with the help of Florida’s Technological Research and Development Authority, an independent state agency that partnered with Kennedy on technology transfer initiatives, the Center began working with Surtreat Holding LLC, of Pittsburgh, Pennsylvania, a company that had developed a chemical option to fight structural corrosion in 1997. Surtreat’s method was to apply its anti-corrosive solution product, TPS-II, to the surface of a corroding concrete slab, where it would then seep through to the rebar, coating it and preventing further corrosion.
Combining Surtreat’s TPS-II with electromigration fit well in the Kennedy dual-use program, part of NASA’s technology transfer and commercialization effort. The cooperative effort involved Surtreat providing NASA with the corrosion-inhibiting chemical and concrete test slabs, along with technical support as needed. Kennedy provided testing specifications and procedures, then prepared the concrete with the Surtreat chemical and carried out an environmental evaluation of the treatment. Kennedy’s materials scientists reviewed the applicability of the chemical treatment to the electromigration process and determined that it was an effective and environmentally friendly match, suitable for use at the NASA facility.
Ten years later, NASA is still using this combined approach to fight concrete corrosion, and it has also developed a new technology that it believes will further advance these efforts. The technology is a liquid galvanic coating, applied to the outer surface of reinforced concrete, to protect the embedded rebar from corrosion. The coating contains one of several types of metallic particles—magnesium, zinc, or indium. An electrical current established between metallic particles in the applied coating and the surface of the steel rebar produces cathodic protection of the rebar. The current forces a flow of electrons from the coating (anode) to the rebar along a separate metallic connection. This surplus of electrons at the rebar (cathode) prevents the loss of metal ions that would normally occur as part of the natural corrosion process. The technology, made of inexpensive, commercially available ingredients, can be applied to the outside surface of reinforced concrete (most rebar corrosion prevention must be applied directly to the rebar) and with a conventional brush or spray, eliminating the need for expensive, specialized labor.
This new technology is currently in use at Kennedy, but NASA also saw the immediate benefits that could be gained by transferring this technology to the private sector, where decay and corrosion of concrete structures costs billions of dollars per year.
Partnership
Ten years after its initial partnership, Surtreat has partnered with NASA again by licensing the new liquid galvanic coating technology and has already put it to use. Its first test, in early 2007, was completed at the U.S. Army Naha Port, in Okinawa, Japan, a coastal facility built during the Korean War and subject to much of the same environmental stressors as those found at Kennedy.
Product Outcome
The NASA-developed coating may be used to prevent corrosion of steel in concrete in several applications, including highway and bridge infrastructures, piers and docks, concrete balconies and ceilings, parking garages, cooling towers, and pipelines, to name just a few.
Surtreat is the ideal partner to bring this technology to the public, as the company has a proven record of providing full-service, innovative, and technical solutions for the restoration and prevention of deterioration and corrosion in steel-reinforced concrete structures. Their Total Performance System provides diagnostic testing and site analysis to identify the scope of problems for each project, manufactures and prescribes site-specific solutions, controls material application, and verifies performance through follow-up testing and analysis.
The coating lasts 10 years or more, reducing maintenance costs over the lifetime of the structure; and testing has proven that the treatment yields reductions in rebar corrosion potential, water penetration, chemical reactivity, and water-soluble chloride, while generating increases in hardness, flexural strength, and pH levels. The treatment also provides resistance to chloride penetration and problems associated with freezing and thawing of the porous structures.
Surtreat treatments are environmentally friendly, and the company focuses on preventing and minimizing adverse environmental impacts by identifying and controlling potential environmental risks in advance. The solutions used are water-soluble and environmentally safe, and in testing have shown no effect on the turbidity, pH, or dissolved oxygen content levels in water. Surtreat’s formulations bond inorganic compounds to structures, where they become part of the steel and concrete matrix indefinitely. It leaves no residues, coatings, or materials that could potentially harm humans, animals, fish, or the environment.
Total Performance System™ is a trademark of Surtreat International.
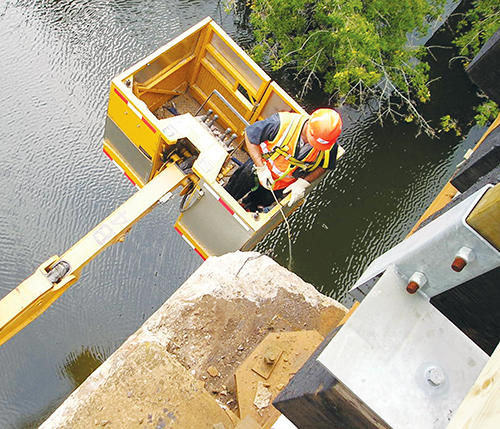
The Surtreat coating is environmentally friendly and lasts 10 years or more, reducing maintenance costs over the lifetime of the structure.
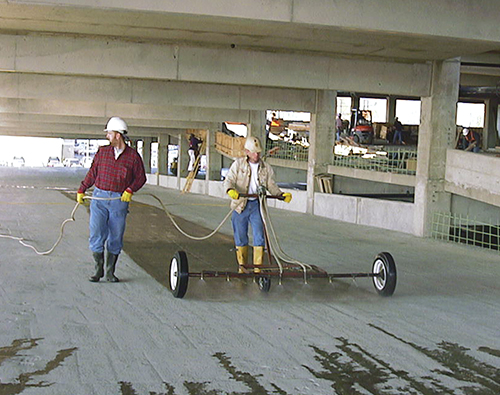
This parking structure was suffering from water and deicing salt infiltration, causing a number of corrosion-related problems throughout the structure. The Surtreat chemicals migrated over 2 inches below the surface, halting corrosion.
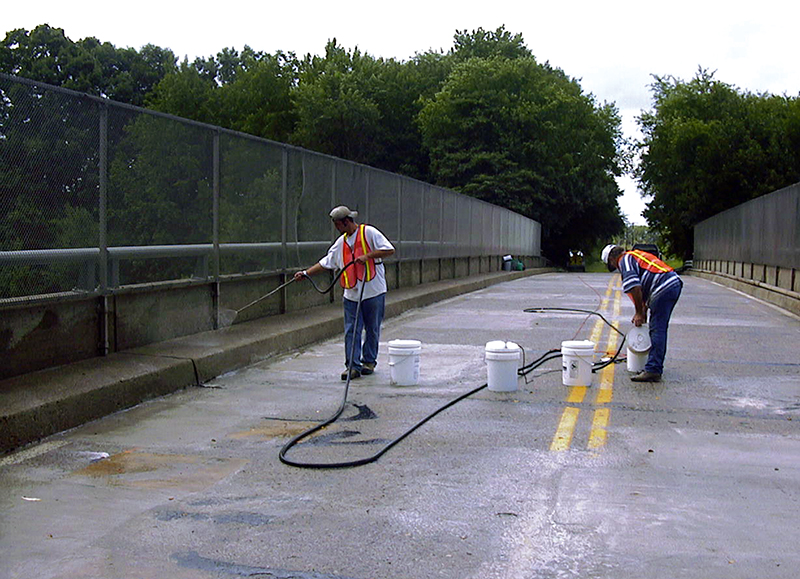
Surtreat uses topically applied, chemically reactive, migrating formulations unique to each project.